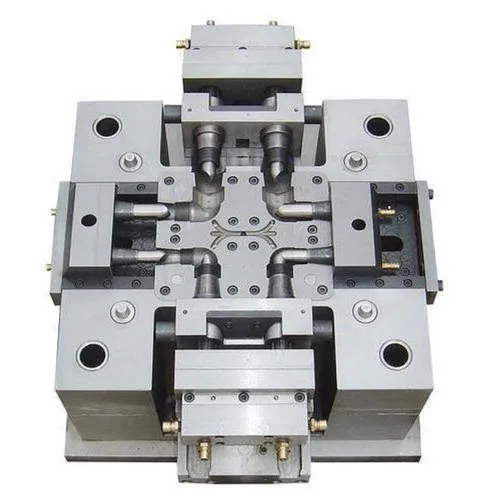
The design of PVC molds for plumbing applications focuses on achieving high dimensional accuracy, smooth surface finishes, and optimal flow of molten material. Mold cavities are carefully engineered to produce fittings such as elbows, tees, couplings, and valves with precise dimensions to ensure leak-free connections. Draft angles are incorporated into the design to facilitate easy ejection of parts without damage, while venting systems prevent air entrapment, which can lead to defects like voids or bubbles.
Wall thickness uniformity is another crucial factor in mold design, as inconsistent thickness can lead to warping or weak points in the final product. Additionally, the molds must accommodate features like threads, flanges, or grooves that are essential for functional plumbing components.
Material Selection and Mold Durability
The molds used for PVC plumbing components are typically made from high-strength tool steel or hardened aluminum to withstand repeated cycles of high-pressure injection molding. These materials ensure durability and resistance to wear, maintaining precision over extended production runs. Cooling channels are integrated into the mold design to regulate temperatures during the injection process, preventing material degradation and reducing cycle times.
Applications of PVC Molds in Plumbing
PVC molds are used to manufacture a wide range of plumbing products, including pipes, joints, and specialized fittings. These components are employed in residential, commercial, and industrial plumbing systems for water supply, drainage, and irrigation. Molded PVC components are lightweight, corrosion-resistant, and capable of handling high water pressures, making them a preferred choice in the industry.
Customization and Innovation
Advanced mold design techniques enable the creation of customized plumbing components tailored to specific projects or standards. Computer-Aided Design (CAD) software allows engineers to simulate mold performance and optimize designs for maximum efficiency and minimal material waste. Additionally, innovations like multi-cavity molds and automated systems enhance production speed and cost-effectiveness.