Automotive mold engineering is a specialized field of manufacturing engineering that focuses on the design, development, and production of molds used to create plastic and metal components in the automotive industry. These molds are crucial for producing parts with high precision, consistency, and durability in large volumes.
Importance in the Automotive Industry
Modern vehicles consist of thousands of individual components, many of which are produced using molding processes such as injection molding, die casting, and compression molding. Mold engineering ensures that these parts meet strict automotive standards for safety, performance, and aesthetics.
Key Components of Automotive Mold Engineering
1. Design and Development
CAD Modeling: Engineers use Computer-Aided Design (CAD) tools to model the part and the corresponding mold.
Simulation: Software like Moldflow or ANSYS is used to simulate the mold filling, cooling, and warping process.
DFM (Design for Manufacturability): The mold is designed for ease of manufacturing and cost-efficiency.
2. Material Selection
Mold materials: Tool steel, aluminum, or other high-durability alloys.
Component materials: Thermoplastics (e.g., ABS, PP), thermosets, or lightweight metal alloys (e.g., magnesium, aluminum).
3. Mold Fabrication
CNC Machining
Electrical Discharge Machining (EDM)
Surface finishing and polishing
Hardening and heat treatment
4. Types of Molds in Automotive Applications
Injection Molds: Used for plastic components such as dashboards, bumpers, and door panels.
Compression Molds: Often used for rubber parts like seals and gaskets.
Die Casting Molds: Used for metal parts like engine blocks and transmission cases.
Applications in Automotive Components
Interior Parts: Instrument panels, seat components, air vents
Exterior Parts: Bumpers, grilles, light housings
Engine Components: Cylinder heads, manifolds
Structural Parts: Cross-members, supports
Challenges in Automotive Mold Engineering
Tight tolerances and complex geometries
High production volumes requiring durable molds
Shorter product development cycles
Integration of advanced materials and lightweighting goals
Adapting to electric vehicle (EV) component requirements
Advancements and Trends
3D Printing in Mold Making: Used for prototyping and even final mold inserts.
Smart Molds: Integration of sensors for real-time monitoring.
High-speed Machining: Reduces mold production time.
Sustainable Materials: Recyclable plastics and bio-composites.
Modular Mold Systems: Reduce cost and increase flexibility in production lines.
Conclusion
Automotive mold engineering is a cornerstone of modern vehicle manufacturing. It blends advanced design, precision tooling, and high-performance materials to meet the evolving demands of the automotive sector. As vehicles become smarter and more sustainable, mold engineering continues to evolve to support innovation in design, function, and efficiency.
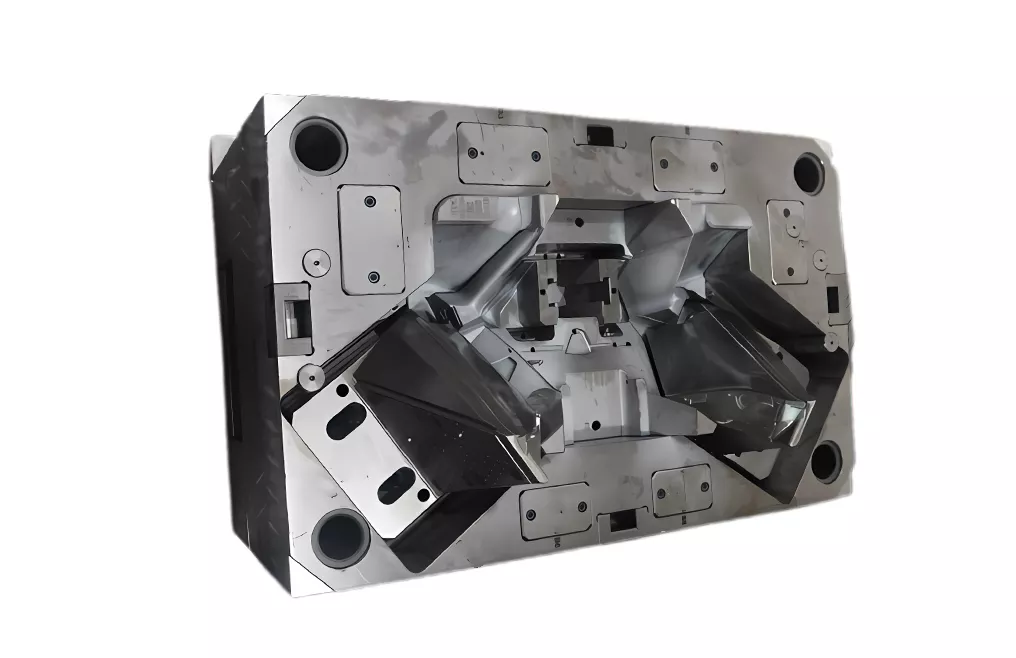