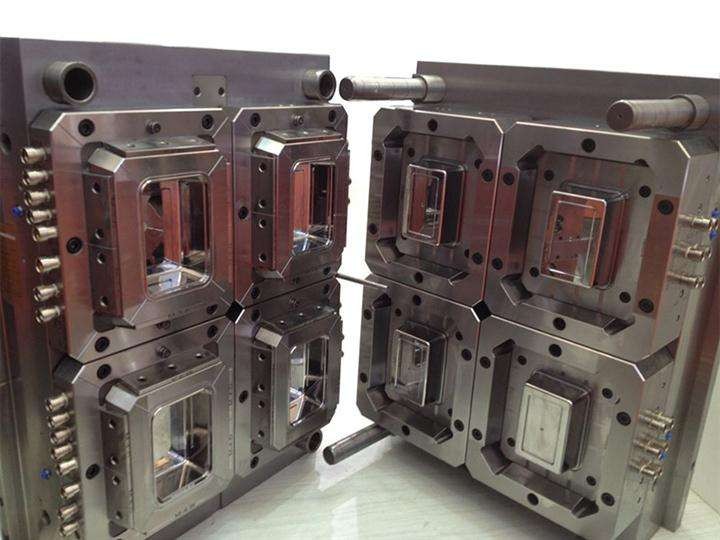
Thin-wall injection molding is a specialized manufacturing process used to produce lightweight, high-strength plastic components with extremely thin walls. This technique is widely applied in industries such as electronics, automotive, and packaging, where reducing material usage and achieving precision are critical. Mastering thin-wall injection molding requires advanced techniques, specialized equipment, and a deep understanding of material behavior under high pressure and speed.
Material Selection
Choosing the right material is a fundamental aspect of thin-wall injection molding. The selected resin must exhibit high flowability to fill the thin cavities quickly and evenly. Common materials include polycarbonate (PC), polypropylene (PP), polyethylene (PE), and acrylonitrile butadiene styrene (ABS). High-performance engineering plastics, such as liquid crystal polymers (LCP) or polyether ether ketone (PEEK), are often used for applications requiring exceptional strength and heat resistance. Additives like glass fibers or impact modifiers may be incorporated to enhance material properties without compromising flow characteristics.
Optimized Mold Design
The design of the mould is critical for thin-wall injection molding. Features such as narrow gates, balanced runners, and uniform cavity thickness ensure smooth and consistent flow. Cooling channels are strategically placed to achieve rapid and uniform cooling, preventing warping or shrinkage. Mold materials must be highly durable to withstand the high injection pressures and temperatures associated with thin-wall processes. Advanced simulation tools are often used to optimize mould design and predict material behavior during injection.
High-Speed Injection
Thin-wall parts require extremely high injection speeds to ensure the molten plastic fills the cavity before it cools and solidifies. Specialized high-speed injection molding machines with advanced servo-driven systems are commonly used. These machines deliver precise control over injection speed, pressure, and temperature, ensuring uniform material distribution even in ultra-thin sections.
Process Control and Monitoring
Achieving consistent quality in thin-wall injection molding demands tight process control. Real-time monitoring of parameters such as injection pressure, temperature, and cycle time is essential. Advanced systems using sensors and feedback loops help detect and correct deviations, ensuring high repeatability and minimal scrap rates. Controlled cooling and ejection processes also help maintain the structural integrity of thin-walled parts.
Gas-Assisted Injection Molding
In some cases, gas-assisted injection molding techniques are employed to reduce material usage and enhance part strength. This process involves injecting a controlled amount of inert gas into the molten material to create hollow sections. This reduces stress on the part, improves rigidity, and minimizes warping.