Injection molding is one of the most widely used manufacturing processes for producing plastic parts in high volumes. The process involves injecting molten plastic into a mold cavity under high pressure, where it cools and solidifies to form the final product. One of the critical factors in determining the efficiency and cost-effectiveness of the injection molding process is the cycle time.
What is Injection Molding Cycle Time?
Cycle time in injection molding refers to the total time it takes to complete one full cycle of the injection molding process, from the beginning of the injection phase to the removal of the finished part. This includes several key stages, each contributing to the overall cycle time:
Injection: The molten plastic is injected into the mold cavity under high pressure.
Cooling: The plastic in the mold solidifies as it cools down to the desired temperature.
Ejection: Once the part has cooled and solidified, the mold opens, and the finished part is ejected.
Mold Closing: The mold is closed in preparation for the next injection cycle.
Key Components of Injection Molding Cycle Time
Injection Time: The time it takes to inject the molten plastic into the mold cavity. This step depends on factors like injection speed, the material being used, and the complexity of the mold design.
Cooling Time: This is often the longest part of the cycle, as the plastic needs to solidify before the part can be removed from the mold. Cooling time is influenced by the material’s thermal properties, mold temperature, and part thickness.
Mold Opening and Closing Time: The time required for the machine to open and close the mold for part ejection and injection. The design of the mold and the type of injection molding machine can affect this time.
Ejection Time: The time required to eject the finished part from the mold once the cooling phase is complete.
Idle Time: Any time spent between the steps, such as waiting for the mold to be closed or for the machine to reset.
Factors Affecting Injection Molding Cycle Time
Several factors influence the cycle time, and optimizing these factors can help reduce cycle time, improve efficiency, and lower production costs:
Material Selection: Different materials have different cooling rates. For example, thermoplastics typically cool faster than thermosets, influencing the cycle time.
Mold Design: The design of the mold, including the number and placement of cooling channels, affects the rate at which heat is removed from the molded part. Poor mold design can lead to uneven cooling and longer cycle times.
Part Geometry: The size and complexity of the part being molded significantly affect the cycle time. Parts with thicker walls or intricate features generally require longer cooling times.
Machine Settings: The speed and pressure of injection, as well as the machine’s cycle parameters, directly impact cycle time. Optimizing these settings can reduce unnecessary delays.
Temperature: Both the mold and the material temperature play a significant role. High mold temperatures can reduce cooling time but may lead to longer injection times.
Clamping Force: The force required to keep the mold closed during the injection process can influence cycle time. High clamping force can slow down the overall cycle.
Importance of Cycle Time in Injection Molding
Cost Efficiency: Shorter cycle times mean more parts can be produced in a given time, which helps lower the per-part cost. Optimizing cycle time can lead to a significant reduction in production costs, especially in high-volume manufacturing.
Production Speed: Fast cycle times allow for higher throughput, which is crucial in industries where meeting high demand or tight delivery schedules is essential.
Part Quality: Efficient cycle times can also contribute to better part quality. Consistency in cycle time helps ensure that each part is produced with uniformity in material distribution, cooling, and dimensions.
Machine Utilization: Reducing cycle time increases the efficiency of the injection molding machine, allowing it to run longer and more often without unnecessary delays.
Optimizing Injection Molding Cycle Time
To improve cycle times, manufacturers can adopt several strategies:
Optimizing Mold Design: Ensuring that the mold has a well-designed cooling system can dramatically reduce cooling times. This includes using advanced cooling techniques such as conformal cooling channels or enhancing mold temperature control.
Advanced Materials: Some materials, such as high-performance resins, offer faster cooling rates, allowing for shorter cycle times without compromising part quality.
Adjusting Injection Parameters: Fine-tuning injection speeds, pressures, and temperatures can improve the efficiency of the injection phase, reducing overall cycle time.
Automation: Implementing automated systems for mold handling, part ejection, and other tasks can minimize idle times and improve overall cycle efficiency.
Monitoring and Maintenance: Regular maintenance of the injection molding machine and mold ensures that all components are functioning optimally, helping to prevent delays and inconsistencies that could prolong cycle time.
Conclusion
Understanding and optimizing injection molding cycle time is essential for manufacturers looking to improve production efficiency, reduce costs, and maintain high-quality standards. By carefully analyzing the various components of the cycle, manufacturers can identify opportunities for improvement and streamline the process, resulting in significant benefits to both the manufacturer and the end customer.
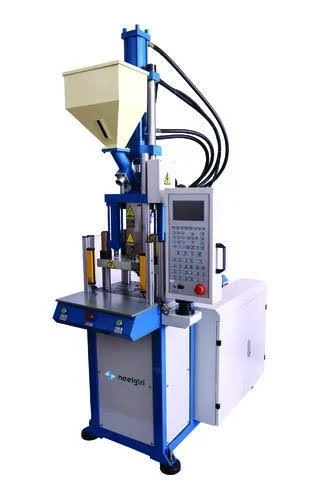