The rapid evolution of autonomous vehicles (AVs) has led to significant changes in the design, materials, and manufacturing processes of automotive components. Among these, injection molding remains a cornerstone technology, but it’s being reshaped by the unique demands of self-driving cars. Here are the key trends in injection molding for AV parts:
1. Shift Toward High-Performance Polymers
Autonomous vehicles rely heavily on sensors, cameras, and advanced electronic systems. These components require housings and support structures that are lightweight yet durable.
High-Temperature and Chemical Resistance: Materials like PEEK, PPS, and LCP are gaining popularity for their performance under harsh conditions.
EMI Shielding: To prevent electromagnetic interference with sensors and electronic systems, polymers are now being blended with conductive additives.
2. Integration of Functional Components
Injection molding is increasingly used to integrate mechanical and electronic functions into a single part—often called “smart parts” or “insert-molded electronics”.
Overmolding and Insert Molding: These processes allow sensors, connectors, and wiring to be embedded directly into plastic parts.
Multi-material molding: Combines flexible and rigid materials for more complex designs, essential for sensor housings and interior interfaces.
3. Precision and Micro-Molding
Autonomous systems require highly accurate components, especially in lidar, radar, and camera mounts.
Tight Tolerances: Micro-molding enables the creation of parts with micro-scale features.
Advanced Mold Design: Use of simulation software to optimize flow, reduce warpage, and ensure dimensional accuracy.
4. Lightweighting for Energy Efficiency
Reducing vehicle weight is critical for improving the range and efficiency of electric autonomous vehicles.
Fiber-Reinforced Plastics: Glass or carbon fiber-reinforced polymers offer strength comparable to metals with much less weight.
Topology Optimization: Design for injection molding now leverages AI-driven topology optimization to create lightweight yet structurally sound components.
5. Sustainable Materials and Processes
Sustainability is becoming a non-negotiable aspect of automotive manufacturing.
Bio-based and Recycled Polymers: The use of sustainable resins is increasing, including PA11 (bio-based) and recycled PET blends.
Waste Reduction: Advanced molding techniques like hot runner systems and in-process recycling help minimize material waste.
6. Increased Use of Automation and Smart Manufacturing
To meet the high precision and volume demands of AV parts, manufacturers are embracing Industry 4.0 practices.
Real-Time Monitoring and Quality Control: Sensors in the mold monitor temperature, pressure, and fill speed.
AI & Machine Learning: Algorithms predict defects and suggest corrective actions in real time.
7. Customization for Sensor and Camera Integration
AVs require various externally mounted sensors, and these parts must be highly customizable.
UV and Weather Resistance: Parts must withstand outdoor exposure, especially for external camera and lidar housings.
Aesthetic and Aerodynamic Design: Molded parts must meet both technical and design specifications for minimal drag and visual appeal.
Conclusion
The injection molding industry is at the forefront of supporting the autonomous vehicle revolution. With advances in materials, process automation, and design flexibility, injection molding is more relevant than ever in producing lightweight, complex, and highly functional parts essential for AV systems.
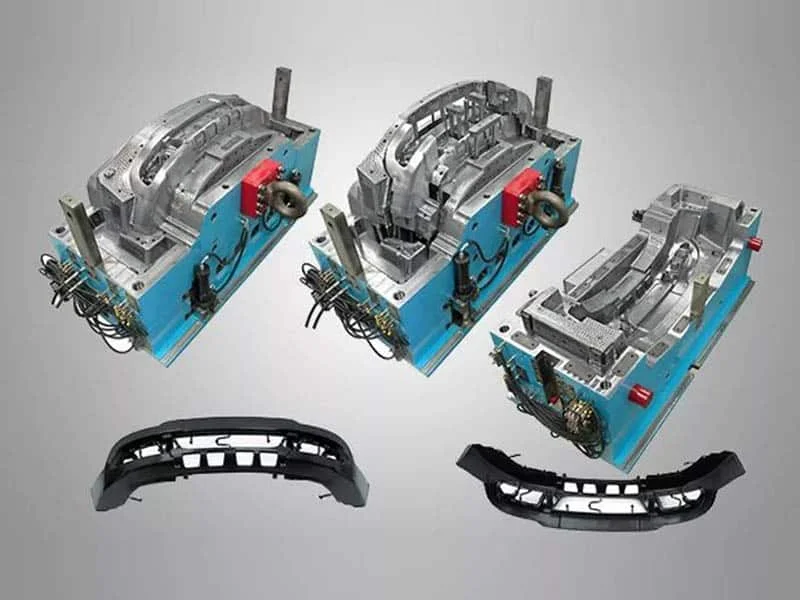