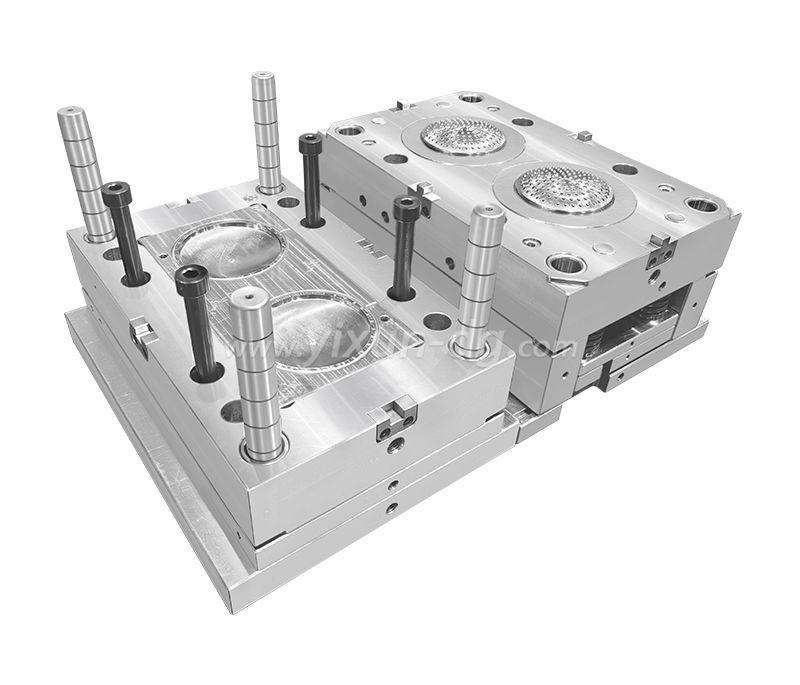
Injection molding tooling, often referred to simply as “the mold,” is an essential component in the injection molding process. It serves as the medium to shape molten plastic into precise and repeatable parts. The tooling design and construction significantly impact production efficiency, part quality, and cost-effectiveness. Below are detailed aspects of injection molding tooling:
The mold comprises various interconnected parts, each serving a specific purpose. The primary components include:
- Mold Base: The structural framework that holds the core and cavity inserts securely within the molding machine.
- Core and Cavity Inserts: These are the most critical sections, forming the internal and external features of the part. Their precision determines the final product’s quality.
The choice of material for tooling impacts its durability, thermal performance, and cost.
- Hardened Steel: Offers high durability and precision, ideal for long production runs.
- Pre-Hardened Steel: Cost-effective for medium-volume production, with moderate wear resistance.
Different types of molds cater to diverse production requirements:
- Prototype Tooling: Temporary molds designed for testing and refining part designs before committing to production tooling.
- Production Tooling: Durable molds built for large-scale production with high precision.
Effective tooling design is crucial for efficient manufacturing and high-quality parts.
- Draft Angles: Essential to ensure easy ejection of parts, preventing damage to the mold or product.
- Venting: Proper placement of vents allows trapped air to escape, avoiding defects like voids or burn marks.
Regular maintenance is vital to keep molds operational and extend their lifespan. Cleaning after each production run prevents material buildup, while periodic inspections help identify wear or damage early. Timely repairs and adjustments ensure consistent production quality and reduce downtime.