The manufacturing world is evolving rapidly, and the PVC molding industry is no exception. Automation, once a futuristic concept, is now at the heart of modern production lines. By integrating advanced machinery, robotics, and smart control systems, automation is revolutionizing the way PVC (polyvinyl chloride) products are molded — boosting efficiency, improving consistency, and lowering costs.
1. Improved Precision and Consistency
Automation reduces the reliance on manual processes, which are often prone to errors and inconsistencies. In PVC molding, precision is crucial — even minor flaws can lead to defective parts or product rejection. Automated machines use precise temperature controls, mold pressure regulation, and timing mechanisms to ensure every cycle yields identical, high-quality products.
2. Increased Production Speed
Automated PVC molding systems can run continuously with minimal downtime, far outpacing traditional manual processes. Robotic arms and conveyors handle tasks like loading, unloading, trimming, and inspection, significantly speeding up the production cycle. This efficiency allows manufacturers to scale operations and meet high-volume demands with ease.
3. Enhanced Safety
PVC molding involves exposure to high temperatures and sometimes hazardous chemicals. Automation minimizes human interaction with potentially dangerous processes. By assigning these tasks to machines, manufacturers improve worker safety while ensuring compliance with health and safety regulations.
4. Cost Efficiency Over Time
While the initial investment in automation can be significant, the long-term cost savings are substantial. Reduced labor costs, lower defect rates, and minimized material waste all contribute to a lower cost per unit. Additionally, predictive maintenance systems help prevent costly downtime by alerting operators to potential issues before failures occur.
5. Smart Monitoring and Quality Control
Modern automated molding machines come equipped with sensors, AI algorithms, and IoT integration, enabling real-time monitoring of every aspect of the production process. These systems can detect anomalies, log performance data, and even self-adjust parameters to maintain optimal conditions — all contributing to higher quality and reduced waste.
6. Flexibility and Customization
Automation doesn’t mean rigidity. With programmable logic controllers (PLCs) and adaptive software, automated PVC molding systems can quickly switch between product designs or specifications. This flexibility is especially valuable for custom molding jobs and low- to mid-volume production runs.
7. Sustainability and Waste Reduction
PVC molding traditionally generates scrap and off-spec material, but automation helps minimize this through precise control and efficient material usage. Some systems even integrate with recycling units to reprocess scrap on-site. This not only cuts costs but also supports environmental sustainability efforts.
Final Thoughts
Automation is not just transforming PVC molding — it’s redefining it. From reducing errors and improving product quality to enhancing worker safety and boosting output, the benefits are clear. As technology continues to evolve, manufacturers who embrace automation will find themselves better equipped to meet growing demand, stay competitive, and deliver superior products.
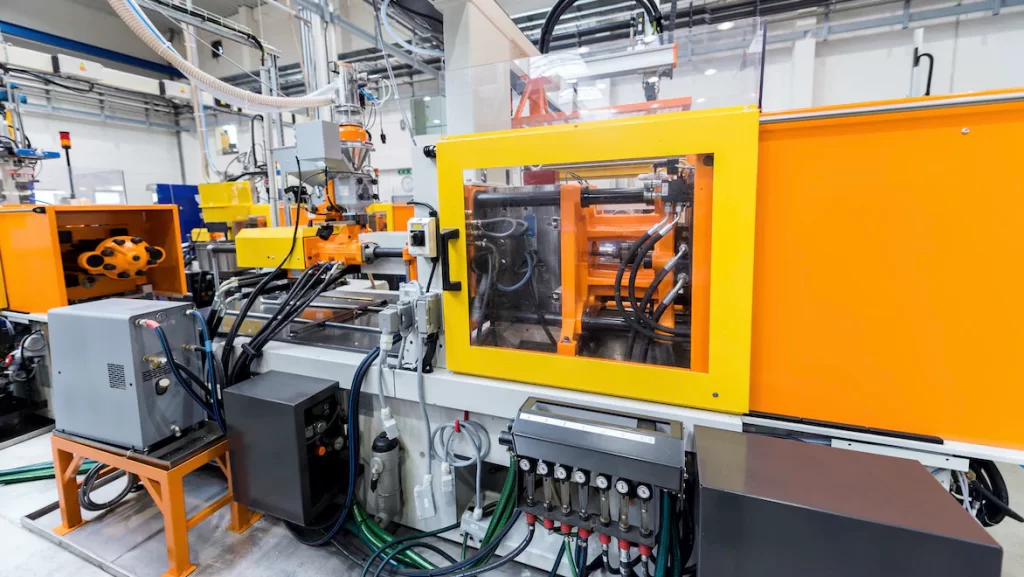