The automotive industry is undergoing a transformative shift towards electric vehicles (EVs) as the demand for sustainable and eco-friendly transportation grows. One of the key factors in the manufacturing process of EVs is the use of specialized molds that are designed to produce the intricate and high-performance components required for these advanced vehicles. Automobile molds for electric vehicle (EV) components are crucial in shaping and creating parts such as battery enclosures, electric motor housings, body panels, and other essential elements of the vehicle.
Key Aspects of Automobile Molds for EV Components
Material Selection and Durability
The molds used for EV components must be highly durable and resistant to wear. Since many EV parts, especially battery enclosures and motor casings, require materials with specific thermal and mechanical properties, molds must be designed to handle these demands. Common materials include high-strength steel, aluminum, and specialized alloys, chosen based on the specific needs of each component.
For example, the battery enclosures often need to withstand high temperatures, and materials like aluminum are chosen for their lightweight nature and thermal conductivity.
Complexity and Precision
EV components are often more complex than their internal combustion engine (ICE) counterparts due to the technological advancements in electric propulsion systems, battery technology, and integrated electronics. This increased complexity requires highly precise molds, designed with advanced 3D modeling and simulation technologies.
Precision in molding ensures that each part fits perfectly, reducing the risk of malfunctioning parts or issues with assembly. Mold makers must work closely with automotive engineers to meet tight tolerances for each component.
Types of Molds Used in EV Manufacturing
Injection Molds: Used to create plastic and composite parts that make up various components such as dashboard panels, interior parts, and battery holders. Injection molds are designed to work with high-performance thermoplastics and composite materials.
Compression Molds: These molds are used for molding composite materials like carbon fiber or fiberglass, which are commonly used in lightweight structural components of EVs. Compression molding is ideal for creating parts that require both strength and lightness.
Die Casting Molds: Die casting is used to manufacture aluminum or magnesium parts for various structural and underbody components of EVs. These molds are typically used for components like motor housings, drive train parts, and battery frames.
Blow Molds: Blow molding is used for hollow components in EVs, such as fluid reservoirs, which are crucial in the overall functioning of electric vehicles.
Customization and Versatility
One of the challenges in designing molds for EV components is the need for customization. With the increasing variety of electric vehicle designs, molds must be adaptable to different shapes, sizes, and functional requirements. This is particularly true for parts like battery packs, which may vary in terms of size and configuration depending on the manufacturer and the vehicle type.
For instance, some EV manufacturers may require specialized battery enclosures for their long-range models, while others may focus on compact designs for urban EVs. Molds must be adaptable to meet the demands of these diverse designs.
Sustainability Considerations
As the automotive industry moves towards greater sustainability, there is a growing emphasis on using molds to create parts that minimize environmental impact. This includes the use of recyclable materials, reducing waste during the molding process, and creating lightweight components that enhance the energy efficiency of electric vehicles.
Additionally, manufacturers are focusing on energy-efficient molding techniques to reduce the carbon footprint associated with production.
Advanced Technologies in Mold Design
With the rise of Industry 4.0, the use of digital tools and automation is playing an increasingly important role in mold design and manufacturing for EV components. Computer-aided design (CAD), computer-aided manufacturing (CAM), and 3D printing are some of the key technologies that help mold manufacturers produce highly accurate and efficient molds.
Additive Manufacturing (3D Printing): 3D printing technology is used to create prototype molds or even functional parts for EVs. This technology allows for rapid prototyping and customization of designs, enabling manufacturers to test and modify parts before committing to large-scale production.
Importance of Mold Maintenance and Optimization
Continuous optimization of molds is essential to ensure the production of high-quality EV components. Mold maintenance involves regular cleaning, reconditioning, and adjustments to ensure that the mold continues to perform at its peak.
The use of wear-resistant coatings and advanced mold materials helps in prolonging the lifespan of the molds, ensuring cost-effectiveness over time. Periodic checks and updates can prevent costly production errors and delays.
Examples of EV Components That Require Specialized Molds
Battery Enclosures: These large, robust parts house the battery pack and need to be able to handle high energy density and manage thermal distribution efficiently. Molds used for these enclosures must be extremely precise and strong, given the safety concerns associated with battery performance.
Electric Motor Housings: EVs use specialized electric motors that need lightweight but durable housings to protect the components inside. The molds used for these parts often involve aluminum die casting to provide the necessary strength without adding excess weight.
Chassis and Structural Parts: In EVs, lightweight, yet strong structural components are vital. Parts like the frame or chassis, often made from lightweight metals or composites, require molds that can accommodate their complex shapes and high-performance requirements.
Interior Components: Parts like dashboards, center consoles, and door panels are often produced using plastic injection molds. These components require both aesthetic appeal and functionality, making precise mold design essential.
Cooling System Components: EVs require efficient cooling systems to maintain optimal battery performance. Components such as radiators, pumps, and hoses are produced using various molding techniques such as injection or blow molding.
Conclusion
Automobile molds for electric vehicle components are a cornerstone of EV manufacturing, enabling the production of highly specialized parts that meet the rigorous demands of modern electric transportation. As the EV market grows and evolves, so too will the complexity of the molds required to produce these components. Advanced materials, precise engineering, and cutting-edge technologies such as 3D printing will continue to play an essential role in shaping the future of mold design for electric vehicles. The focus on sustainability and energy efficiency ensures that the molds used for EVs will contribute not only to the performance of the vehicles but also to the broader goal of reducing environmental impact.
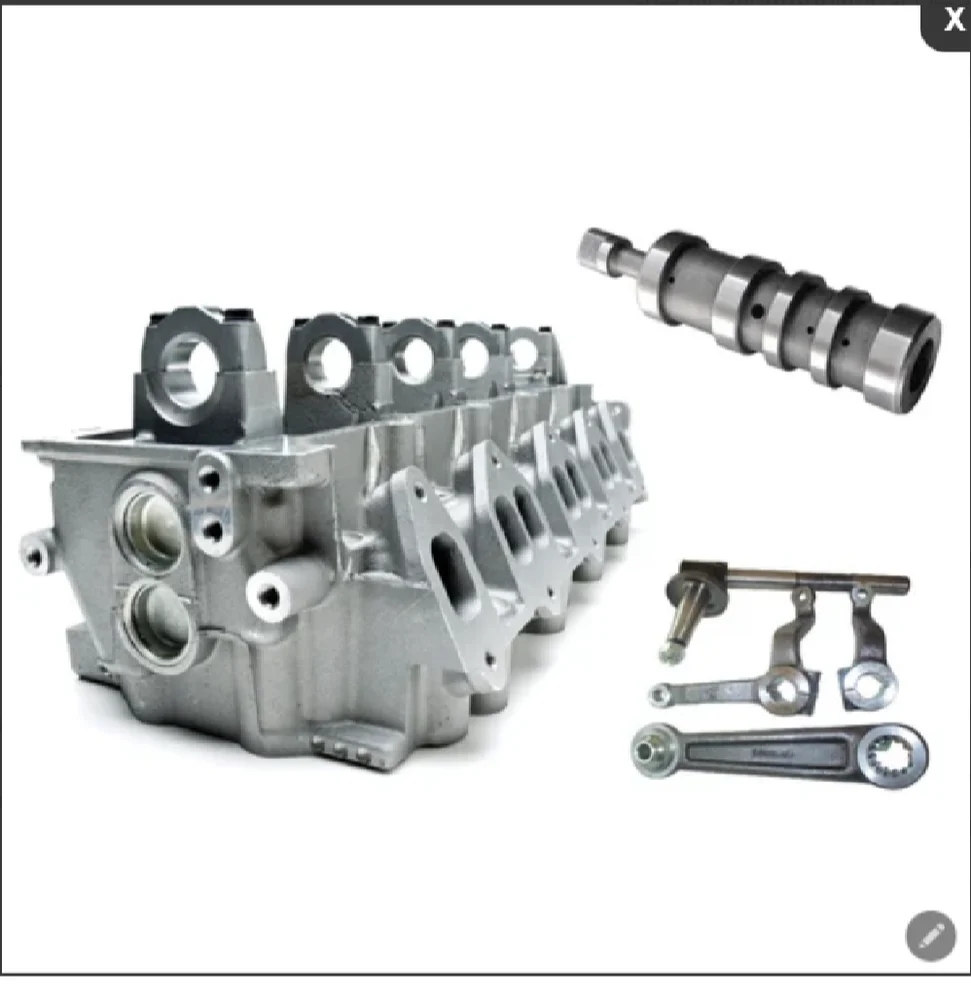