Gas-assisted injection molding (GAIM) is an advanced manufacturing process used to produce lightweight, high-strength automotive parts. It involves injecting gas, usually nitrogen, into the mold during the injection molding process, allowing the creation of hollow sections in plastic components. This technology has gained prominence in the automotive industry due to the increasing demand for lightweight and fuel-efficient vehicles. By reducing part weight without compromising strength or structural integrity, GAIM is helping manufacturers meet stringent fuel economy standards and environmental regulations while maintaining high production rates.
How Gas-Assisted Injection Molding Works
Injection of Plastic: The process begins like traditional injection molding, with plastic being injected into the mold cavity under high pressure.
Gas Injection: Once the cavity is filled with plastic, nitrogen gas is injected into the part under controlled pressure. The gas pushes the molten plastic, creating hollow or foamed sections within the molded part.
Cooling and Solidification: The part is then cooled and solidified, allowing it to retain its shape with the hollow core formed by the gas. The gas is removed, and the part is ejected from the mold.
Advantages of Gas-Assisted Injection Molding for Automotive Parts
Reduced Weight: One of the primary benefits of GAIM is the ability to produce parts with hollow sections. This significantly reduces the weight of automotive components, contributing to fuel efficiency and meeting automotive manufacturers’ goals for reduced vehicle weight.
Improved Strength-to-Weight Ratio: Despite the reduction in material usage, the hollow sections of the parts often maintain or even improve the strength-to-weight ratio of the part, making them suitable for structural components in automobiles.
Material Savings: The reduction in material usage lowers the cost of production, as less plastic is required to create each part.
Complex Geometries: GAIM allows the creation of complex part geometries that might be difficult or costly to achieve with traditional injection molding techniques. This opens up design possibilities for automotive engineers.
Faster Cycle Times: The process can also reduce cycle times compared to conventional molding methods, improving overall production efficiency.
Applications in the Automotive Industry
Bumpers and Fascias: Lightweight bumpers and fascias are critical for improving vehicle fuel efficiency. Gas-assisted injection molding can help create parts with complex geometries while reducing the overall weight, providing both strength and impact resistance.
Dashboard Components: GAIM is increasingly being used to produce lightweight dashboard components, which are designed to withstand impact while reducing the overall weight of the vehicle interior.
Structural Parts: Automotive structural components, such as reinforcements and beams, benefit from the strength and lightness provided by gas-assisted molding. These parts are crucial for vehicle safety and performance.
Door Panels and Trim Pieces: GAIM allows for the production of thin-walled, lightweight door panels and trim pieces that provide aesthetic appeal without adding excessive weight to the vehicle.
Materials Used in Gas-Assisted Injection Molding
Polypropylene (PP): Polypropylene is widely used in the automotive industry due to its lightweight nature, impact resistance, and chemical stability. It is commonly used in bumpers, interior parts, and trim pieces.
Acrylonitrile Butadiene Styrene (ABS): ABS is a versatile plastic known for its toughness, ease of processing, and ability to be used in applications requiring durability, such as dashboards and interior parts.
Polycarbonate (PC): Polycarbonate is used for parts that require high strength, heat resistance, and optical clarity. It is commonly used in automotive lighting and some structural components.
Nylon (PA): Nylon is used in parts requiring high strength and resistance to wear and heat, such as engine components, structural parts, and functional automotive components.
Challenges of Gas-Assisted Injection Molding
Mold Design Complexity: The inclusion of gas channels in the mold requires careful design to ensure uniform gas distribution and pressure control. This can increase the initial investment in mold design and manufacturing.
Gas Control: Maintaining precise control over the gas injection pressure and timing is critical to ensure the desired part quality. Any inconsistency can lead to defects such as gas bubbles, weak spots, or dimensional inaccuracies.
Material Compatibility: Not all materials are suitable for gas-assisted injection molding. The chosen material must have adequate flow properties and be compatible with the gas to avoid defects.
Cost of Equipment: The initial setup cost for gas-assisted injection molding, including specialized molds and gas injection systems, can be higher than traditional molding methods. However, the cost savings in materials and cycle times can offset this over the long term.
Future Trends in Gas-Assisted Injection Molding
Integration with Hybrid and Electric Vehicles: As the automotive industry shifts toward hybrid and electric vehicles, the demand for lightweight components continues to grow. Gas-assisted injection molding can play a significant role in producing parts for these next-generation vehicles, where weight reduction is even more critical for battery efficiency and overall performance.
Advanced Composite Materials: The development of new composite materials designed for use in gas-assisted injection molding will open up new possibilities for creating lightweight, high-strength automotive parts with unique properties.
Sustainability: As environmental concerns become more prominent, the ability of gas-assisted injection molding to reduce material waste and energy consumption is expected to become a key selling point. Additionally, the use of recycled materials in GAIM could further enhance its sustainability credentials.
Conclusion Gas-assisted injection molding is revolutionizing the production of lightweight automotive parts. By reducing material usage and part weight while maintaining strength and structural integrity, GAIM contributes significantly to vehicle fuel efficiency and performance. Its ability to create complex geometries, coupled with material and cycle time savings, makes it a valuable tool in modern automotive manufacturing. Despite some challenges, the future of GAIM looks promising, with growing applications in electric and hybrid vehicles and ongoing advances in material science.
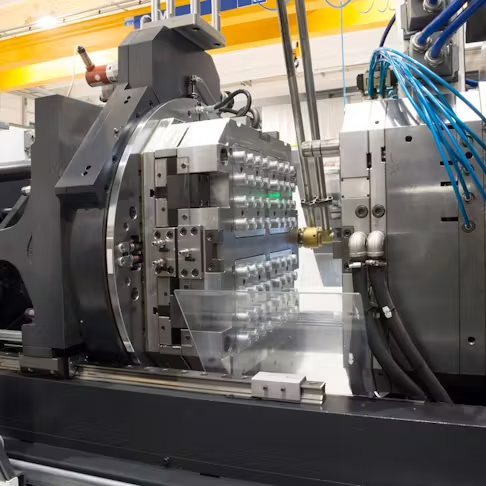