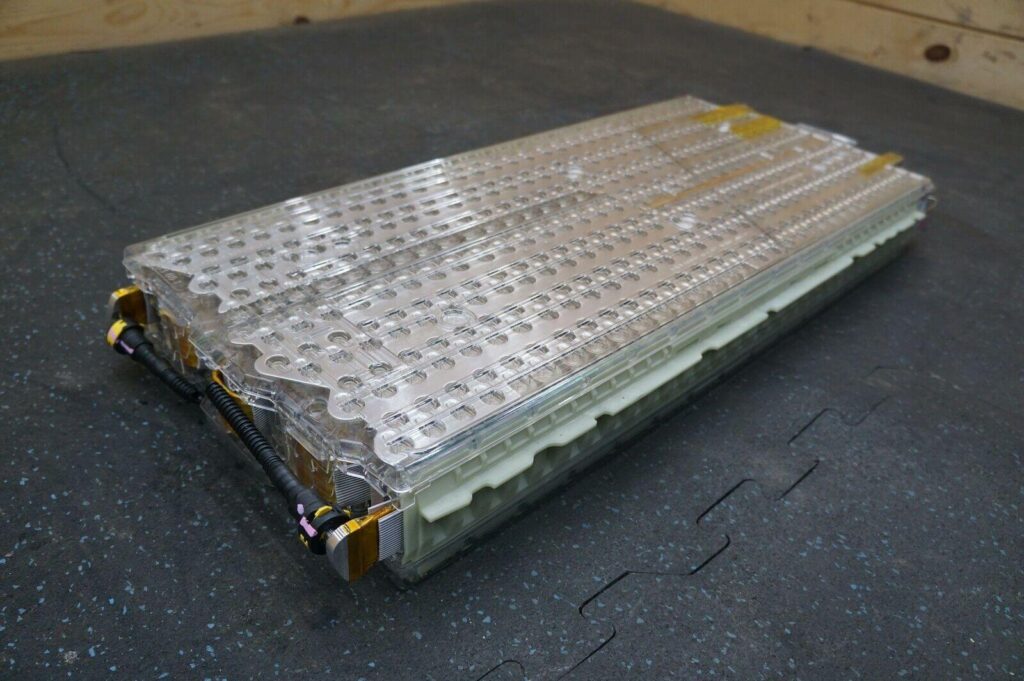
The rise of electric vehicles (EVs) has driven the demand for advanced battery technologies, requiring innovative manufacturing processes to enhance efficiency, safety, and cost-effectiveness. One such breakthrough is the use of 3D-printed molds for producing EV battery casings, offering manufacturers greater flexibility, faster prototyping, and improved design optimization. This technology is revolutionizing traditional molding processes by enabling rapid iteration, lightweight designs, and enhanced thermal management solutions for battery enclosures.
Advantages of 3D-Printed Molds in EV Battery Production
Faster Prototyping and Customization
Traditional mold fabrication for battery casings involves expensive tooling and long lead times. 3D printing allows manufacturers to create customized and complex mold designs in a fraction of the time, accelerating product development cycles. Engineers can rapidly iterate on casing designs to accommodate evolving battery technologies, improving energy efficiency and safety.Cost-Effective Production
Conventional metal molds are costly to produce and modify. With additive manufacturing, companies can reduce material waste and production expenses by using lightweight, high-performance polymers or metal-based composites. This is particularly beneficial for low-to-medium volume production runs, making 3D-printed molds a viable option for emerging EV manufacturers and startups.Design Complexity and Lightweight Structures
3D printing enables intricate geometric designs that are difficult to achieve with traditional machining. Battery casings require optimized airflow channels, cooling systems, and reinforced structures for impact resistance. With 3D-printed molds, manufacturers can integrate lightweight honeycomb or lattice structures that enhance mechanical strength while reducing overall weight, improving EV range and efficiency.Enhanced Thermal and Safety Performance
Battery casings must effectively manage heat to prevent overheating and ensure long-term reliability. 3D-printed molds allow the incorporation of integrated cooling channels and heat dissipation features directly into the mold design. By using high-performance heat-resistant materials, manufacturers can create battery enclosures with superior thermal properties, ensuring compliance with stringent safety regulations.Sustainability and Material Efficiency
The shift toward sustainable manufacturing is crucial in the EV industry. 3D printing reduces material waste compared to traditional subtractive manufacturing processes. Additionally, recyclable and bio-based polymers can be used to create molds, aligning with the industry’s focus on environmentally friendly production methods.Integration with Smart Manufacturing
The combination of 3D printing, AI-driven design optimization, and automated manufacturing enhances precision and repeatability in battery casing production. Manufacturers can leverage digital twin technology to simulate mold performance before production, reducing errors and optimizing material selection.
Future Prospects of 3D-Printed Molds in EV Manufacturing
As EV battery technology continues to advance, 3D-printed molds will play a pivotal role in enabling next-generation battery casings with improved safety, energy density, and performance. With the increasing adoption of solid-state batteries and modular designs, additive manufacturing will provide greater adaptability, allowing for on-demand production and localized manufacturing.
The integration of hybrid additive-subtractive manufacturing methods will further enhance the durability of 3D-printed molds, combining the best of both worlds—rapid prototyping with traditional machining precision. Additionally, advancements in high-temperature and conductive materials will enable the creation of battery casings with embedded sensors for real-time monitoring of thermal and electrical performance.
By leveraging 3D-printed molds, the EV industry can accelerate innovation, reduce costs, and enhance the sustainability of battery production. As technology progresses, this approach will continue to reshape the way manufacturers design and produce high-performance battery enclosures for the next generation of electric vehicles.