In the rapidly evolving automotive industry, materials science plays a pivotal role in enhancing performance, fuel efficiency, and safety. Among these materials, advanced polymers have emerged as indispensable for producing durable, lightweight, and high-performance automotive parts. These innovative materials are engineered to withstand harsh environments, reduce vehicle weight, and improve fuel efficiency without compromising on safety or functionality.
1. The Need for Advanced Polymer Materials
Traditional materials like metals (steel and aluminum) have long been dominant in automotive manufacturing. However, the push for lighter vehicles, lower emissions, and greater design flexibility has led to the adoption of high-performance polymers. Key drivers include:
Fuel efficiency: Every 10% reduction in vehicle weight can lead to a 6–8% improvement in fuel economy.
Corrosion resistance: Unlike metals, polymers are naturally resistant to rust and chemical corrosion.
Design freedom: Polymers offer superior moldability for complex geometries and integration of multiple components.
2. Types of Advanced Polymers Used in Automotive Applications
a. Thermoplastics
These are polymers that soften when heated and harden when cooled, making them recyclable and versatile.
Polyamide (PA) – Commonly known as nylon, used in engine covers, air intake manifolds, and under-the-hood components.
Polyphenylene sulfide (PPS) – Known for high chemical and thermal resistance, ideal for electrical connectors and pump housings.
Polyether ether ketone (PEEK) – Extremely high-performance thermoplastic used in precision parts that require high heat and wear resistance.
b. Thermosetting Polymers
These materials cure into a solid form and cannot be re-melted. They are known for their rigidity and thermal stability.
Epoxy resins – Widely used in composite materials for body panels and structural components.
Phenolic resins – Used in brake pads, clutch plates, and under-the-hood thermal shielding.
c. Elastomers
Rubber-like polymers used for flexibility and impact resistance.
Thermoplastic elastomers (TPEs) – Applied in seals, gaskets, and flexible interior trims.
Silicone rubber – Excellent thermal stability, often used in engine bay seals and electrical insulation.
3. Key Applications of Advanced Polymers in Automotive Parts
Under-the-hood components: High-temperature-resistant polymers are crucial for engine parts, housings, and connectors.
Exterior parts: Bumpers, grilles, and panels made of impact-resistant thermoplastics reduce vehicle weight and improve crash performance.
Interior components: Lightweight polymers enhance aesthetics, noise reduction, and comfort.
Structural composites: Carbon fiber-reinforced polymers are used in high-performance sports cars and EVs for structural strength and weight reduction.
4. Advantages of Using Advanced Polymers
Weight reduction: Leading to improved fuel efficiency and extended EV range.
Durability: Resistance to wear, corrosion, and environmental stress.
Cost-effectiveness: Lower manufacturing and maintenance costs due to longevity and ease of processing.
Sustainability: Increasing use of recyclable and bio-based polymers to reduce environmental impact.
5. Challenges and Future Trends
Despite the many benefits, some challenges remain:
Thermal limitations: Some polymers cannot withstand the highest temperatures like metals can.
Recycling complexity: Especially in composite materials.
Material cost: High-performance polymers can be expensive compared to standard plastics.
Future trends include:
Development of self-healing and smart polymers.
Bio-based polymers from renewable sources.
Improved recyclability and circular economy integration.
Integration with additive manufacturing (3D printing) for rapid prototyping and production.
Conclusion
Advanced polymer materials have revolutionized automotive part design and manufacturing. Their lightweight, durable, and versatile nature makes them essential in modern vehicles, particularly as the industry shifts toward electric mobility and sustainable solutions. As polymer science continues to evolve, we can expect even more innovative applications that drive the next generation of durable, efficient, and eco-friendly automotive technologies.
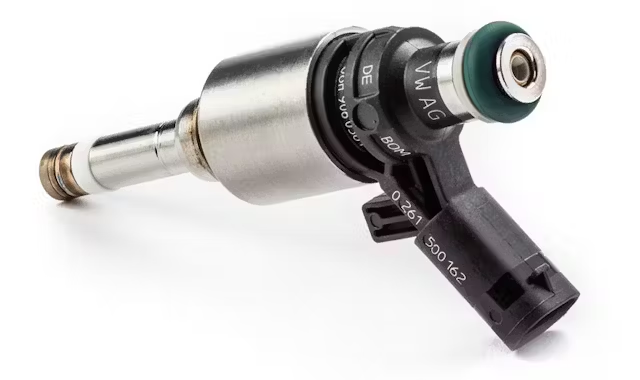