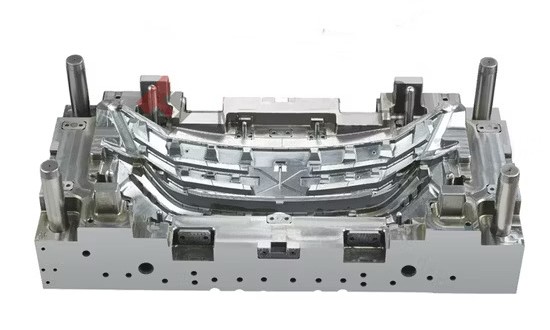
Injection molding plays a critical role in manufacturing under-the-hood components for the automotive industry. These parts, which must endure harsh conditions such as high temperatures, chemical exposure, and mechanical stress, require robust materials and precise engineering. Injection molding provides the necessary precision, material versatility, and cost-efficiency to meet these stringent requirements.
Under-the-hood components often include engine covers, air intake manifolds, coolant reservoirs, gaskets, and sensor housings. These parts are typically designed to withstand high thermal and chemical loads, making material selection crucial. Thermoplastics such as polyamide (PA), polybutylene terephthalate (PBT), and high-performance polymers like polyphenylene sulfide (PPS) are commonly used. These materials offer excellent heat resistance, dimensional stability, and chemical durability, ensuring reliability in demanding environments.
One of the key advantages of injection molding for under-the-hood applications is the ability to produce parts with complex geometries and integrated features. This reduces the need for assembly and enhances the performance of the component. For example, multi-functional parts with built-in reinforcements or channels for fluid and air flow can be molded in a single process. Insert molding and overmolding techniques are also used to combine multiple materials or integrate metal inserts, enhancing functionality and strength.
Cost-efficiency is another significant benefit of injection molding in automotive applications. The high production speed, coupled with the scalability of the process, allows manufacturers to produce large volumes of components consistently. Innovations like gas-assisted molding and hot-runner systems further optimize production by reducing material usage and cycle times.