Polyvinyl Chloride (PVC) is one of the most versatile thermoplastics used across numerous industries, from automotive to healthcare. While standard PVC formulations serve many applications, certain environments and product requirements demand enhanced performance characteristics that only custom blends can offer. Custom PVC blends are tailored formulations designed to meet specific processing, functional, and regulatory needs in molding operations.
Why Customize PVC Blends?
PVC’s base properties—such as chemical resistance, durability, and ease of processing—can be significantly modified by incorporating various additives. Customization allows manufacturers to:
Enhance Mechanical Strength
Add fillers and plasticizers to improve flexibility, impact resistance, and tensile strength.Improve Thermal and Flame Resistance
Include heat stabilizers and flame retardants to meet industry-specific safety standards.Achieve Regulatory Compliance
Use FDA, RoHS, or REACH-compliant additives for applications in medical, food contact, or electronics.Optimize for Specific Molding Techniques
Adapt formulations for injection molding, blow molding, extrusion, or rotational molding to improve cycle times, reduce waste, and ensure dimensional stability.
Key Components of a Custom PVC Blend
Plasticizers
Influence flexibility and softness.
Common choices: phthalates (less common now due to regulations), adipates, citrates, and bio-based alternatives.
Stabilizers
Enhance thermal stability during processing.
Options: calcium-zinc, tin-based, or organic stabilizers depending on application.
Fillers and Reinforcements
Improve stiffness, dimensional stability, and cost-effectiveness.
Includes calcium carbonate, fiberglass, or talc.
Impact Modifiers
Boost shock resistance for rigid applications.
Colorants and Processing Aids
Ensure product aesthetics and smooth mold flow.
Industries and Applications
Medical Devices
Custom blends free of DEHP and other harmful plasticizers for tubing, masks, and containers.Automotive
Formulations with high UV and temperature resistance for dashboards, seals, and gaskets.Construction
Durable, flame-retardant PVC for pipe fittings, window profiles, and cable insulation.Consumer Goods
Soft-touch, vibrant-colored blends for toys, footwear, and packaging.
Advantages of Custom PVC Blends in Molding
Precision Fit to Application Needs
Every element of the blend can be fine-tuned to maximize performance.Cost Efficiency Over Time
Reducing scrap rate, improving cycle times, and enhancing product lifespan lead to better ROI.Regulatory Peace of Mind
Ensures adherence to both domestic and international compliance standards.
Conclusion
Custom PVC blends provide unmatched flexibility and functionality for specialized molding applications. By working with experienced material scientists and compounders, manufacturers can unlock new levels of product performance, durability, and compliance. As market demands evolve, so too will the sophistication of custom PVC formulations, making them indispensable in precision-driven manufacturing sectors.
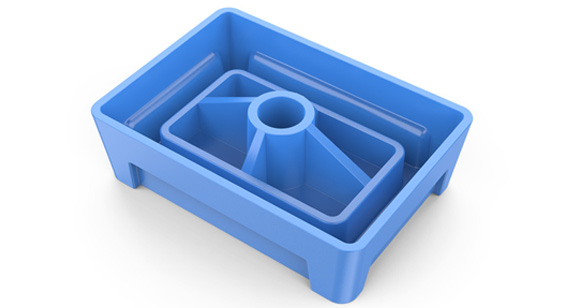