Introduction Polyvinyl chloride (PVC) is one of the most widely used thermoplastic materials in the world, valued for its versatility, durability, and cost-effectiveness. It is commonly used in industries ranging from construction and medical devices to consumer products and automotive parts. However, when exposed to high temperatures during the processing or molding stage, PVC can degrade, leading to the release of harmful compounds and a deterioration of material properties. To prevent this, heat stabilizers are essential in PVC molding processes. These stabilizers not only preserve the material’s integrity but also enhance the overall performance and safety of the final product.
What Are Heat Stabilizers? Heat stabilizers are chemical additives incorporated into PVC formulations to prevent the material from degrading due to heat. They work by either absorbing or neutralizing the heat generated during the molding process. The most common forms of stabilizers include lead-based stabilizers, calcium-zinc stabilizers, and organotin stabilizers, although the use of lead stabilizers has decreased due to environmental concerns.
Heat stabilizers prevent a range of undesirable effects caused by heat exposure, such as:
Discoloration: PVC can turn yellow or brown when exposed to heat without stabilizers.
Loss of mechanical properties: Heat can cause PVC to become brittle or lose its strength.
Degradation of molecular structure: High temperatures can break down the polymer chains in PVC, leading to poor performance and reduced lifespan.
Release of harmful gases: Without stabilizers, PVC can release toxic gases like hydrochloric acid when heated, posing health and environmental risks.
Types of Heat Stabilizers
Lead-based stabilizers: Historically, lead compounds were the most widely used stabilizers due to their cost-effectiveness and excellent performance. However, due to their toxicity, especially in terms of lead contamination, their use has significantly declined in recent years.
Calcium-zinc stabilizers: These are now a popular alternative to lead-based stabilizers. They are non-toxic and environmentally friendly, making them suitable for many applications, including those in direct contact with food or medical products. Calcium-zinc stabilizers offer excellent heat stability, low volatility, and minimal migration.
Organotin stabilizers: Organotin-based stabilizers are another non-toxic option used in PVC formulations. They are particularly effective at stabilizing PVC during the molding process and are commonly used in flexible PVC applications like cables and pipes.
Barium-based stabilizers: These are often used in applications where a high level of heat stability is required. They are also a viable alternative to lead stabilizers.
Why Are Heat Stabilizers Essential in PVC Molding?
Enhanced Processing Efficiency: During PVC molding, the material needs to be heated to a specific temperature to become pliable. Heat stabilizers allow the material to remain stable at these high temperatures, preventing premature degradation that can affect the molding process.
Improved Product Durability: Stabilizers help maintain the mechanical properties of PVC after molding, ensuring that the final product has the desired level of flexibility, strength, and resistance to wear. This increases the lifespan of the molded PVC products, making them more durable and cost-effective in the long term.
Prevention of Toxicity: Heat stabilizers help to prevent the release of toxic gases like hydrogen chloride, which is a byproduct of PVC degradation. This is particularly important for safety and compliance with environmental regulations, ensuring that PVC products meet safety standards for use in various industries.
Color Retention: Without heat stabilizers, PVC can undergo color changes, particularly discoloration like yellowing, when exposed to high temperatures. Stabilizers preserve the aesthetic appeal of the material, which is critical for consumer-facing products such as flooring, window profiles, and consumer electronics.
Environmental and Health Safety: The transition from toxic lead-based stabilizers to more eco-friendly alternatives, such as calcium-zinc and organotin stabilizers, has helped reduce the environmental impact of PVC products. These alternatives ensure that PVC remains a viable option in industries that demand both performance and safety, such as medical and food packaging.
Cost-effectiveness: Though the initial cost of heat stabilizers may add to the price of the raw material, they ultimately help reduce defects in finished products, improve production efficiency, and extend the lifespan of the final products. This makes them a cost-effective investment in the manufacturing process.
Applications of Heat Stabilizers in PVC Molding Heat stabilizers are used in various PVC products, particularly where molding or extrusion processes involve high temperatures. Common applications include:
Pipes and fittings: PVC pipes used in construction and plumbing require heat stabilizers to prevent degradation during manufacturing and ensure long-term performance under high temperatures.
Wires and cables: PVC used in cable insulation must withstand high temperatures during extrusion without losing its insulating properties.
Window profiles: The production of PVC window frames benefits from heat stabilizers to prevent deformation and discoloration during processing.
Medical devices: PVC is widely used in the medical industry for items like IV bags and tubing, where the stability of the material is crucial for patient safety.
Flooring and wall coverings: Heat stabilizers help maintain the quality and appearance of vinyl flooring, ensuring that it resists heat and wear over time.
Conclusion Heat stabilizers play a critical role in the production of PVC molded products, ensuring that the material maintains its integrity during processing and in its final application. By preventing degradation, preserving color, improving durability, and meeting environmental and health standards, heat stabilizers are indispensable for manufacturers looking to produce high-quality, long-lasting PVC products. The use of safe, non-toxic stabilizers, such as calcium-zinc and organotin, reflects the ongoing shift towards more sustainable and eco-friendly practices in the PVC industry. Ultimately, heat stabilizers are essential not only for the performance and safety of PVC products but also for the overall efficiency and sustainability of the PVC molding process.
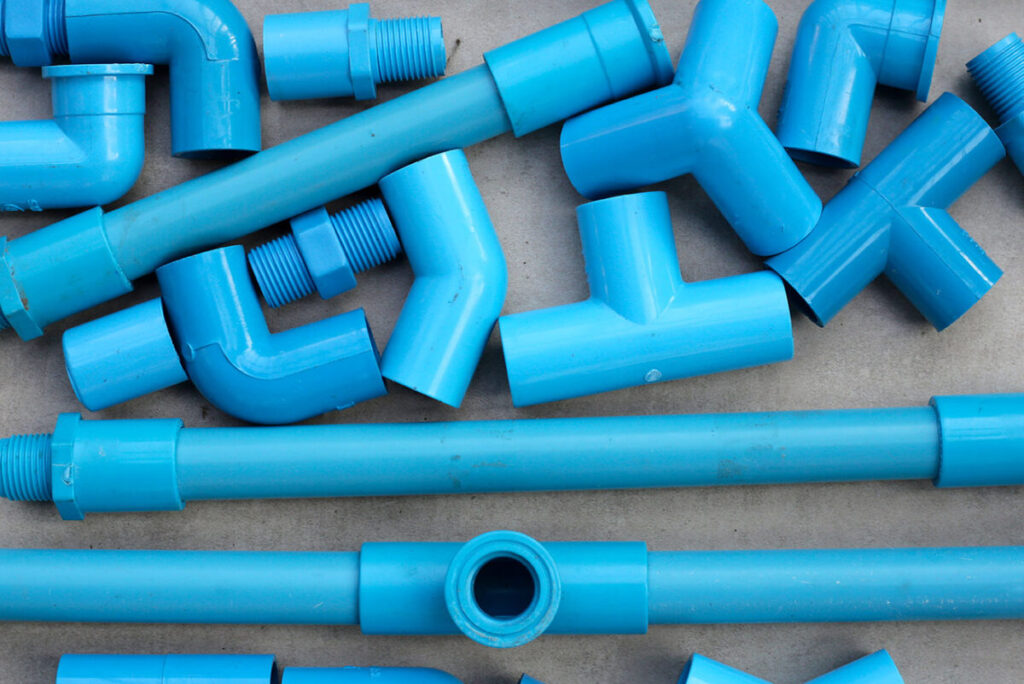