Automotive Mold Lifecycle Management (MLM) refers to the systematic process of managing the entire lifecycle of molds used in automotive manufacturing. Molds are critical tools for producing plastic, metal, and composite components in high volumes with consistent quality. Effective MLM ensures reduced downtime, extended mold life, improved product quality, and optimized production costs.
1. Mold Design and Development
Requirements Analysis: Understand the specifications of the automotive part, including materials, tolerances, and production volume.
CAD Design: Create detailed mold designs using CAD tools, focusing on manufacturability, cooling systems, and ejection mechanisms.
Simulation and Validation: Use CAE tools for mold flow analysis, warpage prediction, and cooling efficiency testing to validate the design before manufacturing.
Design for Maintainability: Incorporate features that simplify future maintenance, repair, and tracking.
2. Mold Manufacturing
Material Selection: Choose high-grade tool steel or other durable materials based on production needs and part complexity.
Precision Machining: Use CNC, EDM, and other high-precision processes to fabricate mold components.
Assembly and Inspection: Assemble the mold and inspect for dimensional accuracy, surface finish, and functional performance.
Trial Runs: Conduct sample production runs to test mold performance and make adjustments as needed.
3. Mold Deployment and Production
Installation: Set up the mold in the injection molding machine or press with proper alignment and calibration.
Process Optimization: Tune machine parameters for optimal cycle time, quality, and material usage.
Monitoring and Data Collection: Use IoT-enabled sensors and systems to monitor mold temperature, pressure, and cycle counts in real time.
4. Mold Maintenance and Repair
Preventive Maintenance: Regularly scheduled cleaning, lubrication, and inspection to prevent wear and tear.
Corrective Maintenance: Repair or replace worn components (e.g., ejector pins, inserts, seals) when defects or inefficiencies are observed.
Maintenance Records: Maintain a digital log of service history, repairs, and modifications for each mold.
5. Mold Storage and Preservation
Storage Conditions: Clean, dry, and climate-controlled environments to prevent corrosion and contamination.
Protective Measures: Apply anti-rust coatings, use protective covers, and secure parts to prevent damage.
Inventory Management: Use barcoding or RFID systems for mold tracking and retrieval.
6. Mold Retirement and Recycling
Assessment for Retirement: Evaluate molds based on wear, performance decline, or obsolescence due to product changes.
Reconditioning: Refurbish molds if economically viable or adapt for new part production.
Recycling: Recycle mold materials responsibly if no longer usable, following environmental regulations.
7. Digital Mold Lifecycle Management Systems
Modern manufacturers leverage digital platforms (often integrated with PLM or MES systems) to:
Track mold usage and performance in real-time.
Schedule predictive maintenance using AI/ML analytics.
Integrate mold data with production and quality control systems.
Enable remote diagnostics and troubleshooting.
Benefits of Effective Mold Lifecycle Management
Increased Mold Longevity
Reduced Downtime and Production Disruptions
Consistent Part Quality
Lower Maintenance Costs
Better Asset Utilization and ROI
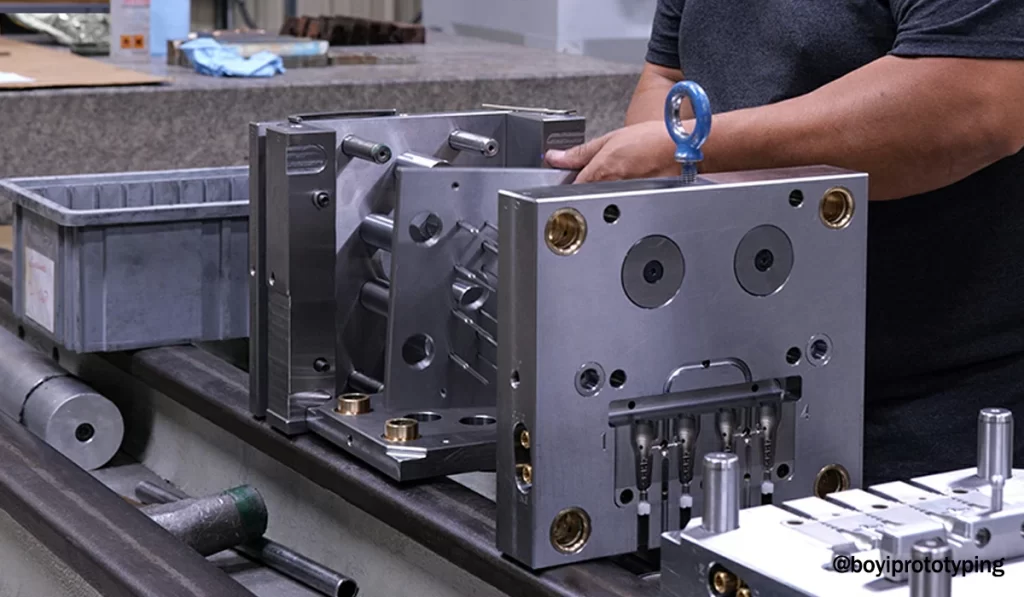