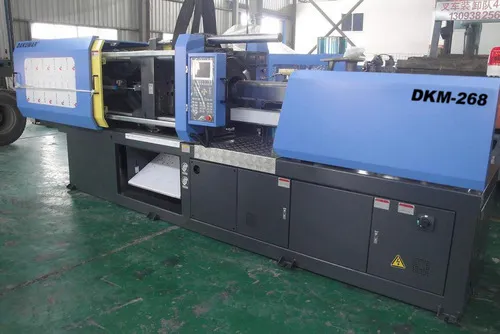
Automation is reshaping the landscape of PVC molding, making the process faster, more precise, and cost-effective while addressing the challenges associated with molding polyvinyl chloride (PVC). This transformation is driven by the integration of robotics, advanced machinery, and smart technologies, which together enhance production capabilities and product quality.
Streamlining Production Processes
Automation reduces cycle times and enhances throughput in PVC molding by optimizing every stage of the process. Robots and automated systems manage material loading, injection, cooling, and part removal, ensuring consistent performance. This streamlined approach minimizes human intervention, reducing delays and boosting overall efficiency.
Enhancing Precision and Quality Control
PVC molding requires precise temperature and pressure control to produce high-quality parts. Automated systems ensure that these parameters are consistently maintained, reducing the likelihood of defects such as warping or bubbles. Advanced sensors and monitoring systems provide real-time feedback, enabling manufacturers to detect and address inconsistencies immediately.
Reducing Material Waste and Cost
Automation significantly reduces material waste by precisely controlling the injection process. This is particularly important for PVC, where excess material can lead to financial and environmental costs. Automated machines optimize material usage, ensuring that only the required amount of PVC is used, which translates into cost savings and improved sustainability.
Addressing Health and Safety Concerns
The handling of PVC involves potential exposure to harmful chemicals and fumes, which pose risks to workers. Automation minimizes direct human contact with PVC during processing, enhancing workplace safety. Additionally, automated systems can be integrated with advanced ventilation and filtration technologies to ensure compliance with health and safety regulations.
Improving Flexibility and Customization
Automated PVC molding systems offer enhanced flexibility to meet diverse manufacturing needs. With programmable settings, these systems can quickly switch between different molds and designs, enabling manufacturers to produce customized products efficiently. This adaptability is essential in industries such as construction, healthcare, and consumer goods, where varying product specifications are common.