High-temperature plastics, also known as high-performance polymers, are materials engineered to withstand extreme heat without losing their mechanical integrity. In injection molding, these plastics are used for applications where traditional polymers would fail due to thermal degradation.
Key Properties
High-temperature plastics are characterized by:
Heat resistance: Capable of maintaining strength and stability at temperatures above 250°C (482°F).
Chemical resistance: Resistant to solvents, acids, and bases.
Dimensional stability: Minimal expansion or deformation under thermal stress.
Flame retardance: Often self-extinguishing and compliant with fire safety standards.
Wear and fatigue resistance: Ideal for high-load or high-cycle environments.
Common High-Temperature Plastics
PEEK (Polyetheretherketone)
Glass transition temperature: ~143°C
Continuous use temp: ~250°C
Excellent chemical resistance and mechanical strength.
PPS (Polyphenylene Sulfide)
Glass transition temperature: ~90°C
Continuous use temp: ~220°C
Flame retardant and dimensionally stable.
PEI (Polyetherimide, e.g., Ultem®)
Glass transition temperature: ~217°C
Continuous use temp: ~170–200°C
High strength, rigidity, and transparency.
PES (Polyethersulfone)
Continuous use temp: ~180–200°C
Known for toughness and hydrolytic stability.
LCP (Liquid Crystal Polymer)
Excellent for thin-walled parts with complex geometries
High flow and heat resistance up to 240°C.
PTFE (Polytetrafluoroethylene)
Use temp up to 260°C
Extremely low friction and excellent chemical resistance.
Benefits of High-Temperature Plastics in Injection Molding
Lightweight alternative to metals
Lower cost of production compared to machining metals
Reduced component wear and increased lifespan
Design flexibility with complex geometries and tight tolerances
Compliance with stringent industry standards (e.g., aerospace, automotive, medical)
Challenges and Considerations
Higher processing temperatures: Requires specialized tooling and equipment.
Material cost: Significantly higher than standard plastics.
Tooling wear: High temperatures and filled resins can wear down molds.
Shrinkage and warpage: Requires precise mold design and process control.
Applications
Aerospace: Components for aircraft engines, interiors, and structural parts.
Automotive: Under-the-hood components, electrical connectors, and fuel system parts.
Medical devices: Sterilizable surgical instruments and dental tools.
Electronics: High-performance connectors, insulators, and circuit components.
Industrial: Pumps, valves, and components exposed to high heat or chemicals.
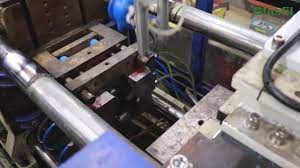