In the competitive world of automotive manufacturing, efficiency is everything. High-volume production environments must maintain rapid, consistent output without sacrificing quality. One of the most critical metrics in achieving this balance is cycle time — the total time required to complete one unit of a product, from start to finish.
Why Cycle Time Matters
Cycle time directly impacts:
Production throughput
Cost-efficiency
Lead times
Customer satisfaction
Overall equipment effectiveness (OEE)
By optimizing cycle time, manufacturers can produce more parts in less time, reduce waste, and improve profitability — all while maintaining rigorous quality standards.
Key Strategies for Cycle Time Optimization
1. Value Stream Mapping (VSM)
Create a detailed map of the current production process to identify bottlenecks, redundancies, and non-value-added steps. VSM helps visualize where cycle time is being lost.
2. Standardization of Workflows
Consistency in task execution minimizes variability. Develop standardized work instructions, especially for repetitive manual tasks, and train operators to follow them strictly.
3. Automation & Robotics
Deploying industrial robots, cobots, and automated material handling systems can significantly reduce cycle times in operations like:
Welding
Painting
Assembly
Inspection
Automation not only increases speed but also enhances precision and repeatability.
4. Tooling and Fixture Optimization
Quick-change tooling systems and ergonomic fixture designs reduce setup time and minimize operator movement, directly improving cycle times.
5. Real-Time Data Monitoring
Use IoT sensors and manufacturing execution systems (MES) to collect and analyze cycle time data in real-time. This allows teams to:
Detect deviations immediately
Pinpoint slowdowns
Take corrective action faster
6. Lean Manufacturing Principles
Apply lean tools like:
5S (Sort, Set in order, Shine, Standardize, Sustain)
Kaizen (continuous improvement)
SMED (Single-Minute Exchange of Die)
Poka-yoke (error-proofing)
These reduce inefficiencies and ensure optimal flow in high-volume settings.
7. Preventive Maintenance
Unplanned equipment downtime can spike cycle times. A proactive maintenance program ensures machines run at peak efficiency and avoids process interruptions.
8. Operator Training and Engagement
Skilled and empowered operators can identify inefficiencies, suggest improvements, and maintain a high level of performance. Cross-training also ensures flexibility in staffing.
Case Example: Cycle Time Reduction in Stamping Line
A Tier 1 automotive supplier reduced cycle time on a stamping line by 18% through:
Upgrading die change mechanisms (SMED implementation)
Introducing a predictive maintenance system
Training operators on best practices
Adjusting material flow to reduce transit delays
This resulted in a 12% increase in daily output and a significant reduction in overtime costs.
Conclusion
Optimizing cycle time in high-volume automotive part production is not a one-time fix — it’s a continuous effort involving people, process, and technology. By systematically identifying and eliminating delays, waste, and inefficiencies, manufacturers can achieve greater agility, reduce costs, and stay competitive in an increasingly demanding market.
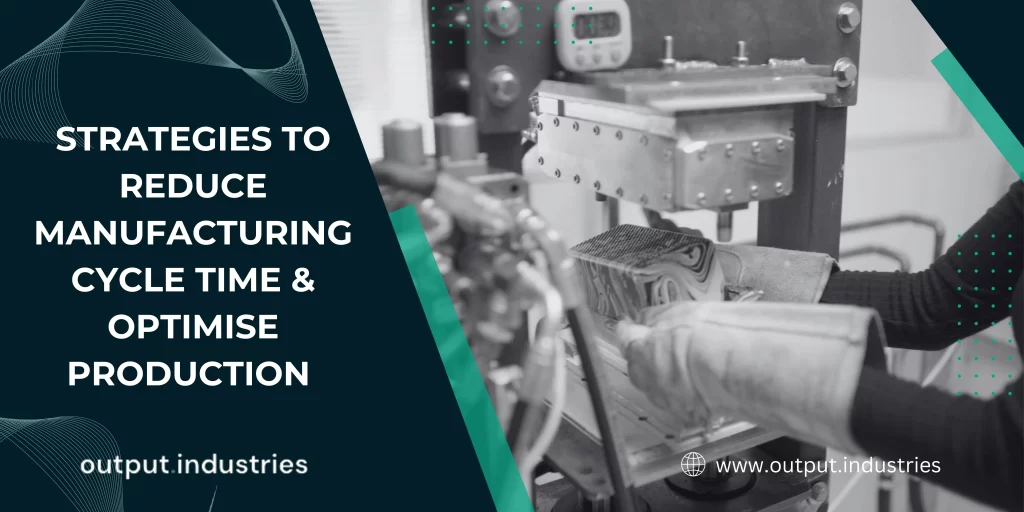