Molding is a critical process in the production of automotive components. The molds used for manufacturing parts like bumpers, dashboards, and interior panels must be precisely designed and maintained to ensure high-quality, defect-free parts. However, various issues can arise during molding, leading to defects in the final products. Understanding these defects and how to prevent them is essential for ensuring smooth production. Here are some common defects in automotive molds and their prevention:
1. Warping
Definition: Warping is a distortion or bending of the molded part due to uneven cooling or internal stresses within the material. It can occur when the cooling rate is inconsistent across the part or when the material shrinks unevenly as it cools.
Prevention:
Even Cooling: Ensure that the mold’s cooling system is evenly designed, with proper coolant flow around the part.
Proper Material Selection: Choose materials with low shrinkage rates that are less prone to warping.
Optimize Mold Design: The design of the mold should ensure uniform material flow and cooling, particularly in thicker sections of the part.
Control Process Parameters: Maintain consistent temperature and pressure settings during molding.
2. Short Shots
Definition: A short shot occurs when the mold cavity does not fill completely, leaving an incomplete part. This can be caused by insufficient material flow or poor injection pressure.
Prevention:
Correct Injection Pressure: Ensure that the injection pressure is high enough to fill the mold completely but not too high to cause defects like flash.
Proper Gate Design: Design gates to ensure that material flows evenly into all parts of the mold.
Mold Venting: Ensure the mold is well-vented to allow the air to escape as the material fills the cavity, preventing blockages that could cause short shots.
Material Temperature: Ensure the material is injected at the correct temperature to ensure fluidity.
3. Sink Marks
Definition: Sink marks are depressions or indentations that appear on the surface of the molded part, typically in areas where the material is thicker.
Prevention:
Uniform Wall Thickness: Design parts with uniform wall thickness to prevent localized shrinkage that causes sink marks.
Optimize Cooling Rate: Implement a balanced cooling system to reduce excessive material contraction during cooling.
Increase Injection Speed: Inject the material at a faster rate to reduce the likelihood of sink marks.
Use of Inserts: In cases where part thickness cannot be uniform, consider using metal inserts to provide structural support.
4. Flash
Definition: Flash occurs when excess material escapes from the mold cavity, resulting in thin edges around the part. This happens when the mold halves do not close completely or when excessive pressure is applied during injection.
Prevention:
Accurate Mold Closing: Ensure the mold closes properly, without any gaps, before the injection process begins.
Proper Clamping Force: Apply the correct amount of clamping force to hold the mold halves tightly together.
Mold Maintenance: Regularly check and maintain the mold to prevent misalignment or wear that may cause flash.
Process Control: Adjust injection speed and pressure to prevent excessive material flow.
5. Surface Defects (Scratches, Scuffs, or Imperfections)
Definition: Surface defects like scratches, scuffs, and other imperfections can occur due to contamination, poor mold surface finish, or improper handling of parts.
Prevention:
Mold Surface Quality: Maintain the mold surface with high precision and smoothness to prevent scratches or scuffs.
Cleanliness: Ensure that the mold is kept free of contaminants, such as dust or debris, which can cause defects on the surface of the part.
Proper Handling: Train operators to handle parts carefully to prevent damage during removal from the mold.
6. Bubbles or Voids
Definition: Bubbles or voids in the molded part can occur when air or gas is trapped during the molding process. This leads to internal cavities or air pockets, which can weaken the part.
Prevention:
Mold Venting: Ensure adequate venting to allow any trapped air or gases to escape during the injection process.
Injection Speed and Pressure: Adjust the injection speed and pressure to ensure that the material fills the mold cavity without trapping air.
Degassing of Materials: Degas or preheat certain materials to reduce the chances of bubbles forming during the injection process.
7. Dimensional Inaccuracy
Definition: Dimensional inaccuracies occur when the part does not meet the required tolerances, resulting in parts that are either too large, too small, or out of specification.
Prevention:
Precision Mold Design: Design the mold to the exact specifications, ensuring proper alignment and dimensioning to produce accurate parts.
Constant Monitoring: Regularly monitor process parameters such as injection pressure, temperature, and cooling rates to avoid variations in the part’s dimensions.
Material Consistency: Use consistent and high-quality raw materials to reduce variation in part dimensions.
Tooling Calibration: Ensure that all tooling used in the molding process is calibrated and maintained regularly to meet strict dimensional standards.
8. Mold Wear and Tear
Definition: Over time, the mold may experience wear and tear due to repeated use, leading to changes in the shape, texture, and performance of the molded parts. This can lead to defects like dimensional inaccuracies, surface imperfections, or poor part quality.
Prevention:
Regular Maintenance: Perform regular maintenance checks and repairs on molds to identify signs of wear and tear early.
Use High-Quality Mold Materials: Select mold materials that are resistant to wear and abrasion.
Mold Coatings: Apply special coatings to mold surfaces to increase their resistance to wear and corrosion.
9. Cold Slugs
Definition: Cold slugs are solidified chunks of material that form in the mold cavity due to the material cooling and hardening before it reaches the entire mold. This can block the flow of the material and lead to incomplete filling.
Prevention:
Maintain Proper Material Temperature: Ensure that the material is injected at the correct temperature to maintain fluidity throughout the injection process.
Optimize Gate and Runner Design: Design the gate and runner systems to ensure smooth flow of material into all areas of the mold.
Preheat the Mold: Preheat the mold to the correct temperature before injection to reduce the chances of cold slugs forming.
Conclusion:
Preventing defects in automotive molds requires attention to detail in mold design, material selection, process parameters, and regular maintenance. Understanding the causes of common defects and implementing preventive measures can significantly improve the quality of the final parts, reduce waste, and increase production efficiency. By consistently monitoring and optimizing the molding process, manufacturers can ensure high-quality automotive components that meet the stringent requirements of the industry.
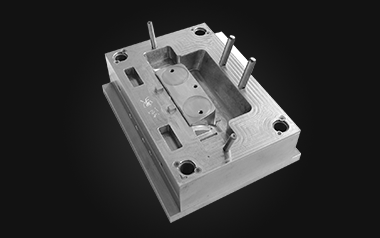