Water and gas-assisted molding technologies are innovative manufacturing methods primarily used to produce hollow or thick-walled plastic parts with improved efficiency and quality. When applied to PVC (Polyvinyl Chloride), these processes offer several benefits in terms of product performance, cost savings, and design flexibility. However, working with PVC in these methods poses unique challenges due to its thermal properties and processing behavior.
What is Gas-Assisted Injection Molding (GAIM)?
Gas-assisted injection molding involves injecting an inert gas—usually nitrogen—into the molten polymer during or after the injection phase. The gas pushes the plastic against the mold walls, creating hollow sections and reducing part weight.
Advantages in PVC Applications:
Reduces material usage by forming hollow sections.
Minimizes warpage and sink marks in thick-walled parts.
Enhances surface finish and dimensional stability.
Shortens cooling and cycle times.
What is Water-Assisted Injection Molding (WAIM)?
Water-assisted molding operates on a similar principle as gas-assisted molding but uses water instead of gas. Water has a much higher heat transfer rate than gas, which significantly improves cooling efficiency.
Benefits for PVC:
Faster cooling and cycle time reduction (compared to gas).
Improved internal surface quality.
More efficient for larger hollow channels.
Reduced stress and deformation in the molded part.
Challenges of Using These Techniques with PVC
PVC is a thermally sensitive material and degrades at relatively low temperatures, releasing corrosive gases like HCl. This makes high-temperature processing risky. Additionally, PVC has a higher viscosity compared to other thermoplastics, making flow and gas/water penetration more difficult.
Considerations:
Temperature Control: Precise control is needed to avoid thermal degradation.
Mold Design: Needs to be optimized for even flow and cooling.
Material Formulation: Use of stabilized PVC grades suitable for high-pressure processes.
Corrosion Resistance: Equipment and molds must resist chemical attack from PVC byproducts.
Process Flow (Generalized for PVC Products)
Injection Phase: Molten PVC is partially or fully injected into the mold.
Gas/Water Penetration: After a short delay, gas or water is injected through a core pin or special nozzle to create internal channels.
Holding Phase: The fluid maintains pressure while the part cools.
Cooling and Ejection: For WAIM, water is removed; then, the part is ejected.
Applications of GAIM and WAIM in PVC Products
Piping Systems: Lightweight hollow pipes and fittings.
Automotive Components: Door handles, ducts, and trims.
Consumer Products: Furniture, appliances, and sporting goods.
Medical Devices: Lightweight housing and complex profiles.
Building Materials: Hollow window profiles, cable ducts, and wall panels.
Conclusion
Water and gas-assisted molding technologies offer significant advantages for manufacturing complex and lightweight PVC products. While PVC presents unique processing challenges due to its sensitivity to heat and corrosion, with the right equipment and formulation, these techniques can enhance productivity, reduce costs, and enable innovative designs. Continuous development in mold design, processing control, and material stabilization is expanding the potential of these advanced molding technologies in PVC applications.
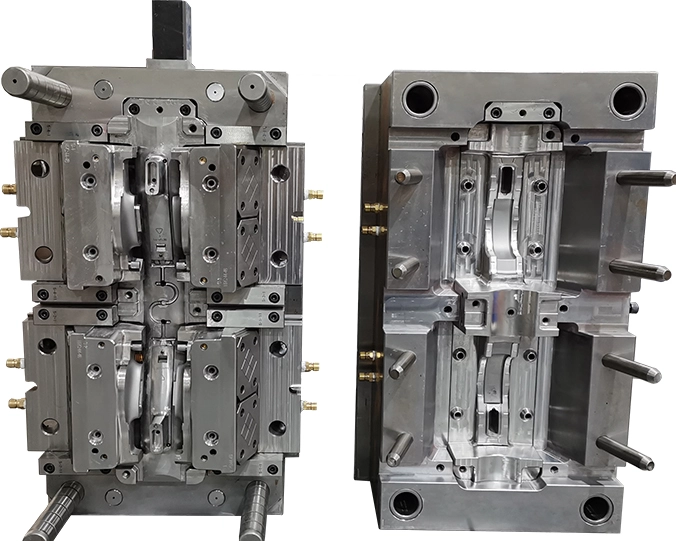