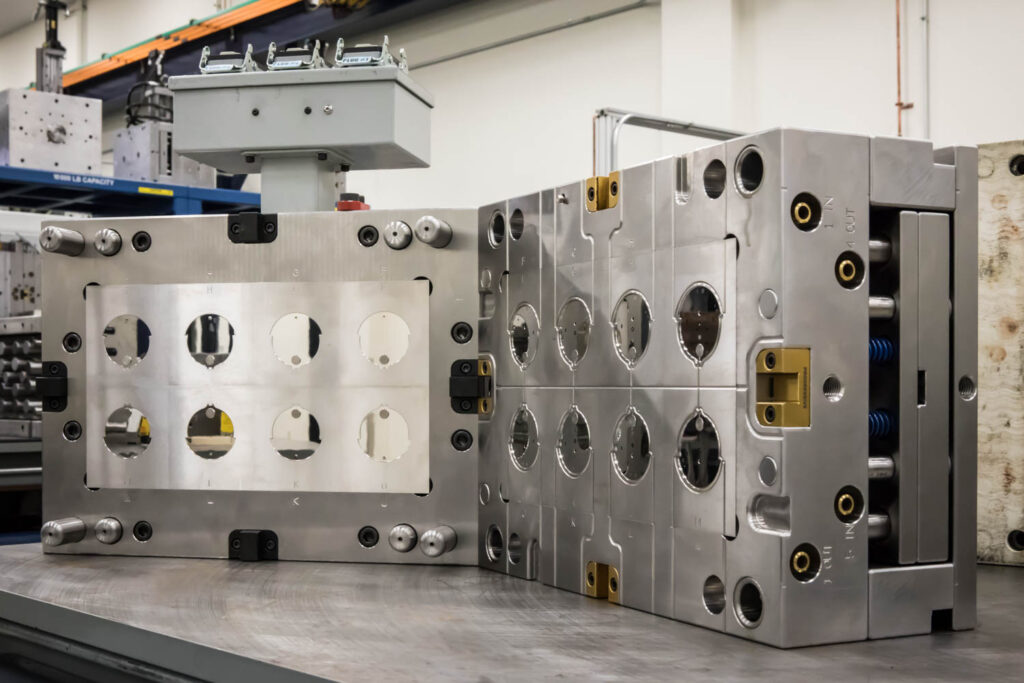
Polyvinyl chloride (PVC) molding has evolved significantly with the advent of advanced technologies, enabling manufacturers to produce high-quality, durable, and precisely engineered components. PVC is widely used in industries such as construction, automotive, healthcare, and consumer goods due to its versatility, chemical resistance, and cost-effectiveness. Innovations in PVC molding technologies have enhanced efficiency, improved product quality, and expanded the range of applications for PVC-based products.
One of the most notable advancements in PVC molding is precision injection molding, which allows manufacturers to create intricate and complex parts with minimal defects. Modern injection molding machines are equipped with enhanced process control systems, ensuring precise temperature regulation, optimized injection pressure, and consistent material flow. These improvements help prevent common issues such as warping, sink marks, and surface defects, resulting in superior-quality PVC components.
Another key innovation is bi-layer and multi-component molding, which enables the production of PVC parts with multiple material layers or integrated features. This technique is particularly useful for manufacturing products that require different textures, hardness levels, or enhanced functionality. For example, in the automotive industry, bi-layer molding allows the integration of soft-touch PVC surfaces with rigid structural components, enhancing both durability and aesthetics.
The introduction of low-pressure and gas-assisted PVC molding has also revolutionized the industry. Low-pressure molding reduces material stress and prevents defects, making it ideal for manufacturing large, thin-walled PVC parts. Gas-assisted molding, on the other hand, improves material distribution, minimizes shrinkage, and reduces overall material usage, leading to cost savings and enhanced part performance. These technologies are particularly beneficial for applications in the construction and medical sectors, where precision and material efficiency are critical.
Sustainability has become a driving force in PVC molding advancements. Eco-friendly PVC formulations, including lead-free and phthalate-free compounds, have been developed to meet stringent environmental and safety regulations. Additionally, recycled PVC processing techniques have improved, enabling manufacturers to incorporate post-consumer and post-industrial recycled PVC into new products without compromising quality. These innovations contribute to reducing plastic waste and promoting circular economy practices.
3D-printed PVC molds and rapid prototyping have also transformed the industry by allowing faster and more cost-effective mold development. Additive manufacturing technologies enable the creation of complex mold designs with greater flexibility, reducing lead times and prototyping costs. This advancement is particularly beneficial for small-batch production, custom PVC components, and design validation processes.
Furthermore, smart manufacturing and automation have enhanced efficiency in PVC molding operations. The integration of IoT sensors, AI-driven process monitoring, and automated robotic systems ensures real-time quality control, reduces human error, and improves production speed. These innovations allow manufacturers to achieve greater consistency, optimize energy consumption, and streamline the entire PVC molding process.
As technology continues to evolve, advanced PVC molding techniques are expected to further improve product quality, production efficiency, and environmental sustainability. These innovations ensure that PVC remains a versatile and indispensable material in modern manufacturing, supporting industries with high-performance and cost-effective solutions.