Injection molding is a widely used manufacturing process that involves injecting molten plastic into a mold cavity to produce parts. While it is a highly efficient and versatile process, defects can arise during production, affecting the quality and performance of the final product. Identifying these defects and understanding how to prevent them is essential for improving the overall production process.
Here are some common defects found in injection molding and the ways to prevent them:
1. Short Shots
A short shot occurs when the injected plastic does not fill the entire mold cavity, leading to incomplete parts.
Causes:
Insufficient injection pressure
Low mold temperature
Blocked or undersized runner system
Low melt temperature
Prevention:
Increase injection pressure to ensure the mold cavity fills completely.
Adjust mold temperature to the correct range to maintain material flow.
Check and clean the runner system regularly to prevent blockages.
Ensure that the material is at the correct temperature before injection.
2. Warpage
Warpage refers to the deformation of a part after cooling, often resulting in uneven shapes or twisted surfaces.
Causes:
Uneven cooling rates during the solidification of the plastic
Inconsistent wall thickness
Mold design issues
Internal stresses within the material
Prevention:
Use uniform wall thickness to promote even cooling and reduce internal stress.
Improve mold cooling systems to ensure consistent temperature distribution.
Use appropriate materials that are less prone to warping.
Employ venting techniques to reduce trapped air that can cause uneven pressure during cooling.
3. Sink Marks
Sink marks are depressions that form on the surface of the part, typically in thicker areas, after the material cools.
Causes:
High injection pressure combined with slow cooling time
Thick wall sections that cool slower than thinner sections
Insufficient packing or holding pressure during cooling
Prevention:
Ensure proper packing and holding pressure during the cooling phase.
Reduce wall thickness to allow for more uniform cooling.
Adjust cooling time and mold temperature to optimize material flow and cooling rates.
4. Flash
Flash is excess material that escapes from the mold cavity, forming unwanted thin projections along the parting line.
Causes:
Excessive injection pressure
Worn or damaged mold parts (e.g., defective mold seals or incorrect mold alignment)
High melt temperature leading to material leakage
Prevention:
Adjust injection pressure to an appropriate level to prevent excessive material flow.
Regularly inspect and maintain mold components to ensure proper sealing and alignment.
Optimize material temperature to reduce excessive flow.
5. Air Traps
Air traps occur when air is trapped inside the mold cavity, leading to defects like bubbles or voids in the final product.
Causes:
Insufficient venting in the mold
Too rapid injection speed
Mold cavity design issues preventing air escape
Prevention:
Improve venting by adding vent holes to allow air to escape during injection.
Control injection speed to prevent air from becoming trapped.
Optimize mold design to ensure air can flow out during the injection process.
6. Mold Sticking
Mold sticking happens when the part adheres to the mold, causing difficulty in ejecting it or damaging the part during removal.
Causes:
Inadequate mold release agent
Improper mold surface finish
Low mold temperature or excessive cooling time
Prevention:
Apply mold release agents to facilitate easy part ejection.
Use appropriate mold coatings or finishes to reduce friction between the mold and the part.
Adjust mold temperature to ensure the part cools at the optimal rate, preventing sticking.
7. Brittleness or Cracking
Parts that are brittle or prone to cracking can have compromised durability and performance.
Causes:
Incorrect material selection
Overheating or overheating of the plastic during injection
Poor cooling, leading to internal stresses
Prevention:
Select materials with proper impact resistance for the application.
Maintain the correct injection molding temperature range to prevent degradation of material properties.
Ensure uniform cooling to minimize internal stresses and prevent cracking.
8. Color Mismatch
Color mismatch or inconsistent coloring of the parts can result from improper mixing or contamination of the resin.
Causes:
Inconsistent blending of colorant or additives with resin
Contamination by residues from previous batches
Incorrect machine settings or temperature
Prevention:
Ensure thorough mixing of colorants and additives with the base resin.
Clean the injection molding machine thoroughly between different production runs to prevent contamination.
Monitor machine temperature and processing parameters to ensure consistent color results.
9. Burn Marks
Burn marks are dark spots or discolorations on the surface of the part, typically caused by trapped air or excessive heat.
Causes:
High injection speeds that cause material to overheat
Insufficient venting, trapping air inside the mold
Mold design issues that prevent proper venting
Prevention:
Reduce injection speed to avoid overheating the material.
Improve venting in the mold to allow trapped air to escape.
Modify the mold design to ensure even material flow and reduce the chances of air being trapped.
10. Jetting
Jetting is a defect where the plastic material flows too quickly and solidifies too late, creating a “jet” pattern that results in visible flow marks.
Causes:
High injection speed causing the material to flow unevenly
Low melt temperature or incorrect viscosity of the material
Prevention:
Optimize injection speed and pressure to ensure a smooth and controlled material flow.
Ensure that the melt temperature is consistent and within the material’s recommended processing range.
Conclusion
While injection molding is a reliable and efficient manufacturing process, defects can occur at various stages of production. Understanding the causes of these defects and taking proactive steps to prevent them can significantly improve part quality, reduce waste, and enhance overall efficiency. By carefully monitoring the process parameters, regularly maintaining molds, and selecting the right materials, manufacturers can avoid common defects and produce high-quality products.
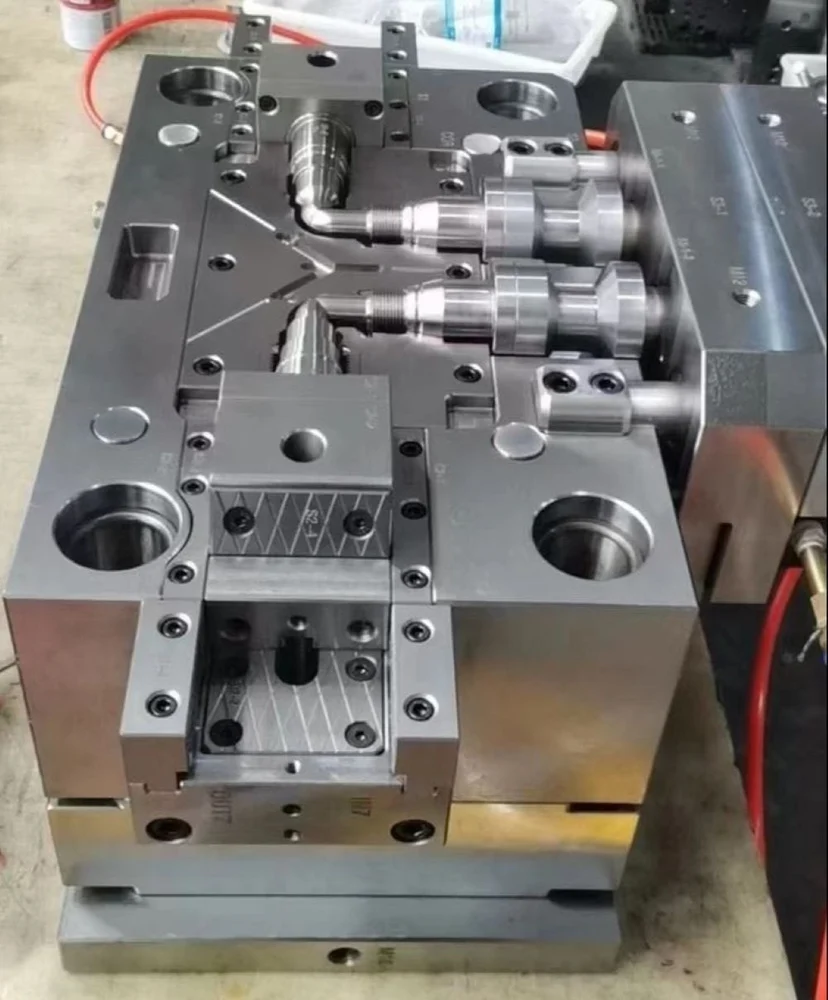