Injection molding has long been a cornerstone of mass production for plastic components due to its efficiency, repeatability, and ability to produce complex geometries. However, as industry demands continue to evolve, so too do the manufacturing techniques associated with it. Advanced manufacturing techniques in injection molding are enhancing precision, speed, sustainability, and design freedom. These innovations are revolutionizing how manufacturers approach product development and production.
1. Scientific Molding and Data-Driven Processes
Scientific molding is a data-driven approach that focuses on understanding and controlling each aspect of the injection molding process through systematic experimentation and analysis. It relies on in-depth process monitoring to optimize parameters such as:
Fill time
Pressure and temperature profiles
Viscosity curves
Clamp force requirements
This results in higher quality parts with fewer defects, shorter cycle times, and better reproducibility.
2. Micro Injection Molding
Micro injection molding allows for the production of extremely small and precise plastic parts, often used in:
Medical devices (e.g., microfluidic chips)
Electronics (e.g., miniature gears)
Aerospace components
Advanced mold designs and specialized micro-scale tooling are essential to this process. It demands ultra-fine tolerances and precise control over pressure and temperature.
3. Multi-Material and Overmolding
Multi-material injection molding, including overmolding and two-shot molding, enables the combination of different materials into a single part. This technique is widely used for:
Ergonomic handles with soft-touch surfaces
Electronic housings with integrated seals
Automotive parts with both rigid and flexible elements
It enhances product performance and aesthetics while reducing assembly steps.
4. Rapid Tooling and Additive Manufacturing for Molds
Rapid tooling involves the use of 3D printing and other digital manufacturing methods to produce mold components quickly and cost-effectively. Key advantages include:
Faster prototyping and iteration
Lower initial tooling costs
Customization for low-volume production
Conformal cooling channels, enabled by additive manufacturing, improve cooling efficiency and reduce cycle time significantly.
5. Gas-Assisted Injection Molding (GAIM)
GAIM involves injecting an inert gas (usually nitrogen) into the mold during the injection process. This forms hollow sections within the part, resulting in:
Lighter components
Reduced material usage
Enhanced dimensional stability
Lower risk of sink marks
It’s commonly used in producing automotive trim, handles, and furniture parts.
6. Process Automation and Smart Molding
Industry 4.0 technologies have led to the rise of smart injection molding, where machines are integrated with:
Real-time sensors
AI-powered process optimization
Predictive maintenance systems
IoT-enabled quality control
This enhances efficiency, reduces downtime, and ensures consistent part quality across production runs.
7. Metal Injection Molding (MIM) and Ceramic Injection Molding (CIM)
These are advanced forms of injection molding used for producing metal or ceramic parts with complex geometries:
Ideal for aerospace, medical, and automotive industries
Combines the flexibility of plastic molding with the strength of metal/ceramics
Post-processing includes debinding and sintering to achieve final material properties
8. Sustainable and Bio-Based Materials
There is growing use of biodegradable polymers, recycled materials, and closed-loop systems in injection molding:
PLA, PHA, and other compostable materials are replacing traditional plastics
Regrind and waste minimization strategies are becoming standard
Sustainable design practices are integrated from the concept stage
Conclusion
Advanced manufacturing techniques in injection molding are reshaping the industry by boosting efficiency, enabling greater design complexity, and supporting sustainable production practices. Companies that embrace these technologies are better positioned to meet the challenges of modern product development while delivering high-quality, cost-effective solutions.
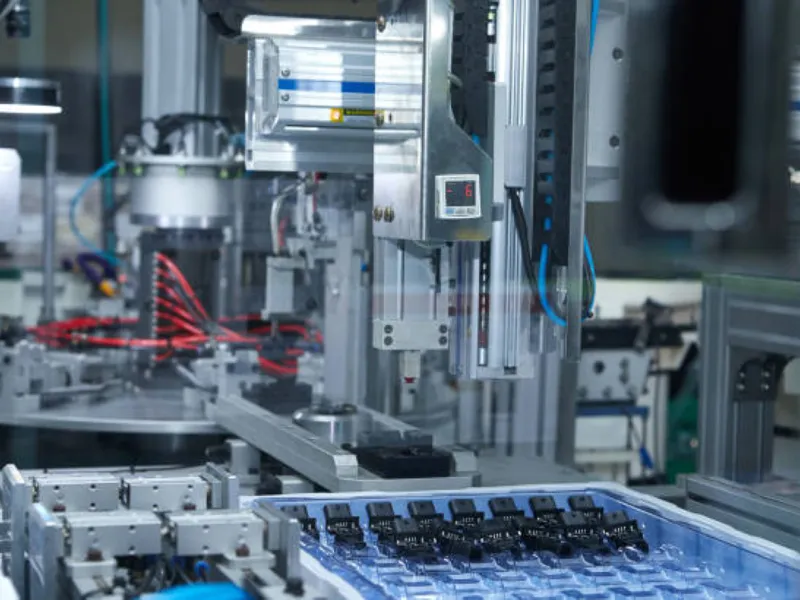