PVC (Polyvinyl Chloride) foam molding is a versatile manufacturing technique used to create lightweight, durable, and cost-effective components. It involves processing PVC material into a foam structure, making it ideal for a wide range of industrial and commercial applications. The resulting product is strong yet lightweight, resistant to moisture, and easy to fabricate.
Applications of PVC Foam Molding
PVC foam molded products are used across various sectors due to their unique properties. Common applications include:
Construction Industry
Wall panels
Ceiling tiles
Decorative moldings and trims
Door and window frames
Automotive Sector
Interior panels
Dashboard components
Soundproofing and thermal insulation parts
Signage and Display
Advertising boards
Exhibition panels
Point-of-sale displays
Furniture and Interior Design
Cabinetry panels
Furniture decorative elements
Lightweight shelves
Marine Applications
Boat interiors
Deck panels
Insulating elements
PVC foam is valued for its resistance to moisture, chemicals, and UV radiation, making it especially useful in environments with variable exposure conditions.
PVC Foam Molding Process
The process of molding PVC foam typically involves the following steps:
Material Preparation
PVC resin is mixed with additives including plasticizers, stabilizers, foaming agents (usually chemical blowing agents), lubricants, and fillers.
The specific formulation varies depending on the desired product properties.
Extrusion or Molding
The compound is heated and fed into an extruder or molding machine.
Heat activates the foaming agent, causing it to release gas and create a cellular (foam) structure within the PVC.
Shaping
For extrusion: The material is pushed through a die to form sheets, panels, or profiles.
For molding: The foamed PVC is injected or pressed into a mold to form a specific 3D shape.
Cooling and Solidification
The shaped foam is cooled in a controlled manner to stabilize its dimensions and mechanical properties.
Finishing
The final product may undergo cutting, lamination, surface texturing, painting, or bonding to other materials.
Precision trimming ensures clean edges and adherence to design specifications.
Advantages of PVC Foam Molding
Lightweight but durable
Moisture and corrosion resistant
Excellent thermal and acoustic insulation
Cost-effective for mass production
Easy to fabricate, cut, and install
Environmentally friendly (recyclable formulations available)
Conclusion
PVC foam molding is a critical process in modern manufacturing, offering a sustainable and flexible solution for various design and engineering challenges. Its balance of physical properties and affordability ensures continued growth in diverse sectors such as construction, automotive, and signage.
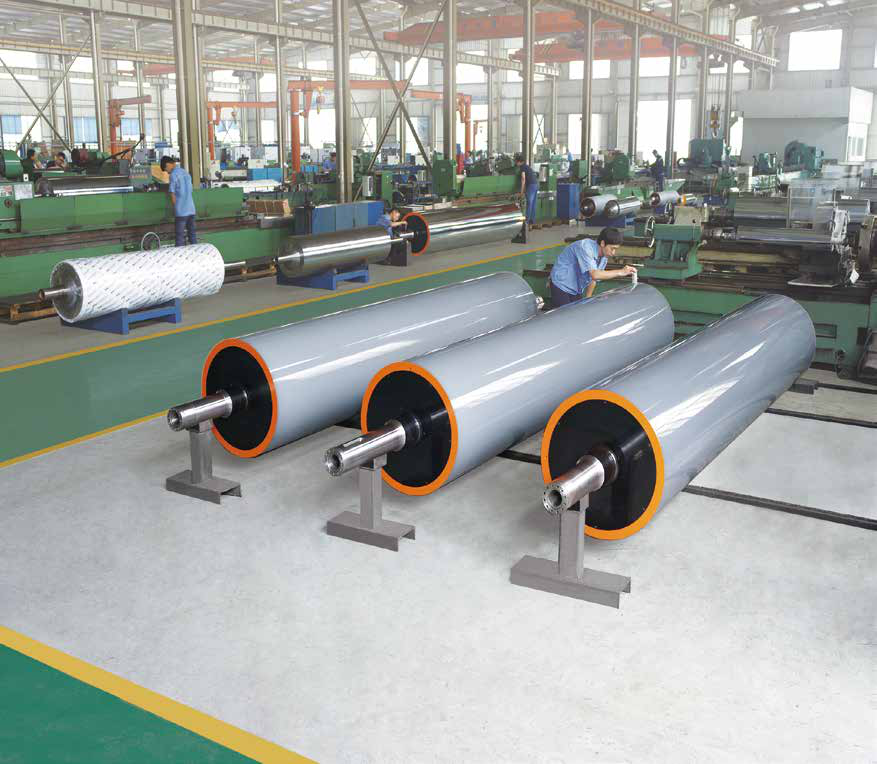