Polyvinyl Chloride (PVC) is one of the most widely used thermoplastics across industries due to its excellent chemical resistance, durability, and ease of fabrication. However, traditional PVC can degrade over time when exposed to ultraviolet (UV) radiation, leading to discoloration, brittleness, and loss of mechanical properties. To combat this, UV-resistant PVC formulations have been developed, making PVC suitable for outdoor molding applications such as trims, panels, enclosures, and exterior components.
Understanding UV Resistance in PVC
PVC is inherently susceptible to UV degradation, which occurs when UV radiation breaks down the polymer chains. This degradation typically manifests as:
Color fading or yellowing
Surface chalking
Loss of mechanical strength
Cracking or brittleness
To address these issues, UV-resistant PVC incorporates UV stabilizers and impact modifiers during the compounding process. Common additives include:
Titanium dioxide (TiO₂): A white pigment that reflects UV light and acts as a barrier.
Carbon black: Used in darker PVC formulations, provides strong UV shielding.
UV absorbers: Chemicals that absorb UV radiation and dissipate it as low-level heat.
Hindered amine light stabilizers (HALS): Help to neutralize free radicals formed during UV exposure.
Benefits of UV-Resistant PVC in Outdoor Applications
UV-resistant PVC provides a combination of advantages that make it suitable for various outdoor molded products:
Enhanced weatherability: Maintains appearance and structural integrity over prolonged sun exposure.
Color retention: Reduced fading and discoloration even in harsh climates.
Durability: Resists cracking, peeling, and brittleness due to UV exposure.
Low maintenance: Resistant to mold, mildew, and corrosion.
Cost-effective: More economical compared to materials like aluminum or UV-resistant wood composites.
Typical Outdoor Molding Applications
Exterior Trim and Fascia Boards
Outdoor Signage and Display Frames
Window and Door Moldings
Garden and Landscape Edging
Electrical Enclosures and Conduits
Architectural Moldings and Claddings
Design and Processing Considerations
When designing products using UV-resistant PVC for outdoor use, consider the following:
Wall thickness: Ensure structural strength under thermal cycling.
Color selection: Lighter colors typically reflect more UV and remain cooler.
Surface finish: Glossy finishes may reduce dirt accumulation and chalking.
Processing temperatures: Use recommended settings to avoid thermal degradation during molding or extrusion.
Conclusion
UV-resistant PVC is a highly effective solution for outdoor molding applications where long-term exposure to sunlight and weather is a concern. Through the use of advanced additives and proper formulation, PVC can achieve extended service life, maintain its aesthetic appeal, and provide excellent value for a wide range of outdoor products.
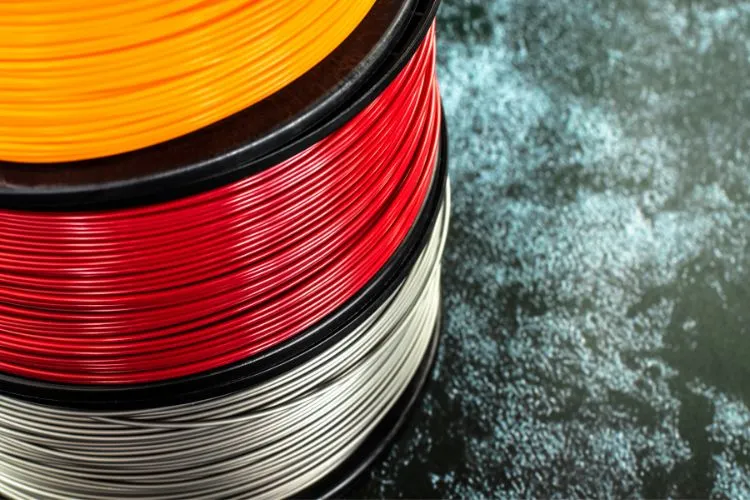