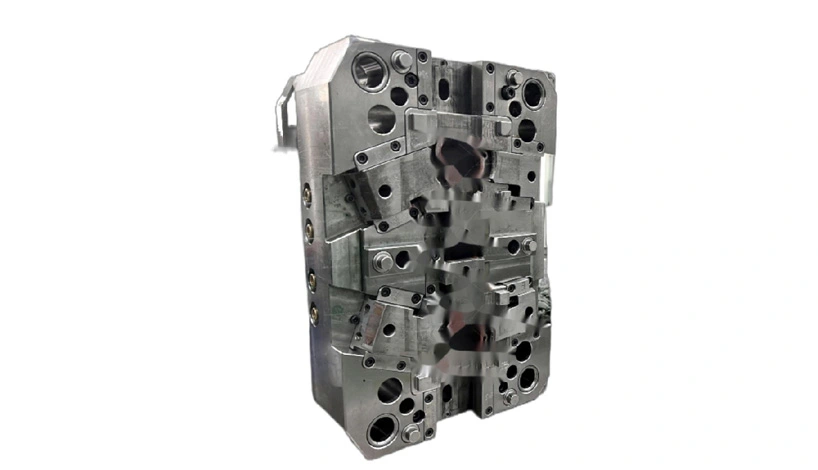
Injection molding plays a critical role in the manufacturing of smart wearable devices. As these devices become more advanced and feature-rich, the need for precise, reliable, and high-quality components has grown. Injection molding is widely used for producing the plastic parts of these devices, such as casings, buttons, and connectors, due to its ability to meet high-volume, complex design, and durability requirements.
Key Applications of Injection Molding for Smart Wearable Devices:
1. Precision Components
- Enclosures and Casings: The outer casings of smart wearables like smartwatches, fitness trackers, and AR glasses often need to be produced using injection molding. These casings require high precision to house sensitive electronics and sensors, while also maintaining a sleek and ergonomic design.
- Buttons and Dials: Smart wearables typically have physical buttons or rotating dials for user interaction. Injection molding allows for intricate designs and precise manufacturing of these small, often complex components.
- Charging Ports and Connectors: Small, durable connectors and charging ports are essential for wearables. Injection molding provides the necessary strength and precision for these parts, ensuring a reliable connection while maintaining a compact form factor.
2. Material Selection
- Lightweight and Durable Materials: Smart wearables need to be lightweight yet strong enough to withstand daily wear and tear. Materials like ABS (Acrylonitrile Butadiene Styrene), PC (Polycarbonate), and PPS (Polyphenylene Sulfide) are commonly used in injection molding for wearables. These materials offer a good balance between strength, durability, and light weight.
- Soft-touch and Medical-Grade Plastics: For comfort, wearables often require soft-touch finishes on surfaces that come into contact with the skin. Injection molding can accommodate materials with soft-touch coatings or medical-grade plastics for skin safety.
3. Customization and Complex Designs
- Multi-material Molding: Wearables may require multiple materials in a single component, like a soft rubber exterior combined with a hard plastic interior. Overmolding and two-shot molding techniques in injection molding allow for the creation of parts with different material properties in a single molding cycle, ensuring that different materials are combined for optimal functionality.
- Complex Geometries: Wearables often have intricate, compact, and ergonomic designs, and injection molding allows for the production of these complex geometries with tight tolerances, essential for both aesthetics and functionality.
4. Rapid Prototyping and Short Runs
- Prototyping: Injection molding is also used for producing prototypes and small batches of wearable components. Using rapid tooling and small batch runs, manufacturers can quickly iterate on new designs and test their prototypes before committing to large-scale production.
- Low-volume Production: Many wearable tech companies use injection molding for small-scale production runs when launching new products or for limited-edition designs.
5. Incorporating Electronics and Sensors
- Embedding Electronics: Some smart wearables require the integration of sensors, LEDs, or other electronics directly into the molded part. With insert molding or two-shot molding, manufacturers can embed electronic components (e.g., sensors, RFID chips, antennas) into the part during the molding process, saving assembly time and improving part integrity.
- Waterproofing and Sealing: Wearables, especially fitness trackers and smartwatches, often require waterproofing. Injection molding allows for the incorporation of seals and gaskets, helping to create waterproof or water-resistant designs that protect the internal electronics.
6. Smart Surface Features
- Touchscreen Frames and Bezels: Smart wearables often feature touchscreens, which require precise molding of bezel frames and surrounding elements. Injection molding can produce the fine details necessary to hold touch-sensitive screens securely while maintaining a clean and aesthetic design.
- Textured Surfaces and Patterns: Wearables, particularly fitness-oriented ones, may require textured surfaces for grip or visual appeal. Injection molding can create these textures on the surface of the components, such as raised patterns on the wristbands or backplates, for both functional and cosmetic reasons.
7. Scalability and Cost Efficiency
- High-Volume Production: Injection molding allows for the mass production of wearable device components at a relatively low cost per unit once the molds are developed. This makes it ideal for the growing demand for smart wearables, which often require millions of units to be produced at affordable prices.
- Automated Manufacturing: Injection molding is highly automated, which makes it efficient and cost-effective for the high-volume production needed for wearable devices.
8. Environmental Considerations
- Sustainability: As environmental concerns grow, manufacturers are increasingly focusing on sustainable materials for injection molding. Biodegradable plastics, recycled plastics, and energy-efficient manufacturing techniques are gaining traction in the production of smart wearable devices.
- Reduced Material Waste: Injection molding is a highly efficient process with minimal material waste compared to other manufacturing methods, which makes it an environmentally friendly option for high-volume production.