In automotive manufacturing, the demand for high-quality, cost-efficient, and scalable production methods is ever-growing. One of the most effective solutions for achieving these goals is the use of multi-cavity molds in injection molding processes. Multi-cavity molds are essential in the production of automotive components, offering substantial benefits in terms of production efficiency, cost reduction, and consistency in product quality.
1. What Are Multi-Cavity Molds?
A multi-cavity mold is a type of mold that is designed to produce multiple identical parts in a single cycle. Unlike single-cavity molds, which produce only one part per cycle, multi-cavity molds can produce several components simultaneously, typically ranging from two to several dozen cavities, depending on the complexity and size of the part.
These molds are widely used in injection molding processes to manufacture automotive parts, including bumpers, dashboards, interior trims, connectors, housings, and other critical components. The use of multi-cavity molds in automotive manufacturing allows for the efficient production of high volumes of parts, making it ideal for mass production.
2. Benefits of Multi-Cavity Molds in Automotive Manufacturing
a. Increased Production Efficiency
By enabling the production of multiple parts in a single cycle, multi-cavity molds significantly reduce cycle times, boosting overall production output. This is particularly important in the automotive industry, where demand for high-volume parts is a constant. The ability to produce several parts simultaneously allows manufacturers to meet stringent production schedules while minimizing downtime.
b. Cost Savings
The use of multi-cavity molds helps lower the cost per part. With more cavities in a single mold, the cost of producing individual components is reduced due to the economies of scale. In addition, the reduction in cycle time means less time spent per part, further reducing labor and machine operating costs.
c. Improved Part Consistency and Quality
Multi-cavity molds help ensure that all the parts produced are identical in shape and size. The simultaneous production of multiple parts within the same mold under the same conditions reduces variability and improves overall part consistency. This is especially important for automotive components that must meet strict industry standards for performance, safety, and quality.
d. Higher Tool Utilization
Using multi-cavity molds maximizes the use of mold tooling, which is often a significant investment in automotive manufacturing. With multiple cavities, manufacturers can achieve higher output with a single mold, increasing the return on investment (ROI) for mold production.
3. Challenges in Multi-Cavity Mold Design and Manufacturing
a. Complex Mold Design
Designing a multi-cavity mold is more complex than designing a single-cavity mold. Factors such as cavity arrangement, material flow, cooling channels, and gate design must be carefully planned to ensure uniform part quality. Uneven material distribution or cooling can result in defects such as warping, sink marks, or dimensional inaccuracies. Therefore, advanced engineering skills and specialized software are often required to design and simulate multi-cavity molds.
b. Higher Initial Investment
The upfront cost for developing a multi-cavity mold is higher than for a single-cavity mold due to the increased complexity and the need for more advanced tooling and materials. However, this cost is typically offset by the long-term benefits of increased production volume and reduced part costs.
c. Tool Maintenance
With more cavities in a mold, tool maintenance can become more challenging. Regular maintenance and inspections are required to ensure that all cavities are functioning properly and producing parts at the desired quality level. Proper care and maintenance are essential to prevent costly downtime and ensure long-lasting performance of the mold.
4. Applications of Multi-Cavity Molds in Automotive Manufacturing
a. Plastic Automotive Components
Multi-cavity molds are extensively used in the production of plastic components such as bumpers, door panels, grilles, and dashboards. These parts often need to be produced in large volumes to meet the high demands of the automotive market, making multi-cavity molds an ideal solution.
b. Small Precision Parts
Many automotive components, such as connectors, clips, and fasteners, require precise dimensions and are produced in large quantities. Multi-cavity molds are commonly used for these small parts, as they can be produced with high accuracy and in large volumes, which is essential in the automotive sector where space, weight, and cost savings are critical.
c. Injection-Molded Metal Parts (IMD)
Some automotive parts, particularly in high-performance applications, require the use of metal in the injection molding process. Multi-cavity molds can be designed to produce metal inserts or components with precision, benefiting from the higher efficiency and reduced cost per unit that multi-cavity molds provide.
5. Technological Advancements in Multi-Cavity Mold Design
As the automotive industry evolves, so do the technologies used to design and manufacture multi-cavity molds. Advancements in computer-aided design (CAD) software, mold simulation tools, and additive manufacturing have made it easier to optimize mold designs and improve mold performance. Additionally, the use of advanced materials such as high-performance steels and alloys in mold construction has helped increase the durability and lifespan of multi-cavity molds.
6. Conclusion
Multi-cavity molds are a cornerstone of modern automotive manufacturing, offering unmatched production efficiency, cost reduction, and consistency for high-volume parts. Despite the challenges in mold design and initial investment, the long-term benefits make multi-cavity molds an essential tool for mass production. As technological innovations continue to evolve, the use of multi-cavity molds in automotive manufacturing will likely expand further, enabling even greater efficiency and cost-effectiveness in the production of critical automotive components.
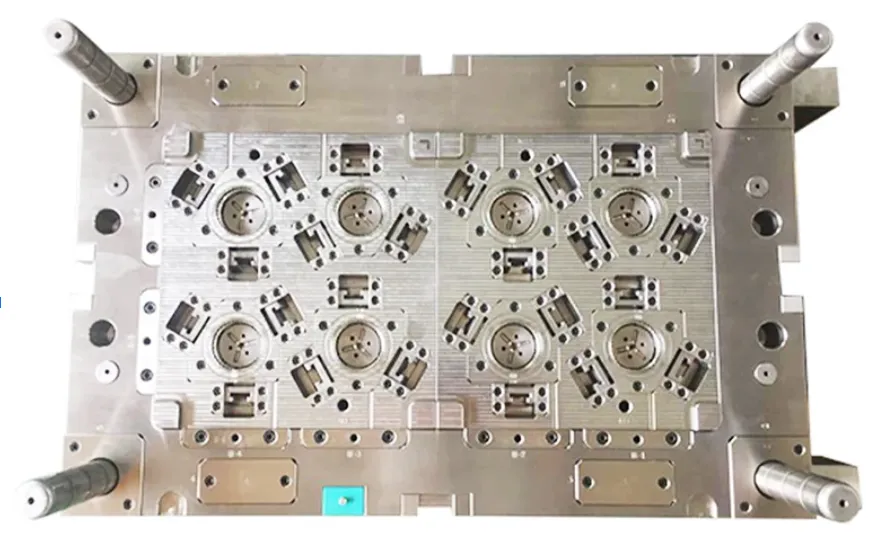