Automotive components exposed to high temperatures—such as those in exhaust systems and engine compartments—demand materials and manufacturing processes that can withstand extreme thermal and mechanical stress. Molding technologies for these parts play a critical role in ensuring durability, performance, and safety in high-heat environments.
Material Requirements for High-Heat Molding
High-temperature automotive applications require molds made from advanced materials that can handle repeated heating and cooling cycles, abrasion, and chemical exposure. Common mold materials include:
Tool Steels (e.g., H13, P20): Known for high thermal fatigue resistance and hardness.
Nickel-Based Alloys (e.g., Inconel): Excellent thermal and oxidation resistance.
Ceramic Molds: Used in investment casting for extremely high-temperature applications.
Thermoplastics used in molding high-heat parts (like engine covers or heat shields) include:
Polyetheretherketone (PEEK)
Polyphenylene sulfide (PPS)
Polyamide-imide (PAI)
High-temperature Nylon (PA 46, PA 6T/6I)
Molding Processes for High-Heat Parts
Injection Molding:
Widely used for under-the-hood plastic parts.
Specialized molds with advanced cooling channels and high-strength steels are used to handle the thermal load.
Compression Molding:
Common for composite engine covers and heat shields.
Suitable for thermosetting plastics reinforced with glass or carbon fibers.
Die Casting:
Used for metal engine parts like cylinder heads, engine blocks, and turbocharger components.
Requires high-temperature resistant molds often cooled actively to manage cycle times.
Investment Casting:
Ideal for complex exhaust components like turbo housings and manifolds.
Uses ceramic molds that are destroyed after each use, allowing for intricate geometries.
Applications in Exhaust and Engine Systems
Exhaust Manifolds: Often require molds that support casting stainless steel or high-nickel alloys for thermal resistance.
Turbocharger Components: Die-cast or investment cast molds used to form high-performance, heat-resistant parts.
Cylinder Heads and Engine Blocks: Cast using permanent steel or sand molds to withstand high thermal gradients and pressures.
Thermal Shields & Engine Covers: Injection molded from heat-resistant thermoplastics with complex mold geometries for precise fitting and performance.
Challenges in High-Heat Molding
Thermal Cycling Fatigue: Molds undergo rapid and repeated temperature changes that can lead to cracking.
Material Degradation: High heat accelerates wear and oxidation in mold materials.
Dimensional Stability: Maintaining precision during thermal expansion and contraction is critical.
Cost: High-performance molds and materials can significantly increase tooling costs.
Innovations and Trends
Additive Manufacturing for Molds: 3D-printed conformal cooling channels improve cycle times and reduce thermal stress.
Coatings and Surface Treatments: PVD/CVD coatings extend mold life by improving heat and corrosion resistance.
Smart Molds: Integration of sensors for real-time temperature and pressure monitoring enhances process control.
Conclusion
Automobile molds for high-heat applications are essential to the performance and longevity of exhaust and engine components. As engine efficiency and emission standards continue to evolve, the demand for more advanced mold materials, precision tooling, and innovative manufacturing techniques will only grow. Partnering with experienced mold manufacturers and staying ahead with new technologies is key to success in this demanding domain.
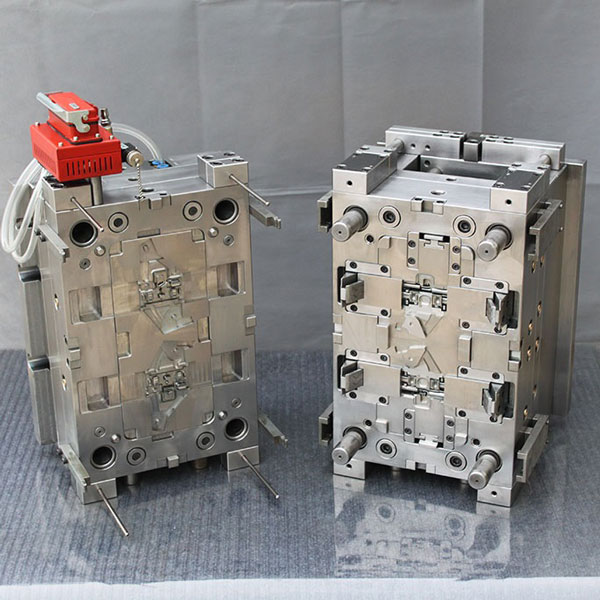