Polyvinyl chloride (PVC) is widely recognized for its excellent chemical resistance, making it a popular material in various industrial molding applications. Its ability to withstand exposure to a wide range of chemicals while maintaining mechanical integrity and durability makes it a reliable choice for components used in harsh environments.
1. Understanding PVC’s Chemical Composition
PVC is a thermoplastic polymer made from vinyl chloride monomers. Its structure is primarily composed of carbon, hydrogen, and chlorine atoms, which contribute to its chemical inertness. The presence of chlorine enhances PVC’s resistance to oxidation and corrosive substances compared to other plastics.
2. Resistance to a Broad Spectrum of Chemicals
PVC demonstrates strong resistance to many common industrial chemicals, including:
Acids: Hydrochloric acid, sulfuric acid (diluted), and phosphoric acid.
Alkalis: Sodium hydroxide and potassium hydroxide.
Salts: Most inorganic salts and their solutions.
Alcohols: Ethanol and methanol.
Oils and Greases: Limited resistance depending on temperature and exposure time.
However, PVC is less resistant to:
Ketones: Such as acetone.
Esters and Aromatic hydrocarbons: Like benzene and toluene.
Chlorinated solvents: Such as trichloroethylene.
3. Grades of PVC for Enhanced Resistance
There are several grades of PVC used in industrial molding, including:
Rigid PVC (uPVC): Common in pipe fittings, valves, and housings due to high mechanical strength and chemical resistance.
CPVC (Chlorinated PVC): Offers improved temperature resistance and broader chemical resistance, making it ideal for hot corrosive liquids.
Flexible PVC: Modified with plasticizers, used in environments where flexibility and some degree of chemical resistance are needed.
4. Applications in Industry
Due to its chemical resistance, molded PVC components are widely used in:
Chemical processing plants: For tanks, pipes, and fittings.
Water treatment facilities: For valves, nozzles, and diffusers.
Agricultural equipment: For fertilizer handling systems.
Pharmaceutical and food industries: For transporting non-reactive chemicals (food-grade PVC is used here).
5. Design Considerations for PVC Molding
When designing PVC-molded parts for chemical exposure:
Material compatibility: Match the PVC grade with the chemicals and temperatures involved.
Wall thickness: Ensure adequate thickness to withstand long-term chemical attack.
Sealing and joints: Use compatible adhesives or gaskets to prevent leaks and degradation.
6. Advantages Over Other Plastics
Compared to materials like polyethylene (PE), polypropylene (PP), or ABS, PVC offers:
Better flame retardancy
Higher tensile strength
Greater resistance to UV degradation (with additives)
Cost-effectiveness in long-term chemical service
Conclusion
Chemical resistance is a critical property that makes PVC a go-to material for industrial molding applications. By selecting the appropriate PVC formulation and carefully considering the chemical environment, manufacturers can create durable, safe, and cost-effective components for a wide range of industrial uses.
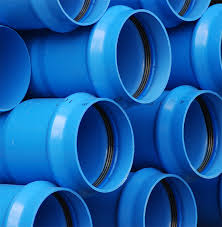