Injection molding is a widely used manufacturing process for producing plastic components in various industries such as automotive, medical, electronics, and consumer goods. However, the process can be energy-intensive and contribute significantly to greenhouse gas emissions. Reducing the carbon footprint of injection molding is critical for achieving sustainability goals and regulatory compliance.
1. Understanding Carbon Footprint in Injection Molding
The carbon footprint in injection molding primarily arises from:
Energy consumption during plastic melting and mold clamping
Raw material production (especially virgin plastic)
Machine operation and maintenance
Post-processing and logistics
2. Strategies to Reduce Carbon Footprint
a. Material Selection
Use of recycled plastics: Replacing virgin plastics with post-consumer or post-industrial recycled materials can drastically cut emissions.
Biodegradable and bio-based polymers: Options like PLA or PHA reduce dependence on fossil fuels.
Material optimization: Reducing part weight and using fillers (e.g., glass fiber) can decrease material consumption.
b. Energy Efficiency Improvements
All-electric injection molding machines: These machines consume up to 50-70% less energy than traditional hydraulic machines.
Servo-hydraulic systems: Offer better energy efficiency than conventional hydraulics by adjusting motor speed and pressure.
Smart sensors and controllers: Monitor and optimize energy use during the process.
c. Process Optimization
Cycle time reduction: Faster cycles mean less energy per part. This can be achieved through improved mold design and better thermal management.
Hot runner systems: Reduce waste by eliminating the need for sprues and runners.
Scientific molding: Data-driven molding techniques minimize defects, reducing scrap and rework.
d. Sustainable Mold Design
Lightweight molds: Use of lighter materials (like aluminum for prototyping) can reduce energy in mold handling.
Improved thermal conductivity: Better cooling designs reduce cycle times and energy consumption.
e. Renewable Energy Integration
Use of solar, wind, or other renewable sources to power the facility can significantly offset carbon emissions from grid electricity.
f. Waste Management and Recycling
Implement closed-loop recycling systems where scrap is reground and reused.
Lean manufacturing principles to minimize overproduction, waste, and excess inventory.
3. Digitalization and Smart Manufacturing
Industry 4.0 tools (IoT, AI, machine learning) can predict machine behavior, optimize energy use, and reduce downtime.
Carbon tracking software: Helps monitor and report real-time carbon emissions.
4. Life Cycle Assessment (LCA)
Performing an LCA helps identify hotspots in emissions across the product’s life—from raw material extraction to end-of-life disposal—and provides a roadmap for targeted improvements.
5. Case Studies and Real-World Examples
Companies like Arburg and ENGEL have introduced energy-efficient machines that reduce emissions.
Automotive and packaging industries have shown success with recycled and bio-based materials without compromising performance.
Conclusion
Reducing the carbon footprint in injection molding is a multi-faceted effort involving material innovation, energy efficiency, advanced technology, and sustainable practices. Adopting a comprehensive strategy not only helps manufacturers meet environmental targets but also offers long-term cost savings, regulatory compliance, and enhanced brand reputation.
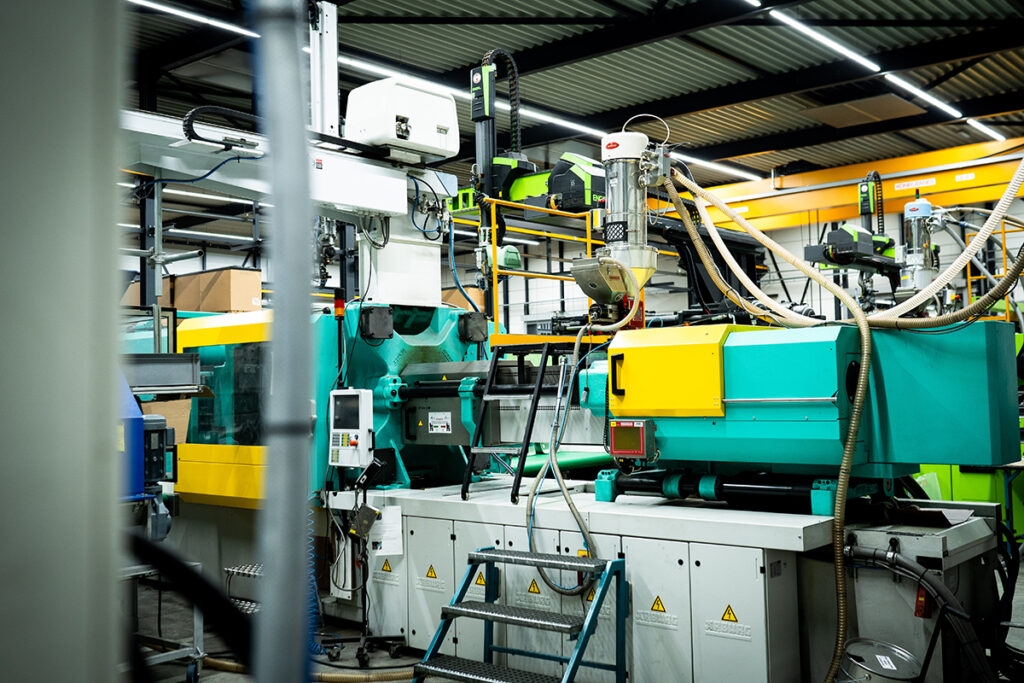