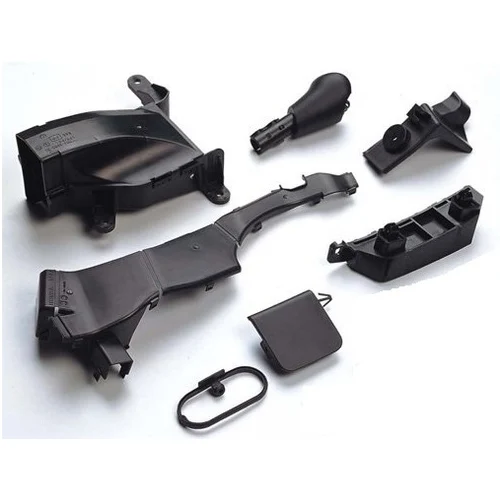
Injection molding is a critical manufacturing process in the production of automotive safety parts. Its ability to create highly precise, durable, and complex components makes it indispensable in the automotive industry, where safety is paramount. From airbags and seatbelt mechanisms to impact-absorbing structures, injection molding plays a significant role in ensuring that safety parts meet stringent regulatory standards and performance requirements.
Importance of Injection Molding for Safety Parts
High Precision
Injection molding ensures that safety-critical components are manufactured with tight tolerances, ensuring proper fit and functionality. For example, the precise alignment of airbag housings is essential for deployment accuracy.Material Selection
High-performance thermoplastics, such as polycarbonate (PC), polybutylene terephthalate (PBT), and glass-reinforced nylon, are often used for their strength, impact resistance, and durability.Repeatability
The process allows for the mass production of identical parts, ensuring consistency across all components, a vital factor for safety compliance.Design Flexibility
Complex geometries, overmolding, and integration of multiple features into a single part are possible, reducing assembly time and enhancing overall performance.
Applications of Injection Molding in Automotive Safety
Airbag Components
- Housings and Covers: Durable thermoplastic housings protect the airbag module and ensure proper deployment.
- Gas Diffusers: Injection molding is used to create the precise structures that channel inflation gases effectively.
Seatbelt Mechanisms
- Retractors and Buckles: Injection-molded parts provide the strength and reliability needed for retractors and buckle housings to perform under stress.
- Guides and Clips: Lightweight yet robust components ensure seatbelt alignment and ease of use.
Impact Absorption Systems
- Energy Absorbers: Molded components in bumpers, dashboards, and interior trims absorb and dissipate energy during collisions.
- Crumple Zones: Molded plastic reinforcements in vehicle frames enhance crashworthiness while reducing weight.
Child Safety Systems
- Car Seats: Injection-molded structures provide a lightweight yet robust framework for child car seats, meeting rigorous safety standards.
Interior Safety Features
- Steering Wheel Housings: Molded parts integrate with airbag systems and ensure structural integrity during impact.
- Headrest Supports: Provide comfort and whiplash protection, with molded structures offering durability and flexibility.
Materials Used in Safety Parts
Polycarbonate (PC)
- High impact resistance and optical clarity make it suitable for safety-critical parts such as transparent airbag covers.
Nylon (PA)
- Often glass-reinforced for additional strength, nylon is used in seatbelt mechanisms and airbag housings.
Polypropylene (PP)
- Lightweight and energy-absorbing, ideal for bumper cores and interior trim components.
PBT and PC/ABS Blends
- These blends offer a balance of toughness and thermal stability, often used in sensor housings and brackets.
Key Advantages of Injection Molding for Safety Parts
Cost Efficiency
High-volume production reduces per-unit costs while maintaining superior quality.Design Integration
Multiple functionalities can be integrated into a single molded part, such as clips, brackets, or channels, reducing assembly complexity.Lightweight Solutions
Plastic components reduce vehicle weight, contributing to fuel efficiency and reducing the overall environmental footprint.Durability and Longevity
Molded parts are resistant to wear, impact, and environmental factors, ensuring long-term performance.
Quality and Safety Standards
Regulatory Compliance
Injection-molded safety parts must meet stringent automotive standards, including ISO 26262 for functional safety and FMVSS (Federal Motor Vehicle Safety Standards).Testing and Validation
- Components undergo rigorous testing for impact resistance, heat resistance, and fatigue to ensure they meet performance requirements.
- Mold flow analysis and simulations are used during design to predict and mitigate potential defects.
Traceability
Advanced manufacturing systems allow for part traceability, ensuring that quality issues can be quickly identified and addressed.
Challenges in Injection Molding for Safety Parts
Defect Prevention
- Defects such as sink marks, voids, or warping can compromise safety.
- Solution: Optimized mold design, material selection, and precise process control minimize defects.
Material Performance
- Ensuring materials maintain performance under extreme conditions such as high temperatures or impacts.
- Solution: Use of advanced engineering-grade thermoplastics and rigorous testing.
Complex Part Requirements
- Some parts require intricate designs with overmolding or multi-material construction.
- Solution: Advanced mold-making technologies, including multi-cavity and multi-shot molding.
Future Trends in Injection Molding for Safety Parts
Lightweight Materials
- Continued development of high-strength, lightweight materials to enhance safety and fuel efficiency.
Advanced Molding Techniques
- Use of 3D printing for rapid prototyping and conformal cooling channels for enhanced part precision and faster cycle times.
Smart Safety Systems
- Integration of sensors and electronic components into molded parts to support advanced driver-assistance systems (ADAS) and autonomous vehicle safety features.
Sustainability
- Increased use of recyclable and bio-based materials for safety parts to reduce environmental impact.