The global shift toward electric vehicles (EVs) has driven significant changes across the automotive manufacturing landscape. One of the often-overlooked yet critically important areas undergoing transformation is automotive mold design and manufacturing. As automakers innovate to meet the unique needs of EVs—lighter weight, compact systems, thermal management, and advanced materials—mold technologies are evolving in tandem. Below are key innovations shaping the future of mold making for EV components.
1. Lightweight Material Molding
EV efficiency depends heavily on vehicle weight. To improve range and performance, automakers are increasingly using lightweight materials such as:
High-performance plastics
Carbon-fiber-reinforced polymers (CFRPs)
Aluminum and magnesium alloys
Mold makers are adapting by developing high-precision tooling capable of handling these materials, including multi-cavity and hybrid molds designed to minimize cycle time and maintain structural integrity.
2. Integrated Component Design
Unlike internal combustion vehicles, EVs often integrate multiple functions into fewer components to save space and reduce complexity. This requires:
Multi-functional mold designs
Insert molding and overmolding techniques for combining conductive and insulating materials
Conformal cooling channels in molds to manage thermal behavior during production
This integration reduces part count and enhances reliability, while posing new challenges for mold precision and durability.
3. Battery Housing and Thermal Management Molds
EV batteries require robust, heat-resistant enclosures. Innovations in mold design support:
High-pressure die casting for aluminum housings
Injection molding of thermally conductive plastics
Complex venting and sealing features integrated into the mold
Advanced tooling now enables the production of battery casings with integrated channels for liquid cooling or passive heat dissipation.
4. Advanced Simulation and Digital Twins
Modern mold development for EVs leverages simulation technologies, such as:
Mold flow analysis
Finite element analysis (FEA)
Digital twin models for virtual testing
These tools reduce prototyping time, improve first-time quality, and allow real-time mold performance monitoring—critical for EV manufacturing where speed to market is vital.
5. Sustainable and Smart Mold Solutions
Sustainability is another major driver. Innovations include:
Recyclable mold materials
Additive manufacturing (3D printing) for mold inserts
Smart molds with embedded sensors for predictive maintenance
Such solutions not only reduce environmental impact but also support circular economy goals in EV production.
6. Automation and High-Volume Production
As EV demand grows, mold innovations are enabling higher throughput with:
Fully automated mold handling systems
Quick-change tooling
Modular molds for customizable component variants
Automation enhances consistency and quality while reducing labor costs, a crucial factor for mass EV production.
Conclusion
Automotive mold innovations are playing a pivotal role in the evolution of electric vehicles. From enabling lightweight structures to integrating advanced functions and improving sustainability, mold makers are at the forefront of EV manufacturing transformation. As EV technologies continue to mature, ongoing collaboration between automotive OEMs, tier suppliers, and mold manufacturers will be essential to stay competitive and meet the challenges of the next-generation mobility landscape.
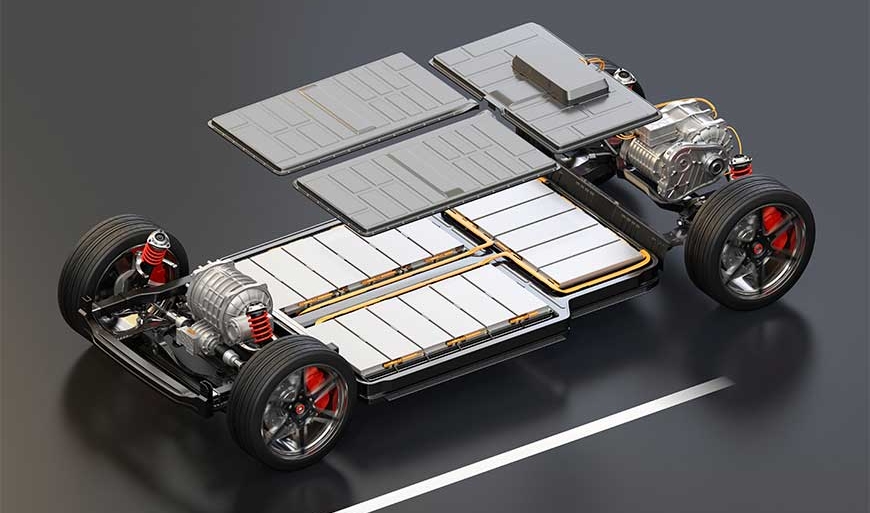