Injection molding is a popular manufacturing process used to create parts and products in large volumes, especially for plastic components. Whether you’re embarking on a new product development project or scaling up production, accurate cost estimation and budgeting are crucial for ensuring profitability, efficiency, and meeting customer demands. This process involves analyzing various factors, including material selection, tooling, machine time, labor, and overhead costs. Below, we break down the key elements involved in cost estimation and budgeting for injection molding projects.
1. Material Costs
The type of material used in injection molding can significantly impact the total cost of a project. The choice between different types of plastics, such as thermoplastics (e.g., polyethylene, polypropylene) or thermosets, can lead to variations in cost. Factors affecting material costs include:
Material Type: High-performance polymers like PEEK or polycarbonate tend to cost more than commodity plastics.
Material Quantity: The amount of material required for each part, including any scrap or waste produced during the molding process.
Material Supplier: Prices can vary depending on supplier agreements, market conditions, and bulk purchasing options.
2. Tooling Costs
Tooling involves the creation of molds, which is one of the highest initial costs in an injection molding project. The mold is usually made of steel or aluminum, with steel being the more expensive option. Tooling costs depend on:
Mold Design: Complex designs require more time, effort, and precision, leading to higher tooling costs.
Material for Mold: The choice of mold material (steel, aluminum, etc.) directly impacts the cost.
Mold Lifespan: Molds with a longer expected lifespan might have a higher initial cost, but over time, they may be more cost-effective if producing a large volume of parts.
Mold Modifications: Any adjustments or modifications during the project can lead to unexpected costs.
3. Machine Costs (Cycle Time)
Injection molding machines are specialized and can be expensive, with costs varying depending on the machine’s size, capabilities, and the complexity of the parts to be produced. Machine costs are generally broken down into:
Machine Hours: The amount of time required for the injection molding process, also known as cycle time, can impact costs. A shorter cycle time is more efficient and cost-effective.
Machine Utilization: The number of parts produced during a machine’s operation also affects the cost. If the machine is running at full capacity, the cost per part will decrease.
4. Labor Costs
Labor costs in injection molding include the workers required for machine operation, quality control, and maintenance. Labor costs are influenced by:
Skill Level: Highly skilled operators may demand higher wages, but their expertise could lead to fewer defects and higher-quality products.
Production Volume: Larger production runs typically lower the per-unit labor cost, while small runs or prototype production require more labor hours per part.
Maintenance and Setup: Setting up the mold and making adjustments during the process add labor hours to the total cost.
5. Overhead Costs
Overhead costs cover the general expenses related to running a manufacturing facility, which may include:
Energy Costs: Injection molding machines consume considerable energy, and energy prices can fluctuate.
Maintenance and Repair: Regular machine maintenance, troubleshooting, and repairs add to the ongoing costs.
Facility Costs: Rent, insurance, and other overhead expenses associated with the physical plant can affect the overall budget.
6. Quality Control Costs
Quality control is a critical aspect of any injection molding project. These costs include:
Inspection and Testing: Some parts require extensive testing for dimensional accuracy, structural integrity, or compliance with regulatory standards.
Scrap and Rework: Some defective parts may be scrapped, and others may need rework. This can add to production costs, particularly for high-precision items.
7. Logistics and Shipping Costs
For injection molding projects, transporting raw materials, completed parts, and finished products to customers or warehouses can add additional costs, which include:
Material Transportation: Costs for getting raw materials to the facility can vary depending on the location and the amount of material required.
Shipping of Finished Goods: Shipping costs, including freight charges and packaging, contribute to the final cost.
Inventory Management: If parts are produced in large quantities and stored before shipping, inventory management costs may arise.
8. Design and Engineering Costs
Before injection molding begins, design and engineering costs can factor into the overall budget. This includes:
Product Design: The complexity of the product’s design will influence both the molding process and tooling requirements. More intricate designs may require advanced design software, prototyping, and collaboration between engineers and designers.
Prototype Development: In many cases, an initial prototype will be produced before full-scale production begins, and this incurs additional costs for testing and iteration.
9. Additional Factors
There are various other factors that can impact cost estimation and budgeting for injection molding, such as:
Project Timeline: Tight timelines may lead to expedited costs or overtime for employees.
Scale of Production: Larger production runs can lead to lower per-unit costs, but small runs are often more expensive.
Location: Regional factors, such as the proximity to material suppliers or labor rates, can also impact costs.
Regulatory Compliance: Compliance with industry standards and regulations (such as FDA approval for medical devices) can increase costs related to testing and certification.
Conclusion: Balancing Cost and Quality
Accurate cost estimation and budgeting for injection molding projects require a comprehensive understanding of the various factors that contribute to the total cost of production. Balancing these elements—material, tooling, machine time, labor, and overhead—requires careful planning, efficient production practices, and the ability to forecast potential challenges. By anticipating costs and identifying areas for cost-saving without compromising quality, manufacturers can ensure that their injection molding projects remain profitable and competitive in the market.
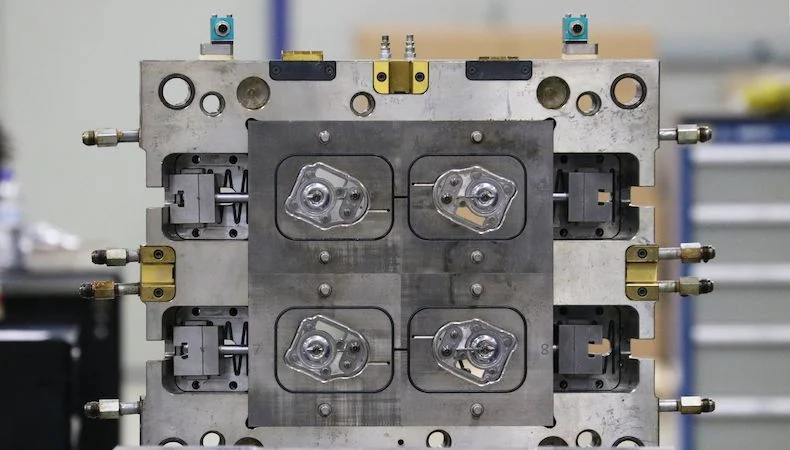