In the highly competitive automotive manufacturing sector, efficiency and sustainability are key drivers of innovation. One area garnering increasing attention is the mold cooling system used in automotive plastic and metal part production. Mold cooling significantly impacts the cycle time, energy consumption, and product quality in molding processes such as injection molding and die casting. Implementing energy-efficient mold cooling systems can lead to substantial cost savings, reduced environmental impact, and enhanced productivity.
Understanding Mold Cooling in Automotive Manufacturing
Mold cooling systems are critical in maintaining optimal temperatures during the molding process. These systems help solidify molten material (plastic or metal) within the mold, affecting cycle time and part quality. In automotive manufacturing, molds are used to produce various components, from dashboards and bumpers to intricate metal engine parts.
Traditional Mold Cooling Techniques
Use of constant flow water channels.
Basic temperature regulation without feedback control.
High energy consumption due to continuous pumping and inefficient heat exchange.
The Need for Energy Efficiency
Traditional mold cooling methods can be energy-intensive, often using more cooling capacity than needed. With increasing emphasis on green manufacturing, automotive companies are looking to:
Lower operating costs.
Reduce greenhouse gas emissions.
Comply with environmental regulations.
Achieve sustainability goals.
Energy-Efficient Mold Cooling Technologies
1. Conformal Cooling Channels
Description: 3D-printed channels that follow the contours of the mold.
Benefits: Improved thermal conductivity, faster and more uniform cooling, reduced cycle times, and lower energy use.
2. Advanced Thermal Control Systems
Features: Smart controllers that adjust coolant flow based on real-time temperature feedback.
Advantages: Avoids overcooling, minimizes energy waste, enhances process consistency.
3. Variable Speed Pumps
Function: Adjust flow rates to meet cooling demands dynamically.
Efficiency: Reduces electricity usage compared to constant-speed pumps.
4. Closed-Loop Cooling Systems
Design: Recycles cooling water through heat exchangers.
Sustainability: Minimizes water waste and heat discharge into the environment.
5. High-Efficiency Heat Exchangers
Innovation: Enhanced materials and designs for quicker heat transfer.
Impact: Reduces energy required for cooling and shortens production cycles.
Benefits of Energy-Efficient Mold Cooling
Benefit | Description |
---|---|
Reduced Energy Costs | Lower power consumption results in significant savings over time. |
Shorter Cycle Times | Improved cooling performance allows faster production cycles. |
Better Product Quality | Uniform cooling reduces warping, shrinkage, and defects. |
Environmental Compliance | Aligns with global emissions and water conservation standards. |
Extended Equipment Lifespan | Lower thermal stress prolongs mold and machine life. |
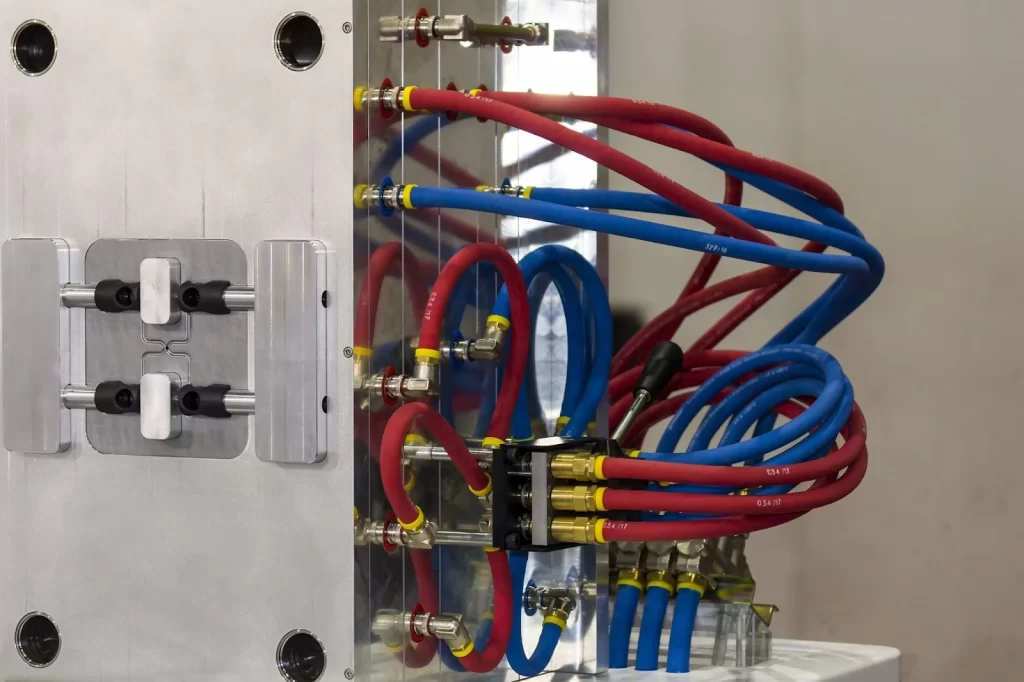