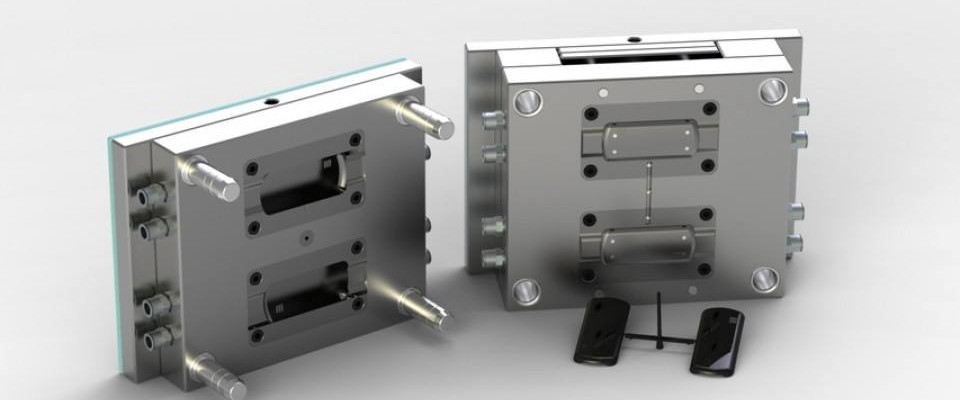
Injection molding is a versatile and efficient manufacturing process widely utilized for rapid production of high-quality parts. This method is especially advantageous for industries requiring large volumes of components with consistent quality, including automotive, medical, consumer goods, and electronics. With advancements in tooling, materials, and process optimization, injection molding has become a cornerstone of rapid manufacturing, enabling businesses to meet tight deadlines without compromising precision or durability.
Key Features of Injection Molding for Rapid Manufacturing
High-Speed Production
Injection molding is designed for quick cycle times, typically ranging from a few seconds to a couple of minutes, depending on the complexity of the part and material used. This speed makes it ideal for producing large quantities in a short timeframe.Repeatability and Consistency
The process ensures identical parts with tight tolerances in every production cycle, which is crucial for industries requiring standardized components.Material Versatility
A wide range of materials, including thermoplastics, thermosets, elastomers, and composites, can be used in injection molding. This allows manufacturers to select materials based on specific performance requirements like strength, flexibility, or chemical resistance.Design Flexibility
Complex geometries, intricate details, and customized textures can be achieved with precision molds, enabling the production of parts tailored to specific applications.
Applications of Injection Molding in Rapid Manufacturing
Prototyping
Injection molding is often used to produce prototypes that mimic the final product, allowing for functional testing, design validation, and market feedback.Bridge Manufacturing
For businesses transitioning from prototyping to mass production, injection molding serves as an intermediary step, producing low-to-medium volumes quickly while finalizing production tooling.Customization
Short production runs of customized or personalized parts, such as medical devices or branded consumer products, can be efficiently handled with injection molding.Mass Production
Rapid manufacturing through injection molding is essential for producing millions of parts in industries like automotive and consumer electronics.
Technological Advancements Enhancing Rapid Manufacturing
Rapid Tooling
- Soft Tooling: Tools made from aluminum or hybrid materials are faster and more affordable to produce compared to traditional steel molds.
- 3D-Printed Molds: Additive manufacturing enables the creation of molds in days rather than weeks, significantly reducing lead times.
Process Automation
Automated injection molding systems reduce human intervention, improving speed, accuracy, and overall productivity.Advanced Simulation Tools
Software like mold flow analysis predicts and resolves potential manufacturing issues, optimizing mold design and process parameters for faster production.Innovative Materials
New polymer blends and composites reduce cycle times and enhance material performance, meeting the demands of rapid manufacturing without sacrificing quality.
Advantages of Injection Molding for Rapid Manufacturing
Cost-Efficiency
Once the mold is created, the per-unit cost of parts decreases significantly, making it an economical choice for high-volume production.Scalability
Injection molding supports both low-volume and mass production, allowing manufacturers to scale up operations as needed.Quality Assurance
The process consistently delivers parts with superior strength, surface finish, and dimensional accuracy.Time Savings
Reduced cycle times and innovations like rapid tooling minimize production lead times, enabling faster delivery to market.
Challenges and Solutions
High Initial Tooling Costs
While tooling can be expensive, techniques like soft tooling and modular molds help reduce upfront investment for rapid manufacturing.Material Waste
Excess material from sprues and runners can be a concern, but it is often recycled or minimized through hot runner systems.Complex Part Designs
Highly intricate designs may require multi-cavity or hybrid molds, which can increase complexity. Advanced CAD/CAM systems mitigate this by optimizing mold design.