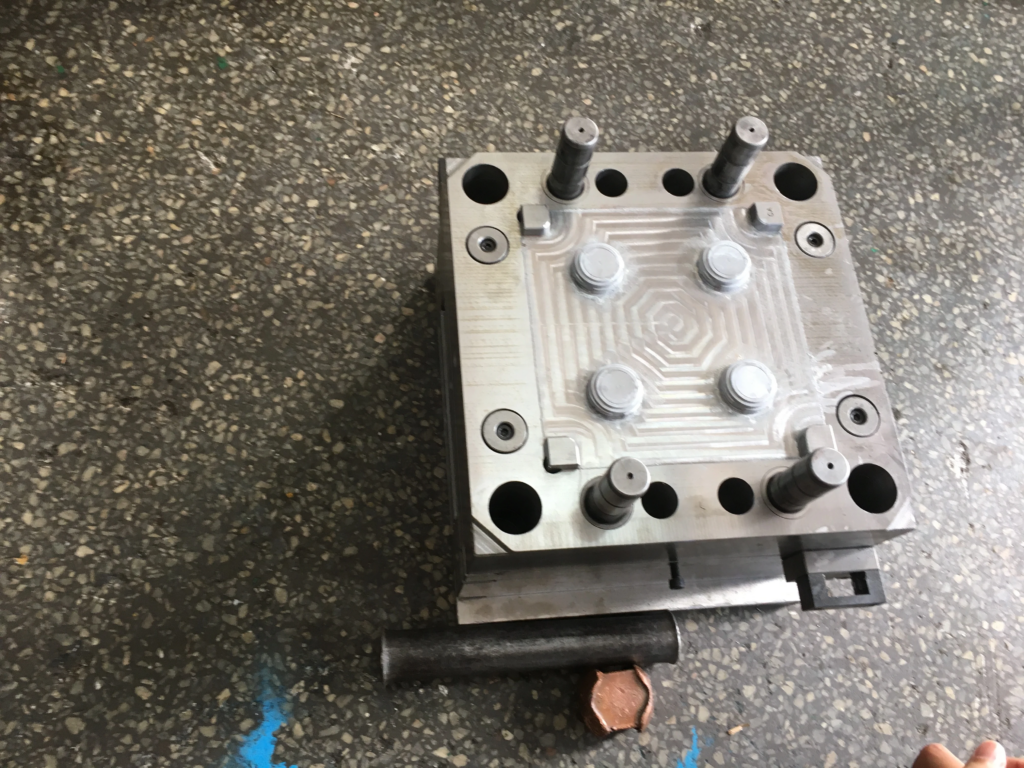
Plastic injection molding has witnessed significant innovations in recent years, revolutionizing the manufacturing industry with enhanced efficiency, precision, and sustainability. These advancements have allowed manufacturers to produce complex and high-performance plastic components with greater accuracy while reducing material waste and production costs. The introduction of cutting-edge technologies such as automation, advanced materials, and smart manufacturing has further elevated the capabilities of plastic injection molding across various industries, including automotive, medical, aerospace, and consumer goods.
One of the most notable innovations in plastic injection molding is multi-material and multi-shot molding, which enables the production of components using multiple materials in a single molding cycle. This technology allows manufacturers to combine different types of plastics or even integrate soft and hard materials within a single part. It enhances product functionality, eliminates the need for post-assembly processes, and improves durability. Overmolding, a related technique, is widely used to create ergonomic grips, sealing components, and aesthetically appealing designs.
Another major breakthrough is the integration of Industry 4.0 and smart manufacturing technologies into plastic injection molding. Real-time data monitoring, machine learning, and artificial intelligence (AI)-driven systems have optimized process control, minimizing defects and improving efficiency. Sensors and IoT-enabled machines track variables such as temperature, pressure, and injection speed, ensuring consistent quality and reducing downtime. These digital innovations help manufacturers achieve predictive maintenance, enhance productivity, and optimize material usage.
Sustainability has also been a driving force behind new developments in injection molding. Bio-based and recycled plastics are gaining popularity as manufacturers seek eco-friendly alternatives to traditional petroleum-based resins. Innovations in biodegradable polymers, such as polylactic acid (PLA) and polyhydroxyalkanoates (PHA), have enabled the production of sustainable plastic products without compromising performance. Additionally, advancements in closed-loop recycling systems allow manufacturers to reprocess and reuse plastic waste, significantly reducing environmental impact.
High-speed and micro-injection molding are also transforming the industry. Micro-injection molding enables the production of extremely small, high-precision components used in medical devices, electronics, and aerospace applications. With advancements in mold design, high-performance resins, and precision control, manufacturers can create intricate plastic parts with tight tolerances that were previously unattainable. High-speed injection molding, on the other hand, reduces cycle times and increases production efficiency, allowing for faster turnaround times in mass manufacturing.
As plastic injection molding continues to evolve, innovations in 3D-printed molds and rapid tooling are further enhancing flexibility and reducing lead times. 3D printing allows manufacturers to create prototypes and custom molds quickly, facilitating faster product development and design validation. This technology is particularly beneficial for low-volume production runs and custom parts, reducing costs associated with traditional mold fabrication.
With these ongoing advancements, plastic injection molding remains a cornerstone of modern manufacturing, enabling industries to produce high-quality, cost-effective, and sustainable plastic components. As technology progresses, the industry is poised to see even more innovations that enhance efficiency, precision, and environmental responsibility.