In injection molding, draft angles are a critical design feature that ensures the efficient release of a molded part from the mold without damaging the part or the mold itself. A draft is a slight taper applied to the vertical faces of the part. Without proper draft, parts can stick in the mold, leading to defects, increased cycle times, or even damage.
Why Draft Angles Matter
Ejection Ease: As the molten plastic cools, it tends to shrink and grip the mold. Draft angles help in reducing friction during ejection.
Surface Finish: Helps maintain the surface finish by preventing scratches during ejection.
Mold Longevity: Reduces wear and tear on ejector systems and mold surfaces.
Reduced Defects: Minimizes the chances of drag marks, warping, or part deformation.
Standard Draft Angle Guidelines
Minimum Draft: Typically 1° to 2° is recommended for most applications.
Texture Considerations: For textured surfaces, add 1° of draft for every 0.001 inch of texture depth.
Deep Features: The deeper the cavity, the more draft you may need — sometimes 3° to 5° or more.
Side Walls: Vertical side walls are especially prone to sticking; they benefit most from added draft.
Best Practices in Draft Design
Apply Draft Early in Design:
Incorporate draft angles from the start to avoid rework.
Consult with mold manufacturers during the design phase.
Uniform Draft:
Ensure consistent draft across similar features to simplify mold design and ensure uniform ejection.
Consider Part Orientation:
Determine the parting line and direction of mold opening to identify which surfaces need draft.
Avoid Undercuts:
Proper draft helps avoid complex undercuts that can increase mold cost and complexity.
Use CAD Tools:
Use features like draft analysis in CAD software to validate your design.
Common Pitfalls
Insufficient Draft: Leads to high ejection force and potential damage.
Neglecting Texture: Not accounting for surface finish when designing draft.
Late Changes: Adding draft late can impact aesthetics and function.
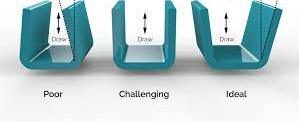