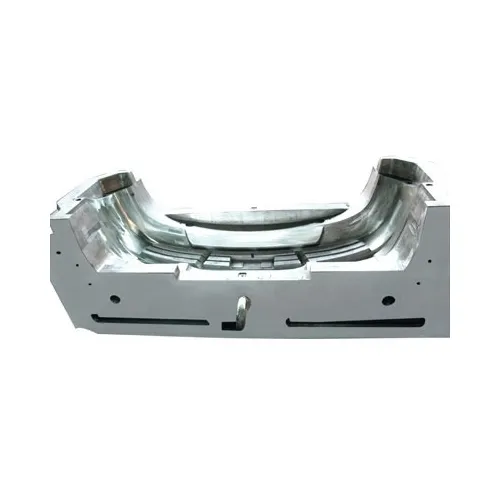
Introduction
Exterior automotive molds are essential components in the manufacturing of various parts for vehicles. These molds are used to create a wide range of exterior elements that contribute to both the aesthetics and functionality of a vehicle. Among the most notable parts produced using these molds are bumpers, grilles, and other exterior features that are critical for vehicle protection, styling, and aerodynamics. This article will explore the importance, types, and manufacturing processes of exterior automotive molds, focusing on bumpers, grilles, and other related components.
1. Bumpers: Protection, Style, and Functionality
Role of Bumpers
Bumpers are one of the most crucial exterior parts of any vehicle. Their primary function is to absorb impact in the event of a collision, thereby protecting the vehicle’s structure and passengers. Modern bumpers are often designed to not only provide safety but also enhance the overall look of the vehicle.
Materials Used for Bumper Molds
Bumpers are usually made from materials like plastic (commonly polypropylene), rubber, or lightweight metals like aluminum. The choice of material affects the bumper’s strength, weight, and cost. Injection molding is the most common manufacturing process for bumpers because it provides high precision and durability while being cost-effective.
Molding Process
The molding process for bumpers involves creating a mold of the bumper shape, followed by injecting molten material (such as plastic) into the mold under high pressure. The material is allowed to cool and harden, forming the bumper’s final shape. This process is highly automated and ensures that bumpers meet safety standards, while also allowing for intricate designs and styling.
2. Grilles: Design and Ventilation
Role of Grilles
The grille is an essential part of the front end of a vehicle, typically located between the headlights and the front bumper. Its primary function is to allow air to flow into the engine compartment, aiding in engine cooling and ventilation. Grilles also contribute significantly to the aesthetic appeal of a vehicle’s exterior, providing a distinctive look that complements the vehicle’s design.
Materials Used for Grille Molds
Grilles are usually made from metals such as aluminum or steel, although plastic and composite materials are also used for some designs. These materials are selected for their durability, corrosion resistance, and ability to withstand harsh environmental conditions.
Molding Process
The manufacturing of grilles generally uses either injection molding for plastic grilles or stamping for metal ones. Injection molding is preferred for plastic grilles because it allows for complex shapes and fine detailing. Metal grilles, on the other hand, are often created using stamping techniques that involve pressing metal sheets into molds under high pressure.
3. Other Exterior Automotive Molds: Mirrors, Fenders, and Side Panels
Apart from bumpers and grilles, several other exterior parts are manufactured using molds. These components include side panels, fenders, mirrors, and trims. Each of these parts serves a specific function and often requires different materials and manufacturing processes.
Side Panels and Fenders: Side panels and fenders are typically molded using either plastic or sheet metal. They provide the structural framework of the vehicle and contribute to its aesthetic design. Plastic panels are lightweight and can be molded into complex shapes, whereas metal panels are used for their strength and durability.
Mirrors: Automotive mirrors are typically made using injection molding for plastic components and glass molding for reflective surfaces. Mirrors play a crucial role in the safety and functionality of vehicles, providing drivers with the necessary visibility.
Trim and Molding: Trim pieces, such as door handles, moldings, and spoilers, are also molded to fit seamlessly into the vehicle’s design. These parts are often made from high-quality plastic or metal alloys, ensuring they are both functional and visually appealing.
4. Benefits of Using Molds in Automotive Manufacturing
Precision: Molding allows for high levels of precision, ensuring that parts fit perfectly within the vehicle’s design specifications.
Cost-Effectiveness: Once molds are created, the production of parts becomes highly cost-effective, especially in mass production scenarios.
Design Flexibility: Molding allows for the creation of complex and intricate designs that may be difficult or impossible to achieve with other manufacturing processes.
Durability and Strength: Molding processes ensure that parts are made to withstand harsh conditions, including extreme temperatures, impacts, and vibrations.
5. Sustainability and Innovation in Molding
As automotive manufacturers continue to emphasize sustainability, the development of environmentally friendly materials for molds is gaining importance. For instance, recycled plastics and bio-based materials are increasingly being used to produce various automotive parts. Additionally, advancements in 3D printing technology are enabling manufacturers to create prototypes and molds faster and with less waste, contributing to more sustainable practices.
Conclusion
Exterior automotive molds play an essential role in the production of bumpers, grilles, mirrors, and other exterior components. These molds are crucial for the safety, performance, and aesthetics of vehicles, and advancements in molding technology continue to enhance the precision, durability, and sustainability of automotive manufacturing. From the protective function of bumpers to the airflow function of grilles, these molds are vital in shaping the cars of tomorrow. As the industry evolves, innovation in mold design and materials will continue to drive the future of automotive manufacturing.