When working on a molding project, choosing the correct grade of PVC (Polyvinyl Chloride) is essential to ensure durability, performance, and cost-effectiveness. PVC is one of the most versatile thermoplastics, and it comes in various grades, each tailored for specific applications. Here’s a comprehensive guide to help you choose the right PVC grade for your project.
1. Understand the Two Main Types of PVC
PVC is generally available in two basic forms:
a. Rigid PVC (uPVC)
Characteristics: Hard, strong, and resistant to impact and chemicals.
Best For: Pipe fittings, profiles, window frames, and structural components.
Advantages: Good dimensional stability, flame resistance, and excellent weatherability.
b. Flexible PVC
Characteristics: Softer and more pliable due to added plasticizers.
Best For: Wire and cable insulation, flexible tubing, medical bags, toys.
Advantages: High flexibility, chemical resistance, and ease of processing.
2. Know Your Application Requirements
Consider the following factors to determine the best PVC grade:
Mechanical Strength – For load-bearing parts, go with rigid PVC.
Flexibility – For parts that need bending or flexing, use flexible PVC.
Thermal Resistance – Some grades withstand higher temperatures better.
Chemical Exposure – Check resistance to acids, alkalis, oils, or solvents.
Outdoor Use – Choose UV-stabilized grades for sunlight exposure.
Food or Medical Use – Use FDA or medical-grade PVC, which are formulated to meet health and safety standards.
3. Choose from Specialty PVC Grades
Depending on the project’s needs, consider these specific PVC variants:
High Impact PVC – Enhanced with modifiers for applications requiring extra durability (e.g., outdoor enclosures).
Clear PVC – Ideal for applications where visibility is important, like packaging or display products.
CPVC (Chlorinated PVC) – Suitable for high-temperature applications (up to ~200°F or 93°C), like hot water pipes.
Medical Grade PVC – Meets biocompatibility standards; used in IV bags, tubing, and catheters.
Food Grade PVC – Compliant with FDA regulations; used in food packaging and processing equipment.
4. Molding Process Compatibility
Ensure the PVC grade is compatible with your molding process:
Injection Molding – Most rigid and some flexible PVCs work well. Choose a grade with good flow characteristics.
Blow Molding – Flexible PVC grades are commonly used.
Extrusion Molding – Rigid and flexible PVCs can both be used, depending on the product being extruded.
5. Check for Additives
PVC can be compounded with various additives to enhance performance:
Stabilizers – Improve heat and UV resistance.
Plasticizers – Increase flexibility in soft PVC.
Lubricants – Enhance processability during molding.
Flame Retardants – Improve fire resistance in electrical applications.
6. Work with Reputable Suppliers
Choose a reliable material supplier who can provide:
Data sheets and technical support
Consistent material quality
Custom formulations if needed
Conclusion
Selecting the right PVC grade for your molding project involves understanding your application requirements, the type of PVC best suited for it, and the performance characteristics you need. Whether you’re creating medical components, construction parts, or consumer goods, choosing the right PVC can lead to better product performance, longevity, and regulatory compliance.
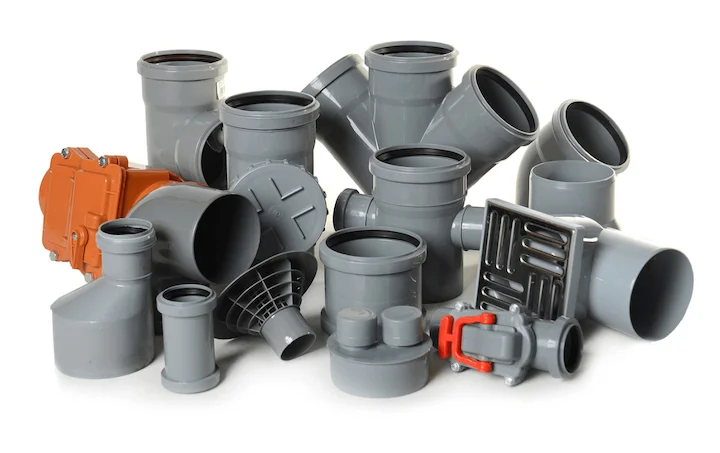