Polyvinyl Chloride (PVC) is a widely used thermoplastic polymer known for its durability, chemical resistance, and versatility. With advances in molding technologies, manufacturers can now produce more complex, precise, and high-performance PVC parts across industries such as automotive, healthcare, construction, and consumer goods.
Advanced PVC molding technologies include innovations in equipment, materials, process optimization, and automation. These advancements improve efficiency, product quality, and environmental sustainability.
1. High-Precision Injection Molding
Definition:
A method where molten PVC is injected into a mold cavity under high pressure.
Advancements:
Use of servo-driven hydraulic systems for better control and energy efficiency.
Integration of multi-cavity molds for high-volume production.
Development of low-shear screws specifically designed for PVC to minimize degradation.
Closed-loop control systems to ensure consistency in shot size, pressure, and temperature.
Applications:
Medical device components, plumbing fittings, and electrical housings.
2. Micro Injection Molding
Definition:
A specialized form of injection molding used to create extremely small, precise PVC parts.
Advancements:
Miniaturized mold and barrel designs.
Enhanced thermal management systems for tight temperature control.
Application of precision robotics for part handling.
Applications:
Micro-valves, connectors, and tiny enclosures for electronics.
3. Gas-Assisted Injection Molding (GAIM)
Definition:
Involves injecting gas (usually nitrogen) into the molten PVC during molding to create hollow sections.
Benefits:
Reduces material usage and weight.
Improves dimensional stability and surface quality.
Shortens cooling times.
Applications:
Handles, frames, and automotive trim components.
4. Co-Injection (Multi-Material) Molding
Definition:
Simultaneous injection of two different PVC formulations or PVC with another compatible material.
Advancements:
Precision layering for dual-hardness parts.
Barrier layer integration for chemical resistance.
Applications:
Soft-touch grips, seals with rigid cores, and multi-functional medical parts.
5. PVC Blow Molding (Extrusion and Injection Blow Molding)
Extrusion Blow Molding:
Used for hollow objects like bottles and containers.
Advanced die design for uniform wall thickness.
Injection Blow Molding:
Greater dimensional accuracy for smaller containers.
Improved surface finish and consistency.
Advancements:
3D blow molding for complex shapes.
Inline quality inspection systems.
6. Precision Compression Molding
Definition:
Preheated PVC is placed into a heated mold and compressed to form the part.
Key Innovations:
Use of thermosetting PVC compounds for high-heat resistance.
Enhanced mold designs for better material flow and pressure distribution.
Applications:
Electrical insulators, gaskets, and high-strength structural components.
7. 3D Printing with PVC-Based Materials
Emerging Trend:
Though still under research, modified PVC filaments are being used in additive manufacturing.
Offers rapid prototyping for PVC-like products.
Challenges:
PVC’s chlorine content requires special handling due to potential emissions.
8. Automation & Industry 4.0 Integration
Features:
Real-time monitoring with IoT-enabled sensors.
Predictive maintenance and process optimization using AI and machine learning.
Automated material handling and quality control systems.
9. Sustainability Innovations
Development of non-phthalate plasticizers.
Use of recycled PVC in closed-loop manufacturing.
Energy-efficient molding machines and waste heat recovery systems.
Conclusion
Advanced PVC molding technologies are shaping the future of plastic manufacturing by enabling greater product complexity, reducing costs, and meeting strict regulatory and environmental standards. As material science and automation continue to evolve, the potential for PVC-based innovations will expand across numerous sectors.
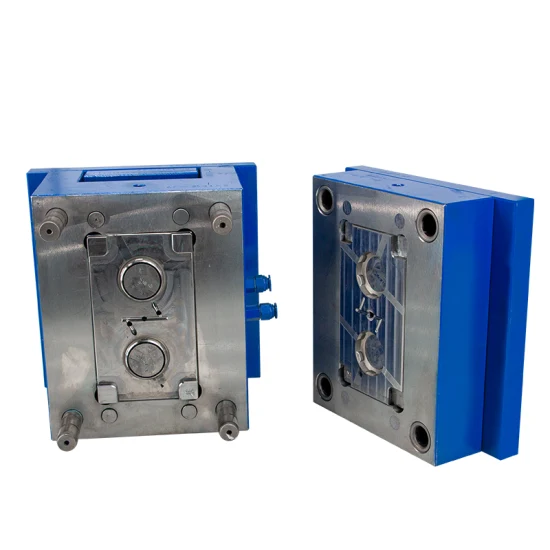