Maintaining and cleaning PVC molds is crucial for ensuring high-quality production, prolonging mold life, and preventing defects in finished products. Proper mold maintenance and cleaning practices are essential for optimizing efficiency and reducing downtime in production processes. Below are some best practices to follow for PVC mold maintenance and cleaning.
1. Regular Inspection
Purpose: Prevent mold wear and detect any potential issues before they become major problems.
Practice: Inspect molds regularly for signs of wear, damage, and buildup. Look for cracks, rust, or any signs of damage to the mold surfaces.
Frequency: Perform inspections at the beginning and end of each production cycle, and during routine maintenance.
2. Pre-Cleaning Procedures
Purpose: Remove any residual PVC material or contaminants before deep cleaning.
Practice:
Cool Down the Mold: Allow the mold to cool before cleaning to avoid burns or injury.
Scrape Off Excess PVC: Use a plastic scraper or a soft brush to remove any excess PVC material that may be stuck to the mold.
Blow Out Residual Material: Use compressed air to blow out any remaining plastic or debris from the cavities and vents.
3. Deep Cleaning and Degreasing
Purpose: Ensure the molds are free from grease, oil, and any other contaminants.
Practice:
Use Solvents: For stubborn residues, use a specialized PVC cleaning solvent or mild degreaser that is safe for the mold material.
Avoid Harsh Chemicals: Harsh chemicals or abrasive cleaners can damage the surface of the mold, leading to reduced mold life. Stick to mild, non-abrasive cleaners.
Brush Cleaning: Use a soft bristle brush to clean the cavities and other detailed mold areas. Be gentle to avoid scratching or damaging the mold surfaces.
4. Use of Mold Release Agents
Purpose: To ensure easy part ejection and prevent mold build-up.
Practice:
Apply a thin layer of mold release agents regularly to prevent plastic from sticking to the mold.
Avoid excessive use, as it may cause build-up that can degrade part quality.
5. Lubrication of Moving Parts
Purpose: To ensure smooth operation of the mold, reducing friction and wear.
Practice:
Lubricate any moving parts such as slides, pins, and ejector mechanisms regularly using appropriate lubricants.
Always use lubricants that are compatible with PVC and don’t leave residue that could contaminate the mold or finished parts.
6. Proper Storage of Molds
Purpose: To protect the molds from damage when they are not in use.
Practice:
Store molds in a dry, clean, and temperature-controlled environment to prevent rust, corrosion, or warping.
Use protective covers or coatings to shield the mold surfaces from dust, moisture, and environmental elements.
Ensure molds are stored in a manner that prevents any undue stress or pressure on the mold cavities.
7. Preventive Maintenance
Purpose: To ensure the mold is in optimal working condition, preventing unnecessary breakdowns.
Practice:
Implement a routine preventive maintenance schedule to replace worn-out components such as seals, pins, or ejector springs.
Check for alignment and wear on key mold components. Over time, misalignments can lead to issues with part ejection and mold closure, affecting part quality.
8. Use of Anti-Rust Coatings
Purpose: Prevent corrosion and extend the life of the mold.
Practice: Apply anti-rust coatings to molds that are exposed to moisture or humidity. This is particularly important if the mold is stored in a humid environment or not used frequently.
9. Documenting Maintenance and Cleaning Activities
Purpose: Track the mold’s condition and service history for efficient maintenance management.
Practice: Keep a detailed log of all cleaning and maintenance activities, including dates, issues found, and parts replaced. This helps track mold performance and plan for future maintenance cycles.
10. Training Personnel
Purpose: Ensure that mold cleaning and maintenance are carried out by skilled and knowledgeable personnel.
Practice: Train all operators and maintenance personnel on the best practices for mold cleaning and maintenance. Proper training can prevent mistakes that could damage the mold or degrade product quality.
11. Avoid Over-Cleaning
Purpose: Prevent unnecessary wear on the mold surfaces.
Practice: While cleaning is important, overzealous cleaning can cause wear on the mold surfaces. Avoid excessive abrasive cleaning methods, such as steel wool or aggressive solvents, unless absolutely necessary.
12. Temperature Management
Purpose: Control temperature during molding to avoid thermal expansion and stress on the mold.
Practice: Maintain a stable temperature for both the mold and the molding material. Thermal cycling can lead to mold degradation, so ensure molds are allowed to cool at the correct rate.
Conclusion
Effective PVC mold maintenance and cleaning are crucial for maintaining the quality and longevity of molds, improving production efficiency, and reducing downtime. By implementing the best practices outlined above, you can ensure that your molds remain in top condition and produce high-quality PVC parts consistently. Regular cleaning, proper lubrication, inspection, and preventive maintenance are all key to achieving long-term success in PVC molding operations.
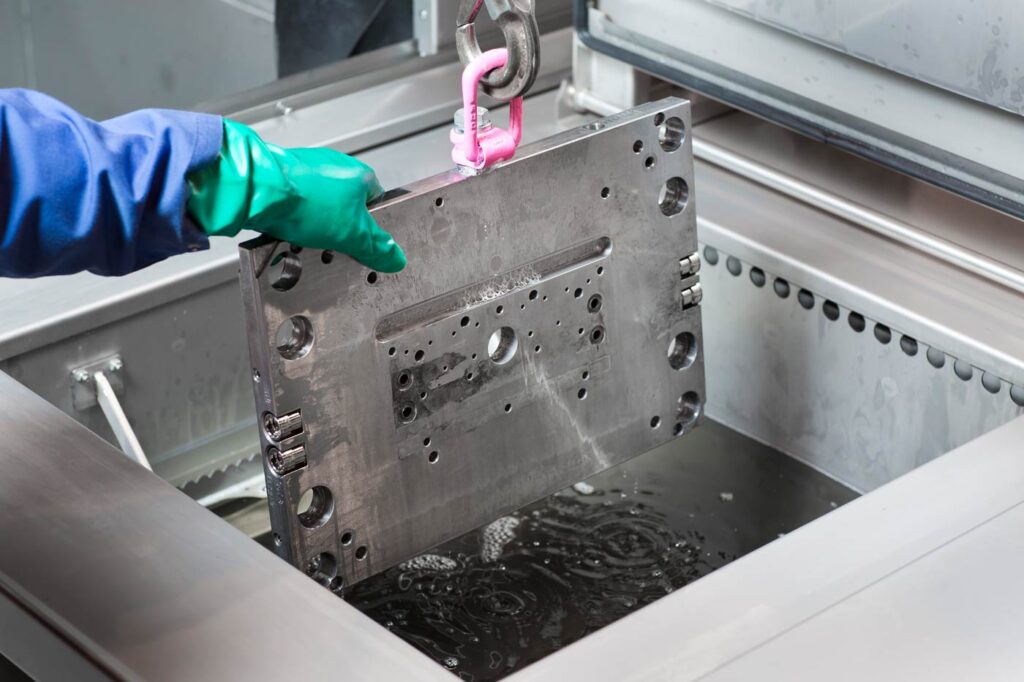
This article shares practical and effective tips for PVC mold maintenance and cleaning. I found the best practices easy to understand and very useful for extending mold life and ensuring product quality. A great resource for manufacturers and technicians alike!