Injection mold fabrication is the process of designing and manufacturing molds used in the injection molding of plastic components. These molds are precision-engineered tools that shape molten plastic into final products. The process involves several technical steps, from design to final assembly and testing.
1. Mold Design
The fabrication process begins with mold design, which is critical to ensuring part accuracy and mold longevity.
CAD Modeling: Computer-Aided Design (CAD) software is used to create detailed 3D models of the mold.
Mold Flow Analysis: Simulation software evaluates how the plastic will flow into the mold, predicting issues like air traps or weld lines.
Design for Manufacturability (DFM): Designers optimize the mold to reduce complexity, cost, and potential defects.
2. Material Selection
Mold materials must withstand high pressure and temperature.
Common materials: Tool steels (like P20, H13), aluminum for prototype molds.
Selection criteria: Durability, thermal conductivity, corrosion resistance, and machinability.
3. CNC Machining
Computer Numerical Control (CNC) machines are used to carve the mold base and cavities from metal blocks.
Rough machining: Removes most of the material quickly.
Finish machining: Provides precision shaping of cavities, cores, and intricate features.
Tolerance: High precision, often within microns.
4. EDM (Electrical Discharge Machining)
EDM is used to create complex geometries and sharp corners that CNC cannot easily machine.
Sinker EDM: Uses a shaped electrode to erode material.
Wire EDM: Cuts through metal using a thin wire and electrical discharge.
5. Heat Treatment
Mold components are heat-treated to improve hardness and wear resistance.
Processes include: Quenching, tempering, and case hardening.
Purpose: Enhances durability and extends mold life.
6. Polishing and Surface Finishing
Polishing the mold cavity is important for part aesthetics and release.
Mirror finish: Used for optical or clear parts.
Texturing: Can be added for grip or aesthetic effects using chemical etching or sandblasting.
7. Mold Assembly
All components are assembled into the mold base.
Includes: Cores, cavities, ejector pins, guide pins, cooling channels, and runners.
Precision: Assembly must ensure perfect alignment and sealing.
8. Mold Testing (T1 Trials)
Before mass production, the mold undergoes testing to evaluate performance.
Trial runs: Test the mold under injection molding conditions.
Inspections: Check for part defects, dimensional accuracy, and cycle time.
Adjustments: Mold may be re-machined or polished for final tuning.
9. Final Approval and Production Release
After successful testing and customer approval, the mold is ready for mass production.
Conclusion
Injection mold fabrication is a complex and precise engineering process. High-quality mold fabrication ensures efficient production, consistent product quality, and extended mold life, which are essential for cost-effective plastic part manufacturing.
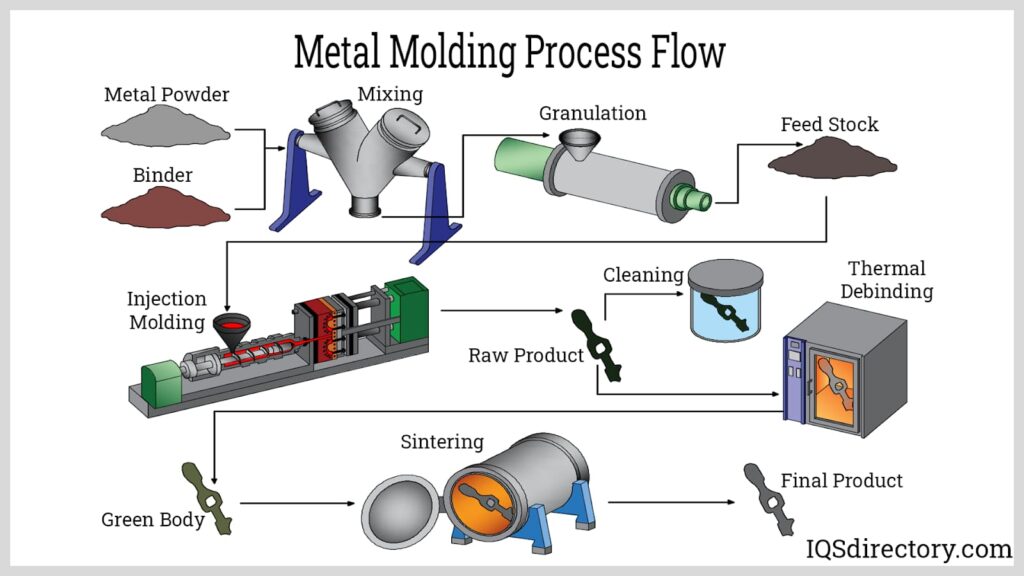