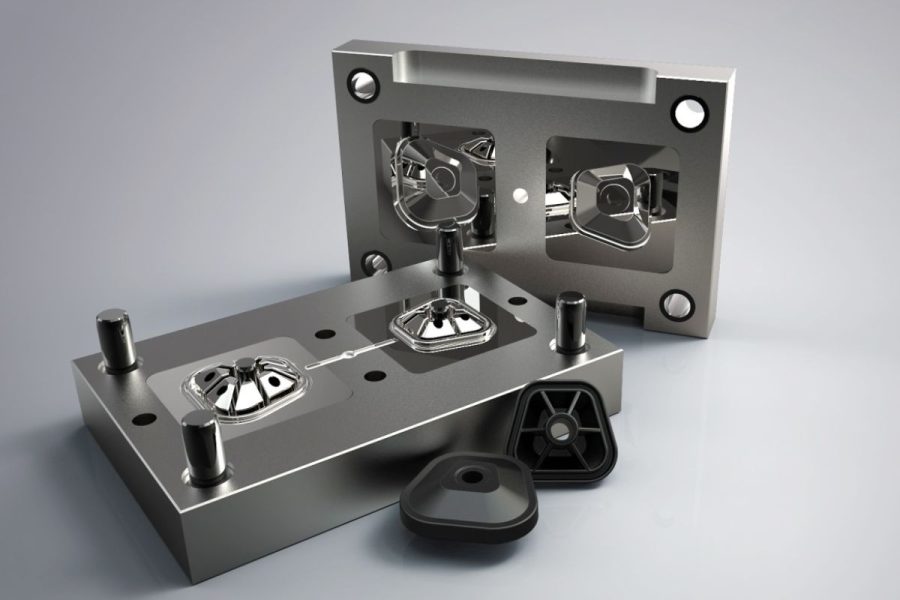
The automotive industry has embraced 3D printing and rapid prototyping as transformative technologies for the design and production of molds and components. These innovations allow manufacturers to accelerate the development cycle, improve design precision, and reduce costs associated with traditional mold-making processes.
3D Printing for Automotive Molds
3D printing, also known as additive manufacturing, enables the creation of molds directly from digital designs without the need for extensive tooling. This approach is particularly advantageous for producing complex geometries and intricate details that are challenging to achieve with conventional methods. Automotive engineers can utilize materials such as high-strength polymers, metal powders, and composites to fabricate molds tailored to specific requirements. The ability to quickly iterate and customize molds reduces lead times and enhances design flexibility.
Rapid Prototyping for Design Validation
Rapid prototyping allows automotive manufacturers to test and validate mold designs before committing to full-scale production. Using 3D printing, prototypes of molds or parts can be created within hours or days, enabling engineers to evaluate fit, form, and function in real-world conditions. This process significantly reduces the risk of errors and costly redesigns in later stages of production.Prototyping also facilitates collaboration between design teams and clients, as physical models provide a tangible representation of the final product. This enhances communication and ensures that designs align with performance expectations and aesthetic requirements.
Benefits of 3D Printing and Rapid Prototyping
- Speed: Traditional mold-making methods can take weeks, while 3D printing and rapid prototyping drastically shorten development timelines.
- Cost Efficiency: The technologies reduce tooling costs, especially for small-batch production or complex designs.
- Design Flexibility: Engineers can experiment with innovative designs, incorporating features like lightweight structures and integrated cooling.
- Sustainability: Additive manufacturing minimizes material waste and energy consumption, aligning with eco-friendly manufacturing goals.
Applications in Automotive Mold Production
3D printing and rapid prototyping are used for producing molds for plastic components, interior panels, and lightweight structural parts. They are also applied in the development of molds for specialty vehicles, motorsport components, and electric vehicle parts, where customization and innovation are critical.