The automotive industry is undergoing rapid transformation, driven by demands for higher performance, sustainability, safety, and cost-efficiency. One area seeing significant innovation is molding technology—particularly with the integration of smart manufacturing principles. Smart molding refers to the use of advanced materials, real-time monitoring, data analytics, and automation in the molding process to enhance quality, reduce waste, and improve production efficiency.
1. What is Smart Molding?
Smart molding technologies combine traditional molding techniques (like injection molding, compression molding, and blow molding) with:
Sensors and IoT devices for process monitoring
Machine learning and AI for process optimization
Digital twins for simulation and predictive maintenance
Advanced materials such as lightweight composites or bio-based polymers
2. Key Smart Molding Technologies in Automotive Manufacturing
a. Sensor-Integrated Injection Molding
Real-time monitoring of pressure, temperature, and flow.
Enables defect detection and quality assurance during production.
Reduces cycle times and material waste.
b. AI-Driven Process Control
Uses machine learning to optimize parameters dynamically.
Predicts potential failures or anomalies in the molding process.
Improves product consistency and reduces downtime.
c. Advanced Composite Molding
Incorporates materials like carbon fiber-reinforced polymers (CFRPs).
Enables lightweight, high-strength automotive parts.
Supports vehicle weight reduction for better fuel efficiency or EV range.
d. 3D Printing and Additive Molding Hybrids
Allows rapid prototyping of mold components.
Reduces tooling time and costs.
Facilitates customization in vehicle interiors and specialty parts.
e. Digital Twin Technology
Creates a virtual replica of the molding process.
Simulates different scenarios to optimize tool design and process parameters.
Enables predictive maintenance and performance tuning.
3. Benefits for the Automotive Sector
Weight reduction through optimized material usage.
Faster time-to-market with agile prototyping and smart production.
Enhanced quality control and fewer defects.
Lower environmental impact due to reduced waste and energy use.
Greater design flexibility enabling complex geometries and multifunctional parts.
4. Applications in Automotive Components
Smart molding is used in the manufacturing of:
Bumpers and body panels
Dashboard and interior trim
Headlight housings and lighting components
Structural components for EVs and hybrids
Battery casings and enclosures
5. Challenges and Future Trends
Challenges:
High initial investment in smart systems and training
Integration complexity with legacy systems
Data management and cybersecurity concerns
Future Trends:
Wider adoption of edge computing and AI at the machine level
More sustainable molding materials (recyclable and bio-based)
Integration with Industry 4.0 and automated supply chains
Cross-functional collaboration between OEMs and material scientists
Conclusion
Smart molding technologies are revolutionizing automotive manufacturing by enabling intelligent, flexible, and sustainable production systems. As the industry continues to shift toward electrification and digitalization, embracing these innovations will be key to maintaining competitiveness and meeting evolving consumer and regulatory demands.
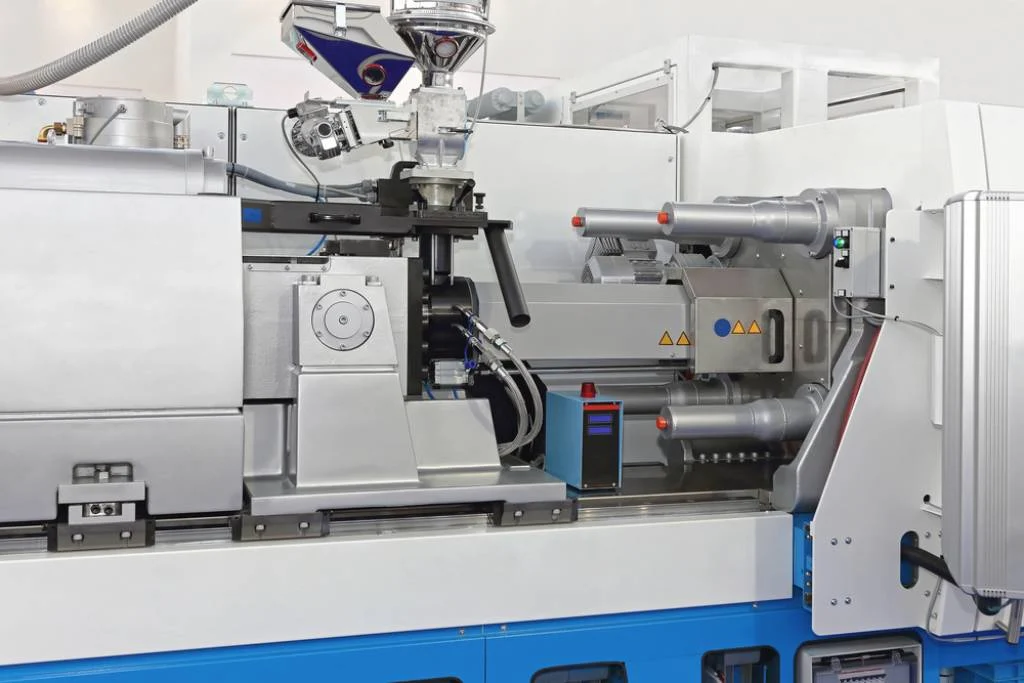