The automotive industry is undergoing a significant transformation driven by Industry 4.0, which is characterized by the integration of smart technologies, data analytics, and automation into manufacturing processes. Automotive molding—a critical component of vehicle production—is no exception. As vehicle designs become more complex and demand for customization increases, molding technologies are evolving to meet the challenges of cost efficiency, precision, and sustainability.
1. Smart and Connected Molding Systems
Industry 4.0 emphasizes connectivity through the Internet of Things (IoT). In automotive molding, sensors and embedded devices are being increasingly used to monitor temperature, pressure, and material flow in real time. This allows for predictive maintenance, reduced downtime, and enhanced process control, improving overall quality and throughput.
2. Digital Twins and Simulation
Digital twin technology is enabling manufacturers to create a virtual replica of the molding process. These simulations help in optimizing design, material selection, and process parameters before actual production begins. This reduces trial-and-error iterations, saves time, and ensures higher first-pass yield.
3. Additive Manufacturing (3D Printing) Integration
Additive manufacturing is being used for prototyping and even small-batch production of molded parts. With rapid design-to-part capabilities, automotive companies can test and validate parts much faster. It also allows for greater design freedom, lightweight structures, and the integration of multiple functions into a single molded part.
4. Advanced Materials and Sustainability
The push toward electric vehicles (EVs) and sustainability is leading to the development and use of recyclable and lightweight composite materials in molding. These materials help improve fuel efficiency and reduce emissions. Industry 4.0 facilitates better material tracking and lifecycle management through data integration.
5. AI and Machine Learning in Process Optimization
Machine learning algorithms analyze large datasets from molding machines to identify patterns and anomalies. This leads to better process optimization, defect prediction, and quality control. AI-driven decision-making reduces human error and supports more agile and responsive manufacturing operations.
6. Customization and Flexibility
With consumers demanding more personalized vehicles, automotive molding must adapt to produce more variants without sacrificing efficiency. Smart factories powered by Industry 4.0 technologies enable quick changeovers, modular tooling, and mass customization capabilities.
7. Human-Machine Collaboration
Collaborative robots (cobots) are being integrated into molding lines to work alongside human operators. These systems enhance productivity and safety while handling complex or repetitive tasks. Augmented reality (AR) is also being used for training and maintenance support.
8. Data-Driven Quality Assurance
Real-time data collection and analysis from each stage of the molding process allow for immediate detection and correction of defects. Industry 4.0 makes it possible to implement closed-loop feedback systems, ensuring consistent part quality and reducing waste.
Conclusion
The future of automotive molding is being reshaped by Industry 4.0 technologies. As the industry moves toward smarter, more flexible, and sustainable manufacturing models, companies that embrace these advancements will be better positioned to meet evolving market demands and remain competitive. The convergence of digital tools, automation, and materials innovation is not just enhancing how parts are made—but redefining what is possible in automotive design and production.
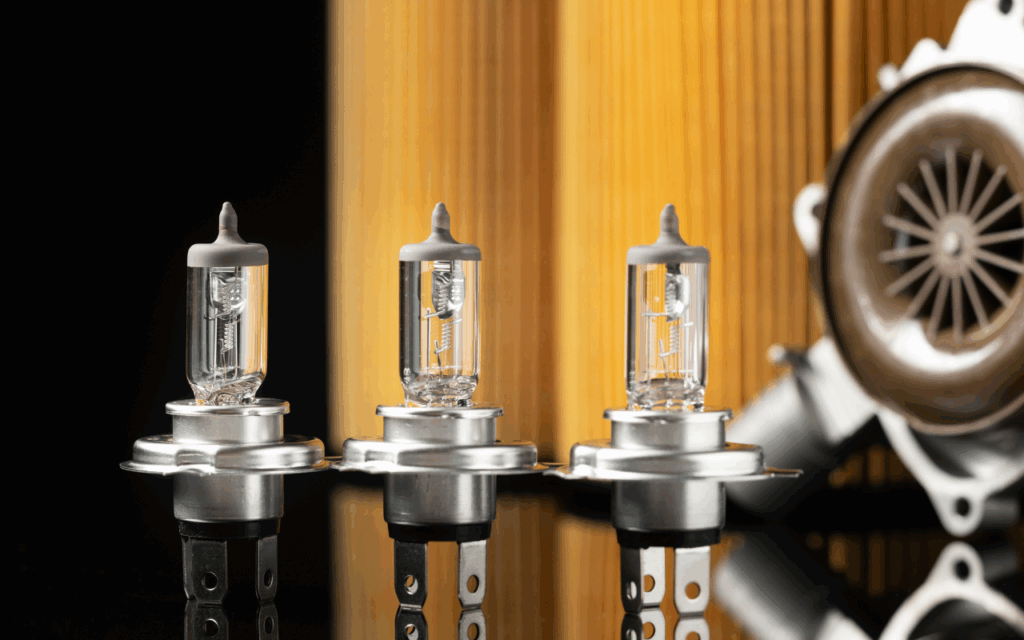