Polyvinyl chloride (PVC) is one of the most widely used thermoplastics in various applications such as pipes, window profiles, flooring, and medical devices. To optimize its properties for different uses, various additives are incorporated into PVC formulations during the molding process. These additives can enhance the material’s performance in terms of strength, flexibility, weather resistance, processing efficiency, and more. Below are some key additives commonly used in PVC molding to enhance its performance:
1. Plasticizers
Plasticizers are essential additives in PVC molding to increase the flexibility, workability, and processability of rigid PVC. These compounds reduce the glass transition temperature of PVC, making it softer and more pliable.
Common Types:
Dioctyl phthalate (DOP)
Diisononyl phthalate (DINP)
Epoxidized soybean oil (ESBO)
Plasticizers are used in applications like flexible tubing, flooring, and upholstery materials.
2. Stabilizers
PVC is susceptible to degradation due to heat, light, and environmental factors during processing and use. Stabilizers are incorporated into PVC formulations to protect it from thermal degradation and UV radiation.
Heat Stabilizers: These protect the polymer from decomposition when exposed to high temperatures. The most common heat stabilizers include calcium-zinc, barium-cadmium, and tin-based stabilizers.
UV Stabilizers: UV stabilizers prevent the degradation caused by ultraviolet light exposure, improving the weatherability of PVC, especially in outdoor applications. Hindered amine light stabilizers (HALS) and UV absorbers are commonly used.
3. Impact Modifiers
Impact modifiers are used to improve the toughness and resistance to cracking of PVC under stress or low temperatures. These modifiers are particularly important in applications where PVC needs to withstand mechanical stress.
Acrylonitrile Butadiene Styrene (ABS)
Methyl Methacrylate Butadiene Styrene (MBS)
By modifying the molecular structure of PVC, these impact modifiers help maintain material integrity under harsh conditions.
4. Processing Aids
Processing aids are used to improve the flow properties of PVC during molding, extrusion, and other processing techniques. They help reduce processing time and improve surface finish, while also preventing melt fracture.
Lubricants: Internal and external lubricants reduce friction between the polymer and machinery during processing. Calcium stearate and zinc stearate are examples of lubricants used to enhance the processing efficiency.
Flow Improvers: These additives help improve the melt flow of PVC, making the material easier to mold into complex shapes.
5. Flame Retardants
In applications where PVC is exposed to fire hazards, flame retardants are added to improve its resistance to combustion. These additives lower the flammability of PVC and reduce the risk of fire spreading.
Organophosphates
Halogenated flame retardants
Hydroxides and hydrated alumina
Flame-retardant PVC is often used in the construction, automotive, and electrical industries.
6. Fillers
Fillers are often incorporated into PVC to reduce material costs, enhance mechanical properties, and improve the dimensional stability of the material. These fillers are particularly useful in rigid PVC applications.
Calcium carbonate: Commonly used for cost reduction and improving stiffness.
Talc: Enhances dimensional stability and improves processing.
Glass fibers: Used for reinforcing the polymer and improving its strength.
7. Antioxidants
Antioxidants are added to PVC to prevent the degradation of the polymer during processing or during its lifetime due to oxidative reactions. They help maintain the material’s properties by inhibiting oxidative damage caused by heat and light.
Secondary antioxidants such as phosphites and thioethers work synergistically with primary antioxidants to extend the product’s longevity.
8. Colorants and Pigments
Colorants and pigments are used in PVC molding to provide desired aesthetic properties to the final product. They allow for a wide range of colors to be achieved in PVC products, including pipes, flooring, and consumer goods.
Organic pigments: For a wide range of colors.
Inorganic pigments: For more stable and durable colors that are resistant to fading.
9. Antimicrobials
In some applications, especially in medical and healthcare-related products, PVC can be treated with antimicrobial additives to prevent the growth of bacteria, mold, and mildew. These additives are important for products such as medical tubing, food packaging, and appliances in humid environments.
10. Antistatic Agents
In certain applications, static electricity buildup can be a concern, especially in electronics or clean-room environments. Antistatic agents are added to PVC formulations to reduce static buildup by increasing the electrical conductivity of the material.
Fatty acid amides and alkyl sulfonates are commonly used antistatic agents.
11. Blowing Agents
Blowing agents are incorporated into PVC formulations to reduce the material’s density by creating a cellular structure. This can reduce the weight of the final product and improve insulation properties. These additives are often used in the production of foam boards, panels, and pipes.
Azodicarbonamide
Dinitrosopentamethylenetetramine (DPT)
Conclusion
Additives play a critical role in enhancing the performance of PVC in various molding applications. They are chosen based on the desired properties of the final product and the specific demands of the application. Whether improving flexibility, durability, resistance to environmental factors, or processing efficiency, the right combination of additives ensures that PVC can meet the needs of diverse industries while maintaining cost-effectiveness.
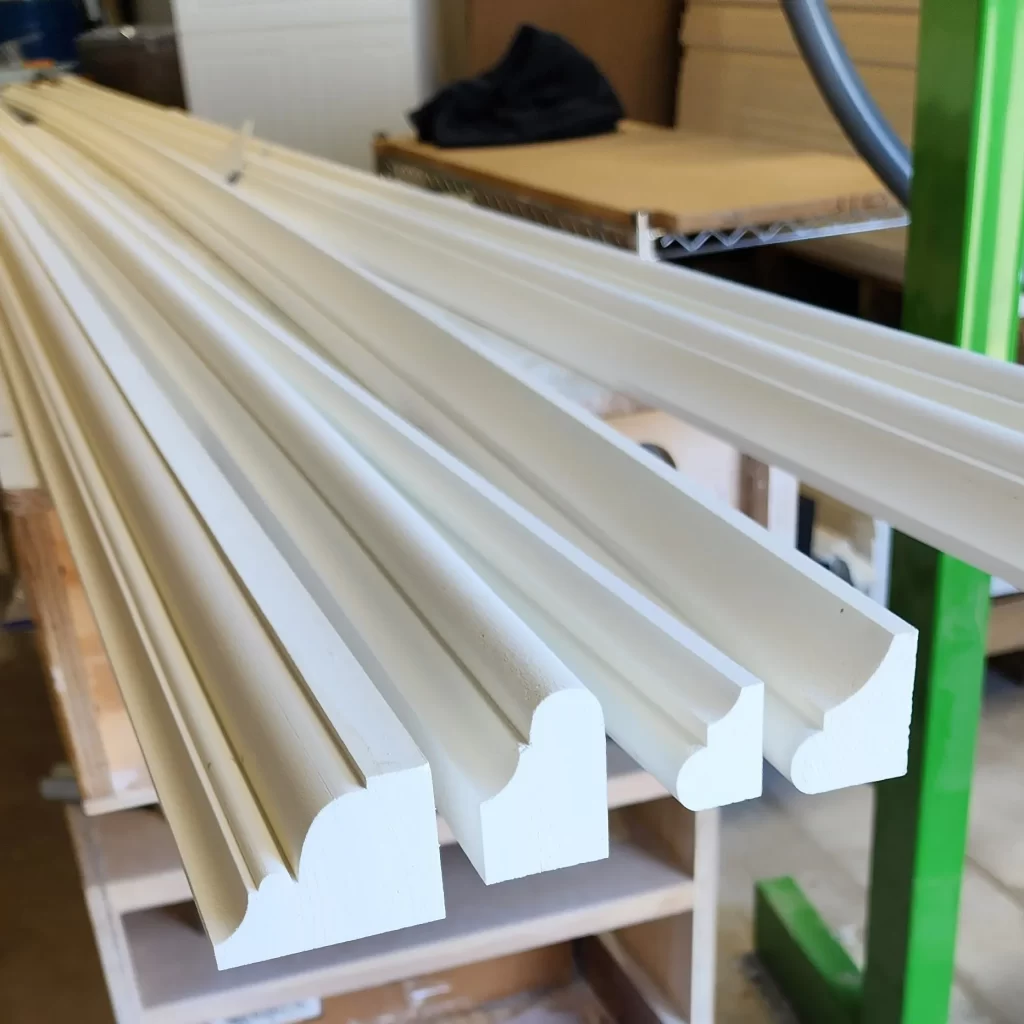