Injection mold maintenance is a critical part of ensuring the efficiency, quality, and longevity of the molds used in injection molding processes. Proper maintenance minimizes downtime, reduces defects, and extends the lifespan of the mold, ensuring consistent production. Here are some key considerations for effective injection mold maintenance:
1. Regular Cleaning and Inspection
Cleaning: Regular cleaning is vital to prevent debris, polymer buildup, or residue from affecting the mold’s performance. A thorough cleaning after each production run helps maintain mold quality and reduces contamination during the next cycle.
Inspection: Mold components should be inspected regularly for wear and tear. Checking for cracks, corrosion, and misalignment is essential to identify any issues before they affect production. Regular inspections help ensure the mold continues to produce high-quality parts without defects.
2. Lubrication
Proper lubrication of moving parts, like slides, cores, and ejector pins, reduces friction and wear. It’s essential to use the right lubricants in the right areas and to clean any excess lubricant that may accumulate. This helps to prevent rusting, jamming, and wear in critical mold areas.
3. Temperature Control
Cooling System Maintenance: The cooling channels play a significant role in controlling the temperature of the mold during the injection molding process. If cooling channels are clogged or not functioning correctly, it can lead to uneven cooling, which affects the quality of the molded parts. Regularly checking and cleaning cooling channels ensures optimal performance.
Heater Maintenance: The heaters in the mold (if used) need to be regularly checked and calibrated. Overheating or underheating can lead to poor part quality, material degradation, or damage to the mold.
4. Wear and Tear on Critical Components
Ejector Pins: These components often experience significant wear due to friction and the stress of ejecting molded parts. Regularly inspecting and replacing ejector pins when necessary is essential to maintain mold performance.
Cavities and Cores: The cavities and cores that form the shape of the molded part can become worn over time. Regular checks for wear, especially in high-production runs, are essential to avoid dimensional inaccuracies and defects in the molded parts.
5. Alignment and Calibration
Proper Alignment: Ensuring that the mold is properly aligned during the assembly process is key to preventing improper sealing and part misformation. Misalignment can lead to flash, part defects, or even mold damage.
Calibration: It’s crucial to calibrate the mold regularly, especially after maintenance or repairs. Calibration ensures that all parts of the mold are in their correct positions and can operate without error during the injection process.
6. Environmental Conditions
Storage Conditions: After production runs, molds should be properly stored to avoid damage. Molds should be stored in clean, dry, and controlled environments to avoid rust, contamination, or damage from extreme temperature fluctuations.
Humidity Control: Molds should be kept in an environment with controlled humidity to prevent moisture from affecting the mold’s components and materials.
7. Preventive Maintenance Schedule
Establishing a preventive maintenance (PM) schedule is crucial for ensuring that the mold stays in optimal condition. Regularly scheduled checkups should be implemented based on factors like the type of material used, the production run length, and the mold’s complexity.
Logbook: Maintaining a logbook for every mold, documenting inspections, repairs, and replacements, is important for tracking mold history and predicting future maintenance needs.
8. Material Compatibility
Some materials can cause more wear on molds than others. For instance, abrasive materials like glass-filled resins can wear down mold surfaces quickly. It’s important to understand the material being molded and how it interacts with the mold to anticipate necessary maintenance.
9. Component Replacement
Regularly check for parts that may need to be replaced due to wear. These include components like seals, pins, bushings, and plates. Timely replacement of worn-out components ensures smooth mold operation and avoids larger, more expensive repairs in the future.
10. Training and Expertise
Skilled Technicians: Injection mold maintenance requires a high level of technical expertise. Ensuring that personnel are properly trained to perform maintenance tasks and troubleshoot issues is vital.
Continual Education: Staying updated on the latest advancements in mold technology, materials, and maintenance techniques can help prevent issues and optimize mold performance.
Conclusion
Effective injection mold maintenance is crucial for ensuring consistent product quality, reducing downtime, and prolonging the lifespan of molds. By focusing on key considerations such as regular cleaning, inspection, proper lubrication, temperature control, and alignment, manufacturers can optimize their injection molding processes and avoid costly repairs. Adopting a proactive approach through preventive maintenance, skilled technicians, and environmental control ensures that molds continue to operate efficiently for years.
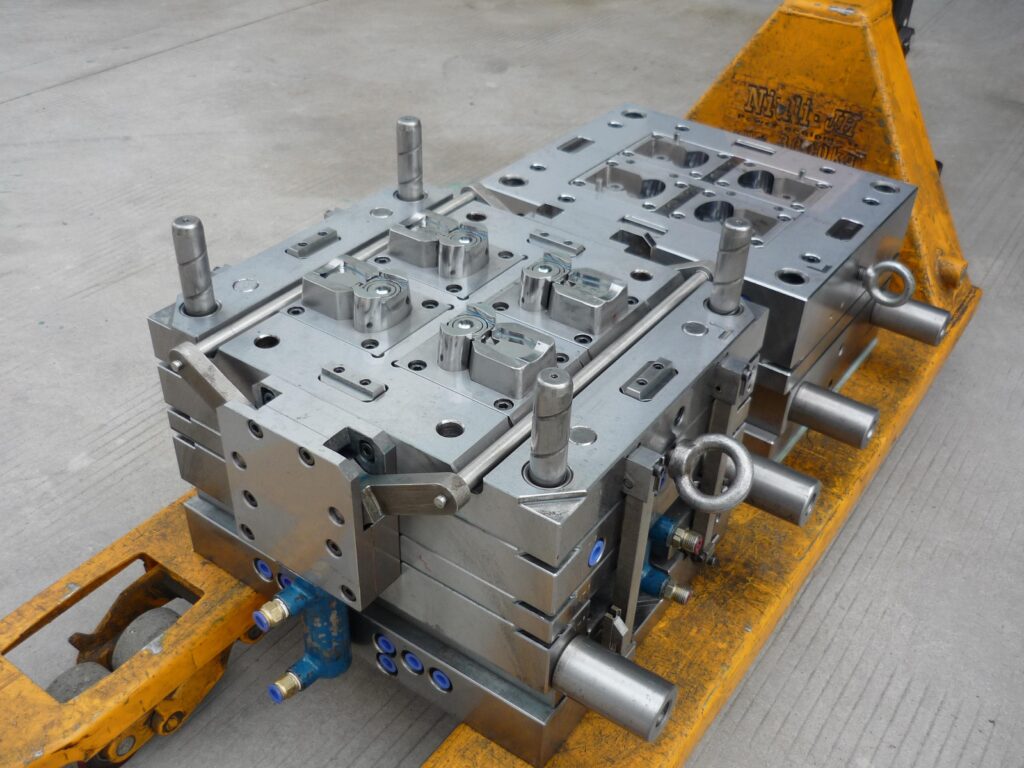