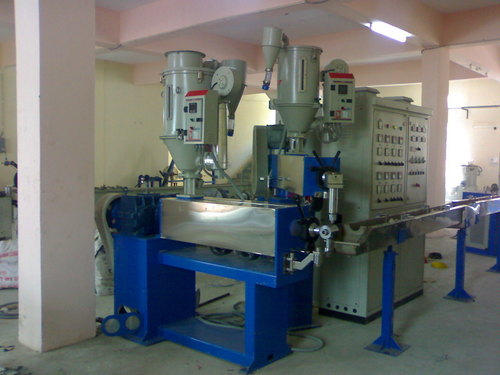
Flexible polyvinyl chloride (PVC) is a widely used material for cable insulation molding due to its exceptional balance of flexibility, durability, and cost-effectiveness. It is employed extensively in electrical, telecommunications, and automotive industries to provide robust insulation for wires and cables, ensuring safety and reliable performance in various operating environments.
Properties of Flexible PVC
Flexible PVC combines the inherent benefits of PVC with plasticizers, which impart elasticity and softness to the material. This results in a versatile material with the following key properties:
- Electrical Insulation: Excellent dielectric properties make flexible PVC an effective insulator for electrical cables.
- Flame Retardancy: Additives can enhance its resistance to ignition, making it safer for applications in high-risk environments.
- Chemical Resistance: It resists oils, chemicals, and moisture, ensuring longevity even in harsh conditions.
- Flexibility and Durability: Flexible PVC withstands bending and twisting, making it suitable for dynamic applications.
- Customizability: It can be colored, UV-stabilized, or modified to meet specific application requirements.
Molding Techniques for Cable Insulation
Flexible PVC is typically processed using extrusion molding for cable insulation. The extrusion process involves heating and pressurizing PVC resin and forcing it through a die to coat the cable core. Key techniques include:
Extrusion Parameters Optimization
Precise control of temperature, pressure, and extrusion speed is critical to achieving uniform insulation thickness and a smooth finish.Twin-Screw Extruders
Twin-screw extruders are often used to mix PVC resin with plasticizers, stabilizers, and other additives, ensuring homogeneity before the material is applied to cables.Cooling and Solidification
After extrusion, the coated cables are rapidly cooled using water baths or air jets to solidify the insulation and prevent deformation.Inline Quality Control
Real-time monitoring systems, such as laser gauges and spark testers, ensure the insulation meets specified dimensions and maintains electrical integrity.
Applications in Cable Manufacturing
Flexible PVC insulation is used across a wide range of cable types:
- Electrical Wiring: For residential, commercial, and industrial power distribution.
- Automotive Cables: Withstand vibrations, temperature fluctuations, and exposure to oils.
- Telecommunication Cables: Protect data and signal transmission from environmental factors.
- Instrumentation Wiring: Maintain accuracy and safety in sensitive equipment.
Advantages of Flexible PVC for Cable Insulation
- Cost-Effective: PVC is affordable compared to alternatives like rubber or thermoset materials.
- Versatile: Easily adapted for different voltage classes and environmental conditions.
- Recyclable: PVC insulation can be recycled, aligning with sustainability goals in manufacturing.