Automobile mold testing plays a crucial role in the automotive industry, ensuring that components meet stringent quality standards before they are used in vehicle production. The molds used for automobile parts, such as dashboards, bumpers, engine components, and body panels, are complex and require precision to ensure the final products are durable, functional, and aesthetically appealing. Below, we explore the importance of automobile mold testing, the processes involved, and the role of quality control and precision in this critical phase of manufacturing.
1. The Importance of Mold Testing in Automobile Manufacturing
Molds are used to create various components of a vehicle, and the process of mold testing is designed to identify any defects or inconsistencies early on. The purpose is to ensure that the molds produce components that meet both functional and aesthetic standards. For example, in the case of plastic injection molding, ensuring that the mold has the right temperature, pressure, and material flow is critical for producing high-quality, durable parts.
Consistency and Accuracy: Mold testing helps ensure that each part produced is consistent in size, shape, and quality. This is crucial for parts that must fit together perfectly, such as body panels or interior components.
Material Integrity: Mold testing checks if the materials used during molding retain their properties, ensuring that parts won’t fail prematurely or deteriorate under extreme conditions (heat, cold, or stress).
Reducing Waste and Cost: Detecting issues in the mold early reduces the need for costly rework or replacement of parts, minimizing waste and ensuring production efficiency.
2. Types of Automobile Mold Testing
There are several types of testing methods used to ensure molds meet automotive industry standards. These tests vary depending on the material being molded, the type of mold used, and the specific component being produced.
a. Dimensional Testing
Dimensional testing ensures that the molded parts meet the required specifications in terms of size and shape. This test often includes the use of precision measuring tools like calipers, coordinate measuring machines (CMM), or 3D scanners.
Purpose: To ensure that the part fits within the designated tolerances.
Process: After the mold is created, a sample part is tested to confirm that all the critical dimensions are accurate. If any deviations are found, adjustments are made to the mold.
b. Structural Integrity Testing
This type of testing is used to verify that the molded part will withstand the mechanical stresses it will experience in its application. Parts like engine components, suspension parts, and structural elements need to be tested for strength, durability, and resistance to deformation.
Methods: Testing methods might include impact resistance tests, tensile strength tests, and fatigue tests.
Purpose: To ensure that the part can handle the mechanical forces it will encounter during its lifetime without failing.
c. Material Compatibility Testing
Automobile parts often require specific materials to meet strength, weight, and durability requirements. Testing ensures that the materials used in the mold (plastic, metal, composites) meet these standards and perform well under operational conditions.
Purpose: To test the material’s properties, including its resistance to heat, chemicals, UV exposure, and weathering.
Process: Samples of the material are subjected to environmental tests such as heat aging, corrosion tests, and accelerated weathering.
d. Cycle Time and Efficiency Testing
Mold efficiency and cycle time are also critical factors in automotive mold testing. The cycle time is the amount of time it takes for the mold to produce a part, from the injection of material to the removal of the final product.
Purpose: To optimize the manufacturing process, reduce production time, and lower costs.
Process: This testing monitors the mold’s efficiency during production, ensuring that parts are being produced within an acceptable timeframe while maintaining quality.
3. Quality Control in Mold Testing
Quality control (QC) is integral to ensuring that the molds and the parts they produce meet the high standards expected in the automotive industry. QC in mold testing involves:
Inspection and Verification: QC inspectors conduct visual checks and measurements of the molded parts, often using automated systems or manual processes.
Process Monitoring: Real-time monitoring systems track parameters such as temperature, pressure, and material flow to ensure consistency throughout production.
Root Cause Analysis: When defects are found, QC teams perform detailed investigations to identify and resolve issues, which can range from material inconsistencies to mold wear.
Regular audits and standardized quality procedures are part of the QC framework, ensuring compliance with international standards such as ISO 9001, TS 16949, and other relevant certifications in the automotive industry.
4. Precision in Mold Design and Testing
Precision is at the heart of automotive mold testing. The automotive industry relies heavily on precise, high-quality components, as even small deviations in shape or size can lead to significant problems in assembly, performance, and safety.
Precision Engineering: The mold must be designed with exacting precision to ensure that the final part fits perfectly with other components. Computer-aided design (CAD) software and advanced simulations are often used to create and test the mold design before physical testing.
Microscopic Analysis: In some cases, high-precision tests are conducted using microscopic imaging to detect imperfections or irregularities that are not visible to the naked eye but could impact the functionality of the part.
5. Advancements in Mold Testing Technology
As technology continues to advance, so too do the methods used for automobile mold testing. New technologies like 3D printing, digital twins, and advanced robotics are enhancing the precision and efficiency of mold testing:
3D Printing: Rapid prototyping allows manufacturers to quickly produce molds or part samples for testing, cutting down on lead time and cost.
Digital Twins: These virtual models of molds help simulate and optimize the entire molding process, predicting potential issues before they arise in real-world testing.
Robotics and Automation: Automated systems are being used to perform repetitive tasks such as dimensional checks, increasing the speed and accuracy of mold testing.
6. Conclusion
Automobile mold testing is a critical phase in the automotive manufacturing process, ensuring that molds produce parts that are not only functional but also safe, durable, and cost-effective. The combination of quality control measures, advanced testing technologies, and precision engineering ensures that every part meets the rigorous standards of the automotive industry. As automotive technologies continue to evolve, so too will the methods and tools used for mold testing, driving innovation in the production of high-quality, reliable vehicles.
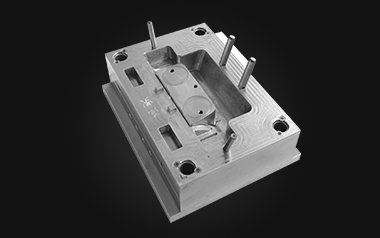