Hybrid molding techniques are advanced manufacturing methods that combine different molding processes or materials to produce automotive components with enhanced performance, reduced weight, and improved cost efficiency. These techniques are increasingly adopted by the automotive industry to meet stringent regulatory demands for fuel efficiency, emissions, and safety while maintaining high aesthetic and functional standards.
1. What is Hybrid Molding?
Hybrid molding refers to the integration of two or more molding processes or materials within a single production cycle. This often involves combining:
Injection molding with thermoforming, compression molding, or metal inserts
Thermoplastics with fiber-reinforced composites, metal, or elastomers
2. Common Hybrid Molding Techniques
a. Injection-Compression Molding
Combines injection molding with compression to form lightweight, dimensionally stable parts.
Applications: Structural parts like door modules and front-end carriers.
b. Overmolding
Involves molding a second material over a previously molded substrate (plastic over metal, rubber over plastic).
Applications: Soft-touch interior components, seals, and gaskets.
c. Insert Molding
Inserts (often metal) are placed into a mold and thermoplastic is injected around them.
Applications: Parts requiring reinforcement, such as brackets or fasteners.
d. Thermoplastic Composite Molding (TPC)
Pre-formed thermoplastic composites are heated and placed into a mold, then overmolded with plastic.
Applications: Structural components like seat backs and bumper beams.
e. In-Mold Decoration (IMD) + Molding
Decorative films are inserted into the mold, and plastic is molded behind them.
Applications: Instrument panels, console trims, and other aesthetic parts.
3. Advantages of Hybrid Molding
Weight reduction: Use of composites and integration of parts lowers overall vehicle mass.
Cost savings: Combines multiple processes into one, reducing assembly and labor costs.
Improved functionality: Enhances part strength, thermal resistance, and acoustic performance.
Design flexibility: Enables complex geometries and integration of aesthetic elements.
4. Materials Used
Thermoplastics: Polypropylene (PP), Polyamide (PA), ABS, PC/ABS
Composites: Glass-fiber or carbon-fiber reinforced polymers
Metals: Aluminum, steel (for inserts or overmolded parts)
Elastomers: TPE, TPU for soft-touch applications
5. Challenges and Considerations
Tooling complexity: Molds for hybrid processes are more complex and expensive.
Material compatibility: Different thermal and mechanical properties must be managed.
Process control: Requires precise temperature, pressure, and timing coordination.
Recycling: Multi-material parts may pose recycling challenges.
6. Applications in Automotive Industry
Exterior: Bumper systems, liftgates, roof modules
Interior: Door panels, dashboards, trim parts
Under-the-hood: Engine covers, structural supports
Electrical/Electronic: Housings, connectors, sensor mounts
7. Future Trends
Increased use of bio-based composites for sustainability
More automation and robotics for precise hybrid molding
Simulation software for predictive modeling and defect reduction
Focus on recyclable hybrid solutions aligned with circular economy goals
Conclusion
Hybrid molding techniques represent a critical advancement in automotive manufacturing, enabling the production of lightweight, high-performance, and aesthetically pleasing components. As the industry moves toward electric and sustainable vehicles, these technologies will play a vital role in redefining how car parts are designed and produced.
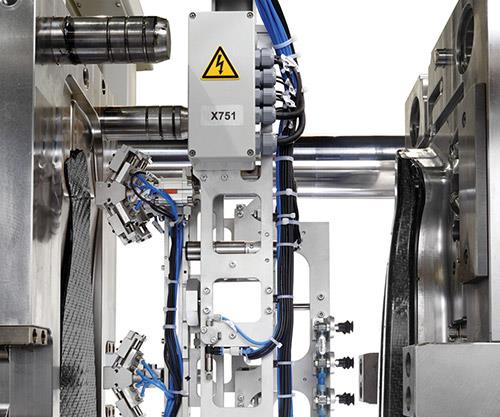